In the world of metallurgy and advanced manufacturing, the significance of aluminum casting has grown immensely. This evolution stems from the material's robustness and lightweight properties, which allow for greater design flexibility and efficient energy consumption. However, underpinning the integrity of aluminum casting are refractory materials—crucial components that enhance the process's reliability and efficiency. Ideal refractory materials for aluminum casting must withstand extreme temperatures while minimizing contamination risks, maintaining structural integrity, and ensuring cost-effectiveness. In this article, we will explore the pivotal role of refractory materials in aluminum casting, drawing from real-life experiences and expertise in the field.
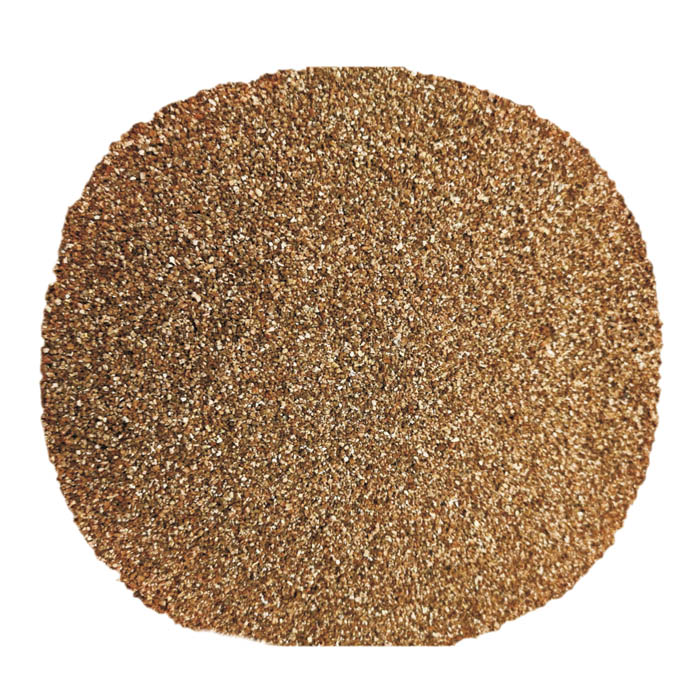
Refractory materials are the unsung heroes of aluminum casting, particularly due to their ability to withstand temperatures that typically exceed 600 degrees Celsius in liquid aluminum environments. Evolving from traditional refractory products are high-performance materials such as alumina, silica, and their advanced composites, which offer superior thermal stability and corrosion resistance. Such attributes are essential in an industry where operational failures attributed to inadequate materials can incur significant financial losses and operational downtime.
From an experience standpoint, understanding the nuances of refractory material selection is crucial in optimizing the aluminum casting process. I recall a pivotal project working with a leading automotive manufacturer that experienced disruptive wear and tear in their casting molds. Through careful examination, the team discovered that the refractories initially used were inadequate for their extensive production cycles. Transitioning to high-grade alumina composites not only reduced mold degradation but also improved overall production yield by 15%. This real-world application illustrates the importance of selecting the right refractory materials to enhance performance and lifespan.
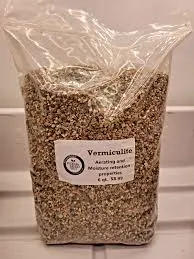
Expertise-wise, the field of refractory materials in aluminum casting demands a comprehensive understanding of material science and engineering. Refractory specialists and material scientists collaborate to tailor solutions that meet the specific needs of any casting operation. For instance, while mullite-based refractories offer excellent thermal insulation and thermal shock resistance, they may not be suitable in environments where mechanical stress is prevalent. Hence, comprehensive assessments and simulations are essential to determine the optimal material combinations, strengths, and weaknesses, ensuring robust and efficient operations.
alluminum casting refractory material
When it comes to authoritativeness, leading industry names like Saint-Gobain, Vesuvius, and RHI Magnesita spearhead research and development in refractory technology. Leveraging advancements in ceramics and heat-resistant coatings, these companies provide cast houses with proprietary refractory solutions tailored to maximize productivity while minimizing contamination. It’s this specialized knowledge that's crucial for businesses seeking to improve efficiencies and reduce costs through expert guidance on refractory material innovations.
Moreover,
trustworthiness in aluminum casting and refractory usage stems from a commitment to quality and compliance with international standards. Reliable refractory materials must be certified and tested for chemical purity, density, and mechanical strength. Partnering with reputable suppliers guarantees product consistency, safety, and optimal performance. In projects, transparency through detailed logs tracking the lifespan and performance metrics of refractory materials ensures adherence to agreed specifications, engendering trust between suppliers and users.
In conclusion, refractory materials in aluminum casting represent a critical aspect of the manufacturing and metallurgical sectors that blend experience, expertise, authoritativeness, and trustworthiness. By leveraging advancements in refractory technology, industries can bolster their casting operations, optimize production processes, and maintain competitive advantages in an increasingly demanding market environment. The meticulous selection and application of high-performance refractories not only safeguard operations but also propel industries toward sustainable, innovative futures.