Boiler refractory materials form the backbone of any efficient industrial heating system. Their role is pivotal as they act as the protective barrier that shields the boiler's interior against extreme temperatures, chemical corrosion, and mechanical wear, ensuring durability and efficiency. The evolution of these materials over the decades reflects significant advancements in technology and material science, marking a dynamic journey from basic clay compositions to complex composite structures capable of withstanding the rigors of modern industrial applications.
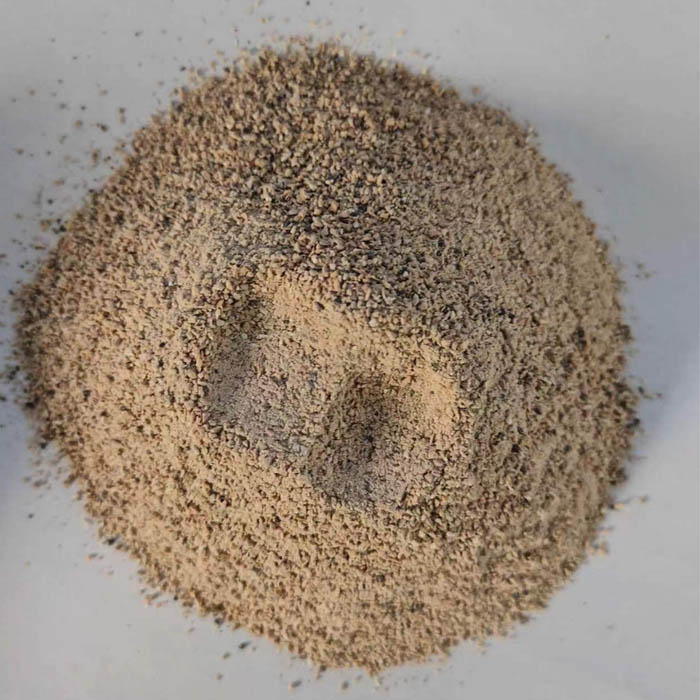
Innovative boiler refractory materials can today be categorized mainly into fireclay, high alumina, silica, and magnesia-refractory materials. Each type boasts specific properties that suit different operational needs, making the selection process critical to boiler efficiency and longevity.
Fireclay refractories have been the traditional mainstay due to their robustness and cost-effectiveness. They comprise alumino-silicate materials and are extensively used because of their ability to withstand moderate temperatures and resist chemical attacks from acidic slags and gases. Nevertheless, they may not be the best for all situations, as they have limitations above certain temperature thresholds and in highly alkaline environments.
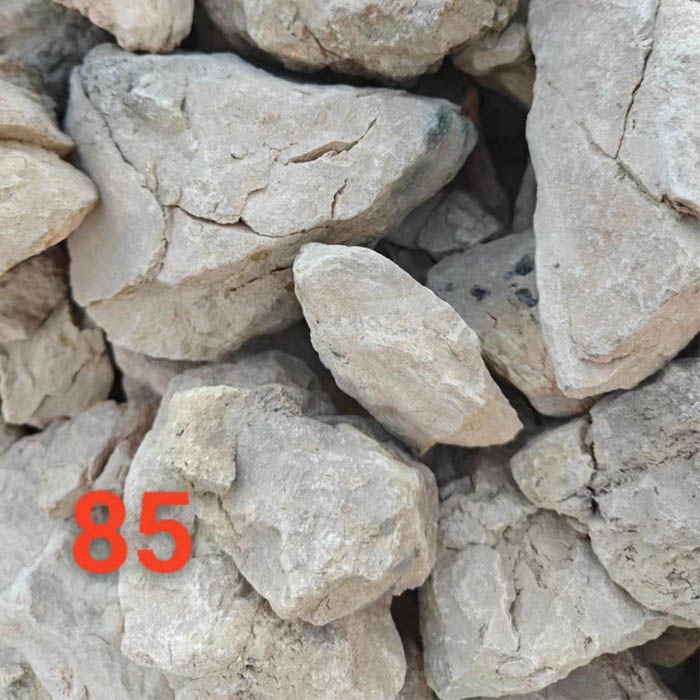
High alumina refractories have garnered significant attention due to their enhanced performance capabilities. Comprising over 45% alumina, these materials provide exceptional resistance to high temperatures, mechanical stresses, and corrosive environments. Industries requiring enhanced refractory lifespan and performance under severe conditions often lean towards high alumina options. This shift highlights how industries prioritize longevity and efficiency over the initial cost.
Silica refractories stand out for their impressive thermal shock resistance and structural integrity at extremely high temperatures, crucial parameters for operations demanding consistent temperature fluctuations. Their use in environments such as glass-making furnaces or other specialized industrial processes demonstrates their versatility. However, their performance can deteriorate in environments where moisture is prevalent, which highlights the need for careful assessment during selection.
Magnesia-based refractories are noted for their alkaline resistance and ability to perform under extreme temperatures exceeding those typically tolerated by other types. The steel industry, among others, values this quality, as processes often involve aggressive materials that would quickly degrade less robust solutions. However, their application requires specific considerations, including the potential for hydration issues, unless experienced handling and preparation techniques are employed.
boiler refractory material
The development of composite refractory materials has introduced a new layer of resilience and adaptability into the market. These composites combine the best attributes of various materials to produce custom solutions tailored to meet specific industrial requisites. The flexibility and innovative engineering behind these composites demonstrate the ongoing commitment to extend operational life and improve thermal efficiency in challenging environments.
Selecting the right boiler refractory material is an exercise in balancing operational demands with material capabilities. Considerations such as the maximum operational temperature, the chemical make-up of slag or exhaust gases, structural stresses, and cost implications are crucial. Relying on expert consultation can bridge the knowledge gap and align material properties with operational goals, reinforcing the essence of proper material selection.
The advent of digital simulation and testing technologies has revolutionized the way engineers approach the refurbishment and installation of refractory materials. Through advanced algorithms and modeling, companies can predict material performance, assess potential points of failure, and optimize refractory design long before implementation. This predictive approach is not only cost-effective but also elevates confidence in the material's ability to perform under real-world conditions.
Furthermore, the importance of regular maintenance and timely inspections cannot be understated. Even the most advanced refractory materials are only as effective as their upkeep. Continuous monitoring for signs of wear, chemical degradation, or mechanical stress ensures that minor issues are addressed before they escalate into major disruptions. Implementing a systematic maintenance protocol not only extends the service life of the materials but also preserves the integrity of the entire boiler system.
In conclusion, the sphere of boiler refractory materials encapsulates both the challenges and triumphs of industrial innovation and engineering expertise. The interplay between traditional knowledge and cutting-edge technology continues to drive the development of more robust, efficient, and tailored refractory solutions. As industries evolve and operational environments grow ever more demanding, so too will the science and application of refractory materials continue to expand, defining the foundations upon which efficient industrial processes depend.