Liquid steel, a term that conjures images of molten metal and blazing forges, represents a crucial component in numerous industries. From automotive manufacturing to construction and heavy machinery, the applications of liquid steel are diverse and expansive. This article delves into the world of liquid steel, focusing on its production, applications, and the innovative technologies surrounding this essential material, while highlighting its reliability and safety to bolster its position in a competitive market.
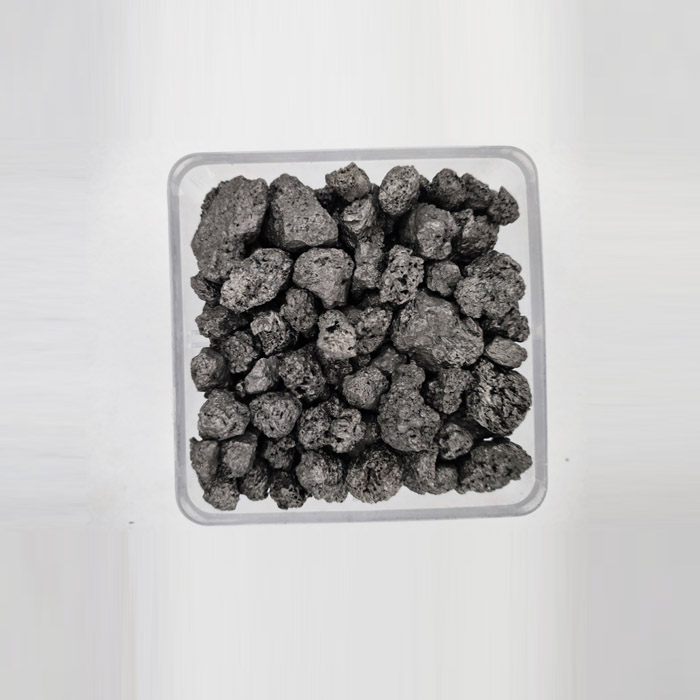
The production of liquid steel is a sophisticated process combining raw materials such as iron ore, scrap steel, and various alloys. At its core, steelmaking involves heating these components to extreme temperatures until they form a molten liquid. The two main methods employed are the basic oxygen furnace (BOF) process and the electric arc furnace (EAF) process. The choice of method depends on factors like the desired steel grade, energy efficiency, and environmental considerations.
Liquid steel's adaptability is one of its most remarkable features. Once in its molten state, it can be cast into various forms to meet specific industrial needs. Continuous casting is a prevalent technique, where molten steel is poured into a mold and rapidly cooled to form semi-finished billets, blooms, or slabs. This versatility in production formats allows manufacturers to tailor liquid steel to a wide range of applications, making it indispensable across numerous sectors.
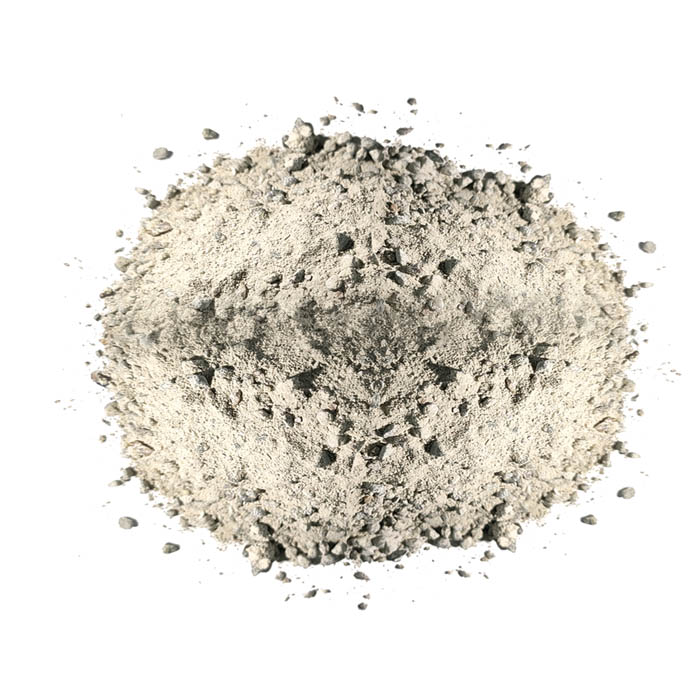
In the automotive industry, liquid steel is the backbone of vehicle manufacturing. Its strength, durability, and fatigue resistance are unmatched, making it the material of choice for critical components such as engine blocks, chassis, and suspension systems. Liquid steel's significance extends to the aerospace domain as well, where it's used in constructing aircraft fuselages and landing gear components due to its superb strength-to-weight ratio. The construction industry also relies heavily on liquid steel for its structural integrity and resilience against natural forces.
Recent technological advancements have propelled liquid steel production into a new era of efficiency and sustainability. Innovative practices are now addressing traditional environmental concerns associated with steel manufacturing, such as high CO2 emissions. The introduction of hydrogen-based reduction processes and carbon capture utilization and storage (CCUS) technologies exemplifies the industry's commitment to reducing its carbon footprint. These pioneering approaches not only enhance the ecological aspects but also optimize the energy consumption of steel production, providing both economic and environmental benefits.
liquid steel
Moreover, the focus on ensuring the highest safety standards in working with liquid steel remains paramount. From modernizing equipment to enhancing operator training and implementing stringent safety protocols, the industry has made significant strides. The implementation of IoT and AI in monitoring and controlling the steelmaking process ensures prompt detection of abnormalities, thereby minimizing the risk of accidents. This emphasis on safety and risk management contributes greatly to the trustworthiness of liquid steel as a reliable material in critical applications.
The expertise and dedication of industry professionals further underscore the authority of liquid steel within its field. Steelmakers possessing decades of experience demonstrate unmatched proficiency in producing high-quality steel, adapting to market needs while ensuring optimal performance. The industry continuously invests in research and development to advance steel technology, support innovation, and maintain its competitive edge. Collaborations with academic institutions and other sectors drive this growth, fostering new developments and unlocking potential applications.
As the global demand for sustainable and high-performance materials grows, liquid steel's role in fulfilling this demand cannot be overstated. Its continuous innovation and adaptability to changing industrial landscapes reinforce its importance as a material. The focus on enhancing its environmental footprint and safety standards is indicative of a forward-thinking approach in a traditionally hard industry. For manufacturers seeking a reliable, high-quality material, liquid steel remains an authoritative choice, fit to meet the evolving needs of modern society.
Ultimately, with its unmatched combination of strength, versatility, and safety, liquid steel parallels a trusted partner in many manufacturing journeys. Its continuous evolution reflects not just an industry solidarity, but a progressive march towards a sustainable and innovative future in material science.