Choosing the right chiller pipe line insulation material is crucial for any industrial or commercial HVAC system. It’s not merely about keeping the chilled water cold; it’s about optimizing energy efficiency, reducing maintenance costs, and extending the longevity of the system. Expertly installed and high-quality insulation material acts as a barrier that not only retains temperatures but also prevents condensation and corrosion, which could otherwise lead to significant damages and costly repairs.
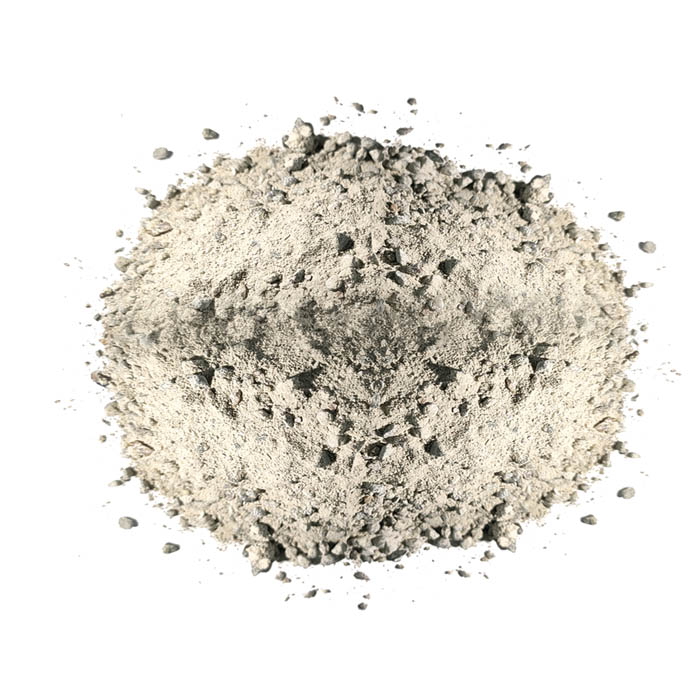
For those seeking an authoritative understanding of chiller pipeline insulation, it's important to first recognize the common materials available and their specific applications. The most popular materials used in the industry include fiberglass, closed-cell elastomeric, and polyethylene foam, each offering its own set of advantages.
Fiberglass insulation is widely recognized for its high thermal resistance and cost-effectiveness. It is typically used in larger diameter pipes due to its ease of application and affordability. From an expert perspective, fiberglass is an excellent choice when the objective is to achieve high thermal efficiency, especially in environments where the pipes are not subjected to harsh mechanical damage.
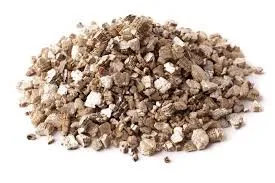
For a more flexible option, closed-cell elastomeric foam stands out. Known for its superior moisture resistance, it’s highly recommended by professionals for environments where piping is exposed to the elements, or where insulation requires a high degree of vibration resistance. This material’s flexibility assists in maintaining the integrity of the insulation around valves and fittings, which are frequent trouble spots for traditional materials.
Polyethylene foam is another prevalent choice among industry veterans due to its low moisture absorption rate and ease of installation. Its lightweight nature doesn’t add excessive weight to the pipe infrastructure, which can be a significant advantage in certain structural settings. For those who prioritize easy maintenance and longevity, polyethylene foam meets those needs efficiently.
chiller pipe line insulation material
Moreover, selecting the correct thickness for these materials cannot be overstated. Insufficient thickness can lead to energy losses while overly thick insulation can become cost prohibitive and unwieldy. Analyzing environmental factors such as humidity, temperature range, and exposure to mechanical wear is paramount in the decision-making process, thereby ensuring the chosen material performs optimally throughout its expected service life.
Authoritativeness in this sector is frequently demonstrated by adherence to industry standards and guidelines, such as those set forth by ASTM International or other relevant bodies. These standards ensure that materials meet stringent safety and performance criteria, providing peace of mind to end users.
Trustworthiness of a selected insulation solution further comes from the vendors and installers involved. Reputable suppliers who provide certified products and experienced technicians ensure that the installation performs as intended, mitigating risks associated with improper application. Regular maintenance checks by qualified professionals support the ongoing performance of the insulation, guaranteeing the system’s efficacy and reducing unexpected costs.
In conclusion, when selecting a chiller pipe line insulation material, it's essential to consider both the material properties and the environmental demands of the system. Trustworthy, expert insight combined with authoritative product standards ensures optimal performance and energy savings, delivering a robust solution that supports the long-term operational success of any chiller system. Whether the choice leans towards fiberglass, closed-cell elastomeric, or polyethylene foam, aligning the material properties with project-specific requirements is key to achieving maximum efficiency and durability.