Boiler refractory materials play a crucial role in the performance and longevity of industrial boilers. These materials are essential for maintaining high temperature operations and providing essential insulation. Selecting the right refractory material can lead to increased efficiency, safety, and cost-effectiveness of a boiler system.
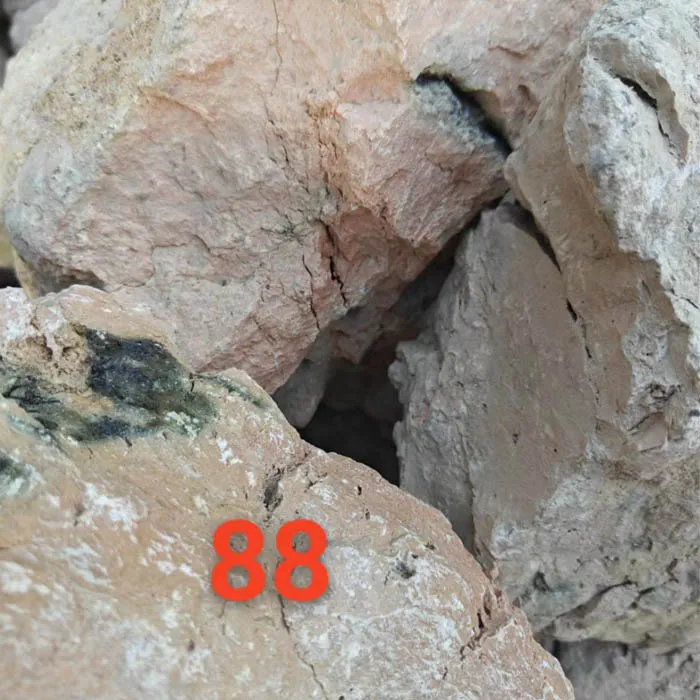
Understanding the Role of Boiler Refractory Materials
Refractory materials are critical for their ability to withstand the extremely high temperatures inside boilers without degrading. They line the interiors of boilers, protecting the steel shell from thermal damage and corrosion. This protection ensures the boiler operates safely, increases its thermal efficiency, and extends its lifespan through reduced wear and tear.
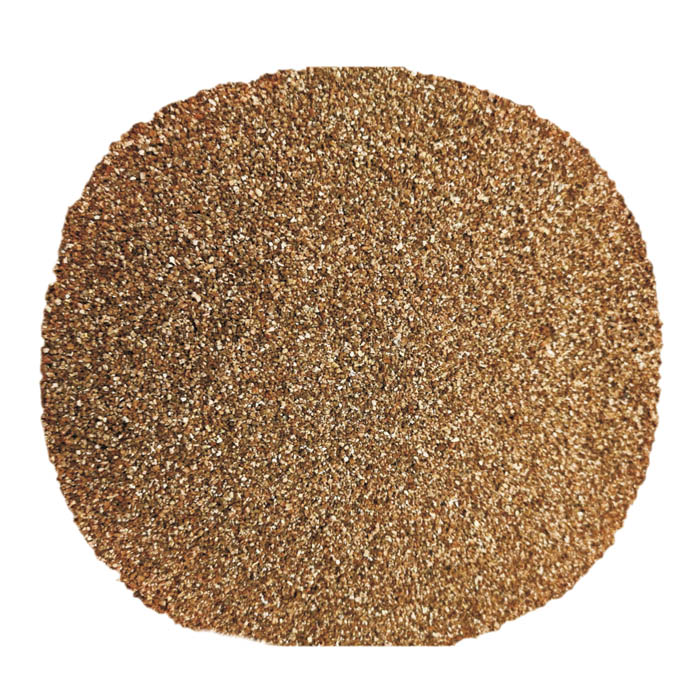
Types of Boiler Refractory Materials
There are several categories of refractory materials used in boilers, each offering unique benefits and features
1. Insulating Refractories Designed to keep heat within the boiler, insulating refractories are lightweight and have low thermal conductivity. They are perfect for applications where minimizing heat loss is critical.
2. Fireclay Refractories Made from aluminous silicate and capable of sustaining temperatures of around 1650°C, fireclay materials are cost-effective and widely used in a variety of industrial applications.
3. High Alumina Refractories These materials contain aluminium oxide (Al2O3) ranging from 50% to 80% and are known for excellent resistance to slag and corrosive environments, making them ideal for harsher conditions.
4. Silica Refractories With high silicon dioxide content, these materials are excellent for applications involving acidic environments and high thermal shocks. They are often used in glass furnaces and coke ovens.
Innovations and Trends in Boiler Refractory Materials
The field of refractory materials is not static; it is constantly evolving. Innovations in material science have led to the development of new materials with better performance characteristics
- Nano-Technologies Utilization of nanotechnology has enabled the development of refractory materials with finer microstructures, offering improved thermal properties, and mechanical strength.
- Composite Refractories Combinations of different types of refractory materials are increasingly used to achieve a balance between cost, durability, and performance, offering tailored solutions to specific industrial needs.
- Environmental Considerations Given the increasing importance of environmental impact, modern refractory materials are being designed to be more sustainable with longer life cycles, reduced energy consumption, and lower production waste.
boiler refractory materials
Selecting the Right Refractory Material
Selecting the appropriate refractory material requires a detailed understanding of the specific operational conditions, including
- Temperature Range Different materials withstand different temperatures. Ensure that the selected refractory can handle the maximum temperatures the boiler will reach.
- Chemical Compatibility Some environments may require refractories with resistance to particular chemicals or slag. Knowing the specific contaminants the boiler will face helps in choosing the right material.
- Mechanical Stress The boiler's size and the pressure conditions it will face should guide the choice of materials with the right mechanical properties to withstand these stresses.
Challenges in Refractory Material Management
Managing refractory materials involves challenges pertaining to installation, maintenance, and inspection
- Installation Accuracy Proper installation is critical to the performance of refractory materials. Poor installation can lead to premature failure and unsafe conditions.
- Regular Maintenance Scheduled maintenance is essential to prolong the life of the refractory lining. This includes regular inspections to detect early signs of wear, such as cracking or spalling, and proactive repairs to maintain integrity.
- Monitoring Technology Employing modern monitoring tools, such as thermal imaging and acoustic monitoring, can help detect issues before they develop into significant problems.
Conclusion
The importance of boiler refractory materials cannot be overstated in industrial applications. The selection, innovation, and management of these materials directly influence the efficiency, safety, and lifespan of boiler systems. Staying informed of the latest advancements and understanding the specific needs of your industrial applications ensures optimal performance and safety.
With new technologies and materials continually advancing, staying engaged with developments in refractory science can provide competitive advantages, ensure compliance with stringent environmental regulations, and promote operational excellence. By prioritizing expertise and trustworthiness, industries can make informed decisions that not only optimize boiler performance but also protect their investment for years to come.