Cold heading wire stands as a pivotal component in the manufacturing world, especially in the production of fasteners, rivets, and other essential hardware. Its importance cannot be overlooked, as industries ranging from automotive to aerospace depend on this material to construct reliable and durable components. Understanding the nuances of cold heading wire, therefore, becomes indispensable for manufacturers seeking to optimize product performance and longevity.
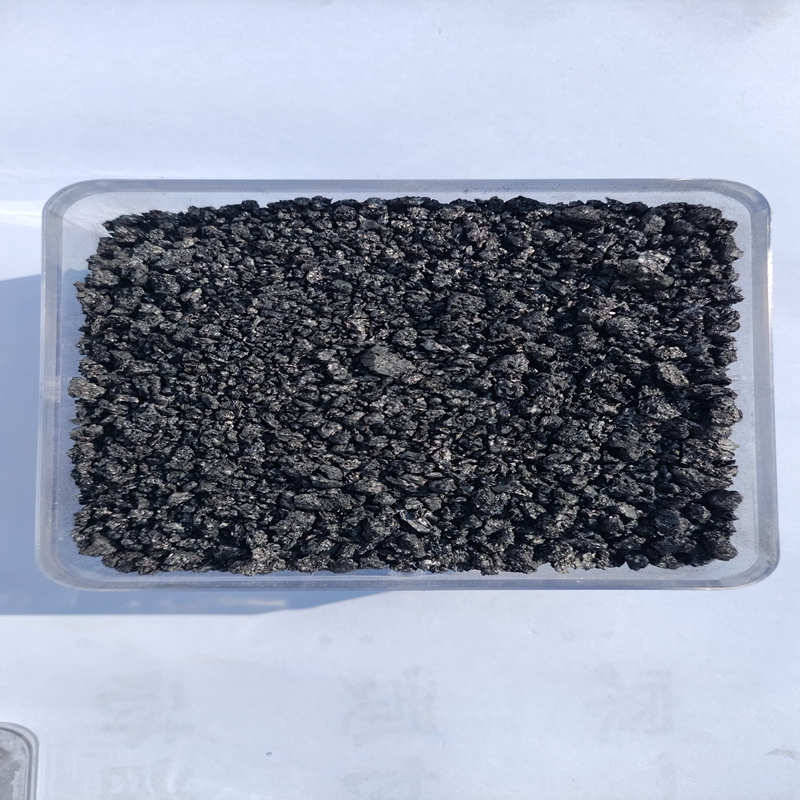
In the realm of manufacturing, expertise in cold heading wire begins with comprehending its intrinsic properties. This wire is engineered to withstand substantial deformation at room temperature, allowing it to be shaped into various configurations without compromising the material's integrity. This unique capability is largely due to the wire's chemical composition and mechanical properties, which are meticulously controlled during production. Typically, cold heading wire is made from carbon or alloy steel, known for their robustness and adaptability. These materials ensure that the wire can endure the stresses of molding processes, resulting in high-quality, precision-engineered final products.
The cold heading process itself is an exercise in precision and expertise. It involves feeding the wire into a header machine where a series of dies and punches systematically compress and shape the wire into the desired form. Unlike traditional machining, which may involve cutting away material, cold heading involves forming, which significantly reduces waste and enhances production efficiency. This technique not only conserves material but also improves the structural integrity of the finished product, making it an economically and environmentally advantageous option for manufacturers. Furthermore, this efficiency extends to how manufacturers can reduce production times and costs, passing these savings onto consumers and maintaining competitive pricing in the market.
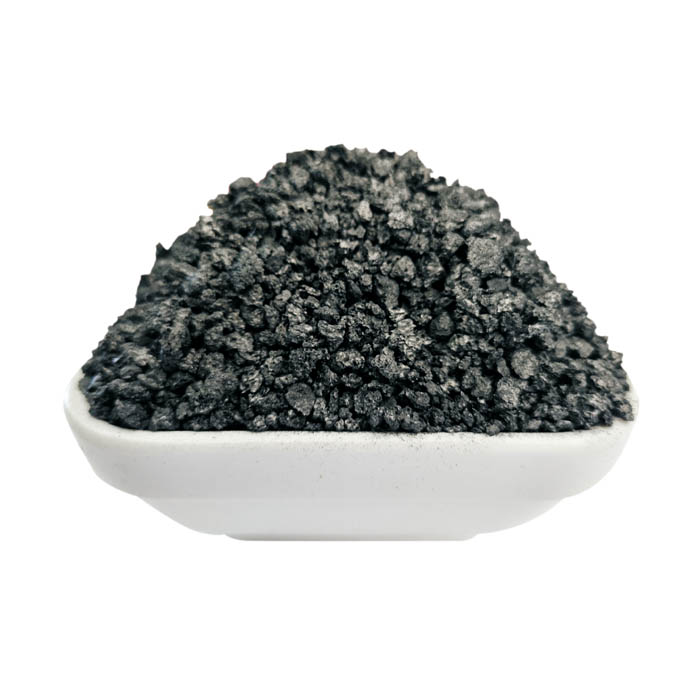
Product performance is significantly influenced by the selection of cold heading wire. For instance, high-performance applications require wires with exceptional tensile strength and surface finish. Hence, manufacturers often involve metallurgical engineers to rigorously test and certify wire quality before it enters production. This layer of quality assurance is crucial for maintaining trustworthiness among consumers, who rely on these assurances for the safety and efficacy of the end products they utilize.
cold heading wire
A notable consideration in cold heading wire operations is the importance of supplier selection. Only reputable suppliers with proven track records should be considered to ensure a consistent supply of wire that adheres to specific industry standards. These suppliers must provide detailed documentation regarding the mechanical properties and chemical compositions of the wire, which acts as an assurance of the material's quality. Partnering with such suppliers bolsters a manufacturer’s authority in the marketplace, reinforcing their reputation for reliability and excellence.
Moreover, handling and storage of cold heading wire requires expert oversight. The wire should be stored in conditions that prevent corrosion, oxidation, or any form of degradation, which might compromise its performance during the heading process. Consequently, facilities must implement stringent climate control measures and regular inspections, ensuring the wire maintains its pristine condition from procurement through to final product creation.
Trustworthiness in the use of cold heading wire is further cemented through continuous innovation and adaptation of the latest technological advancements. The integration of automation and smart manufacturing systems can significantly enhance the precision and repeatability of the cold heading process. Utilizing advanced software for process simulation and quality control can optimize production runs and catch potential issues before they escalate into costly errors. By investing in such technology, manufacturers can assure their clientele of the superior quality and reliability of their products.
Ultimately, cold heading wire remains an essential element in modern manufacturing, blending the finesse of traditional craftsmanship with today’s advanced engineering capabilities. Its continued evolution mirrors the relentless pursuit of excellence in manufacturing technologies. By focusing on acquiring expertise, maintaining high standards of quality, and fostering strong relationships with trusted suppliers, manufacturers can leverage cold heading wire to produce superior products, thereby ensuring customer satisfaction and maintaining a competitive edge in a dynamic market.