Basic refractory materials, integral to numerous high-temperature industrial processes, stand at the forefront of innovation due to their exceptional properties that withstand intense heat and chemical attack. These materials, primarily made of magnesia, dolomite, and chromite, are crucial in industries such as steel manufacturing, glass production, and cement kilning. Their robust nature ensures the longevity and efficiency of linings in furnaces and kilns, providing reliable performance under extreme conditions.
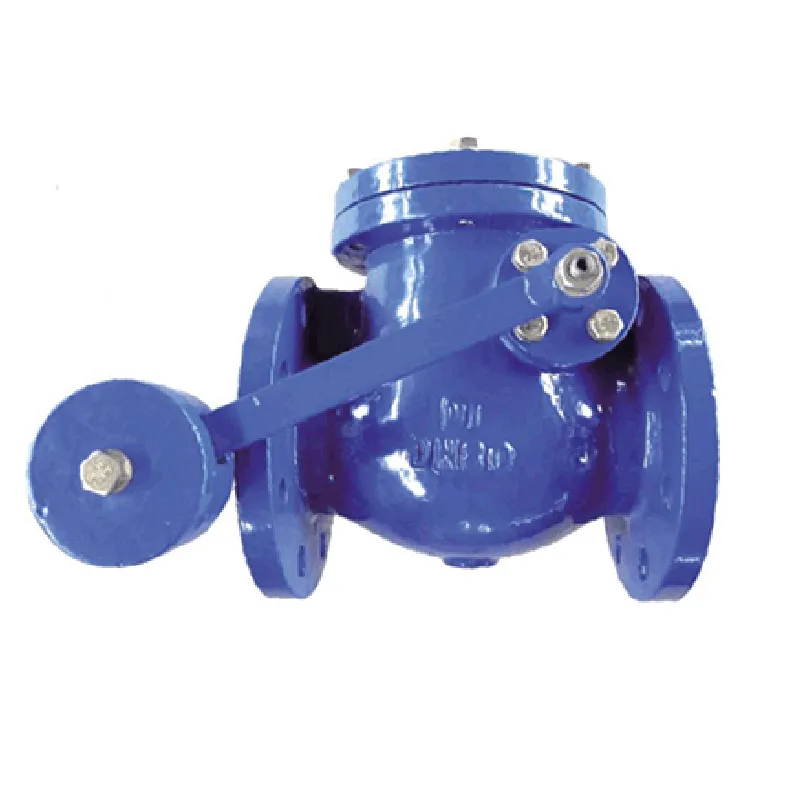
In steel manufacturing, basic refractories are vital in the construction of linings for basic oxygen furnaces (BOFs), electric arc furnaces (EAFs), and ladles. These environments necessitate materials that can endure the grueling combination of high thermal gradients and aggressive slags. Magnesia-based refractories offer superior resistance due to their high melting points and ability to form protective magnesia layers, which interact beneficially with basic slags. This interaction reduces wear and enhances the longevity of furnace linings, ultimately leading to cost efficiencies and uninterrupted production cycles.
In the context of glass production, maintaining purity and preventing contamination are paramount.
Basic refractory materials play a pivotal role in ensuring the quality of glass products. Their resistance to corrosive glass melts and ability to withstand thermal shock make them indispensable in glass tank furnaces. Innovations in basic refractory compositions have led to the development of advanced materials with enhanced corrosion resistance, specifically catering to the unique demands of glass manufacturing. This not only secures the structural integrity of the furnaces but also ensures the consistent quality of the glass produced.
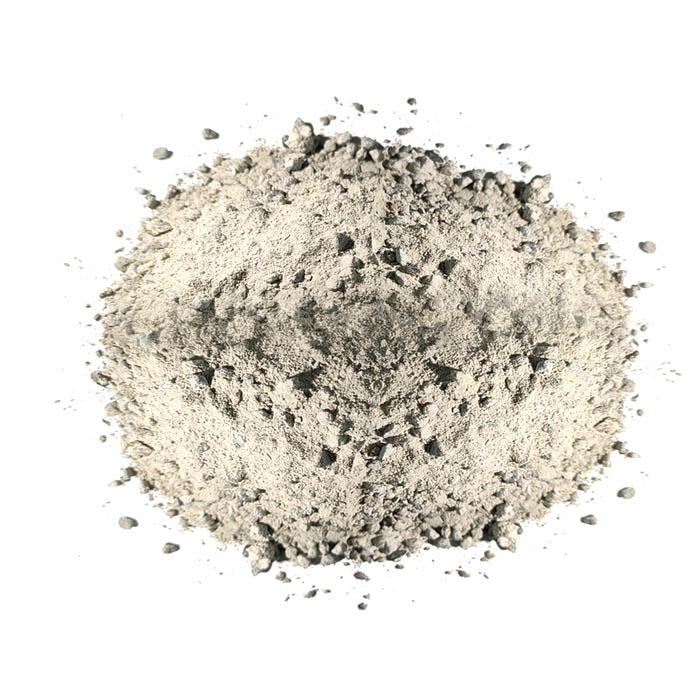
For cement kilns, the role of basic refractories cannot be overstated. These kilns require lining materials that endure high temperatures, chemical interactions with raw materials, and mechanical stress. Dolomite-based refractories are particularly significant due to their compatibility with lime-rich environments and superior resistance to alkali vapors. Recent advancements have focused on improving the thermal insulation properties of these materials, reducing energy consumption and improving the sustainability of cement production processes.
The expertise involved in developing and applying basic refractory materials spans multiple scientific and engineering disciplines. Material scientists work closely with engineers to tailor compositions that meet specific industrial demands. This collaboration has led to groundbreaking improvements in the thermal conductivity, mechanical strength, and chemical resistance of basic refractories. By leveraging cutting-edge technology and exhaustive research, manufacturers can offer solutions custom-fitted to evolve with the demands of modern industry.
basic refractory material
Authoritativeness in the field of basic refractories is bolstered by continuous research and development. Leading industrial players invest heavily in R&D to discover novel mixtures and bonding technologies that enhance refractory performance. These endeavors ensure that basic refractories remain at the cutting edge of technology, meeting the stringent demands of heavy industries while complying with environmental regulations.
Trustworthiness, a critical factor for industries relying on basic refractories, is built through rigorous testing and certification processes. Manufacturers adhere to international standards, ensuring that their products consistently meet the highest quality benchmarks. The integration of advanced diagnostic tools, such as thermal imaging and acoustic emission testing, in the monitoring of installed refractories guarantees early detection of potential failures, facilitating proactive maintenance and prolonging operational lifespan.
The dynamic landscape of basic refractory materials continues to evolve with innovations focusing on eco-friendliness and sustainability. Research into recyclable and environmentally benign refractories is gaining momentum as industries seek to reduce their carbon footprint. Pioneering efforts in this domain promise a future where high-performance materials harmonize with sustainable practices, consolidating the role of basic refractories as indispensable components in industrial advancement.
To conclude, the realm of basic refractories embodies a convergence of experience, expertise, authority, and trustworthiness. These materials not only fulfill critical roles in high-temperature processes but also drive advancements in durability, efficiency, and sustainability. As industries push towards more challenging environments and stricter ecological standards, the development and application of basic refractory materials will undoubtedly remain a cornerstone of industrial progress.