Choosing the right cold insulation material for pipes can significantly enhance system efficiency, extend equipment lifespan, and reduce operational costs. Engineers and project managers often face the challenging task of selecting from a multitude of available materials. Understanding the nuances of different options can guide effective decision-making and ensure projects meet both functional and regulatory standards.
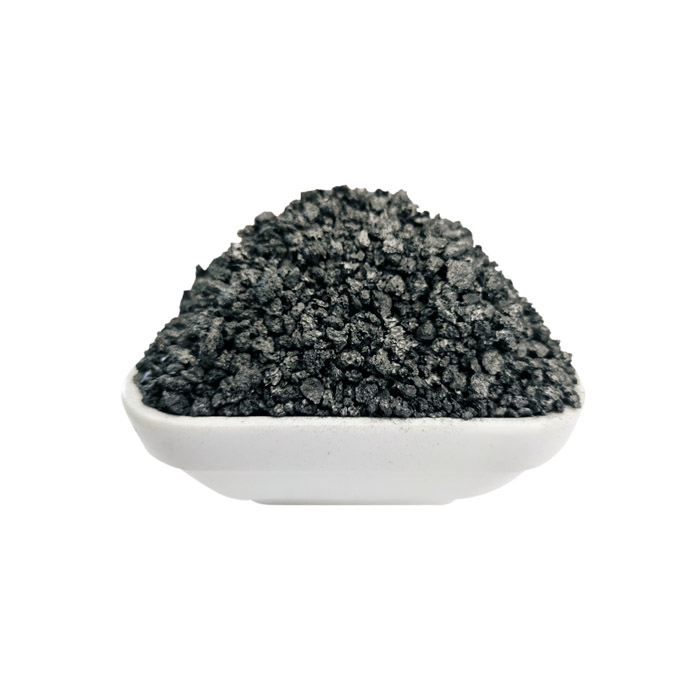
Cold insulation materials serve a critical role in numerous industries, including refrigeration, chemical processing, and food and beverage production. Their primary function is to minimize energy loss and maintain desired temperature levels in piping systems. This not only optimizes operational efficiency but also protects the integrity of the pipes and prevents condensation-related issues.
When selecting insulation materials, performance and durability are paramount. Materials like polyurethane foam, fiberglass, aerogel, and elastomeric foam are widely recognized for their efficiency in cold applications. Polyurethane foam is noted for its exceptional thermal resistance and low thermal conductivity, making it a preferred choice for a wide range of temperatures. It is particularly effective in refrigeration and cold storage applications.
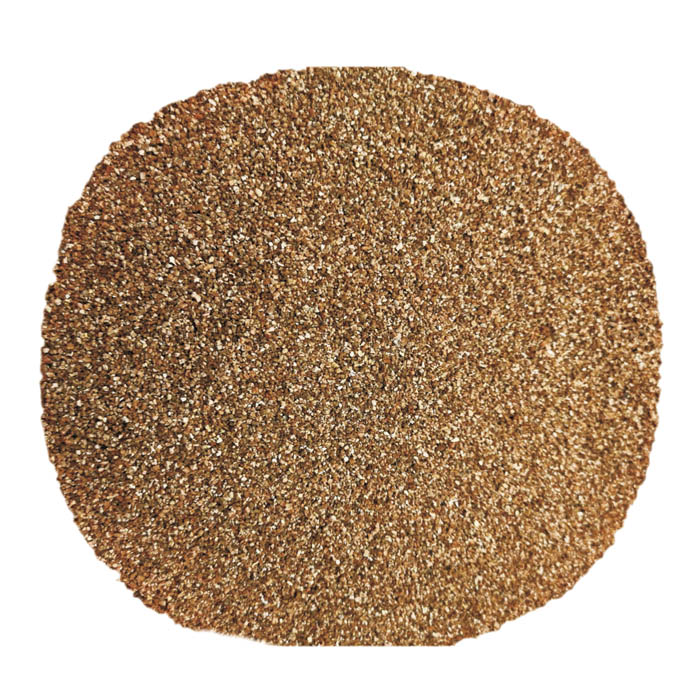
Fiberglass insulation offers excellent resistance to moisture and can maintain performance in environments where condensation is prevalent. Its lightweight nature simplifies installation, but it requires careful handling to avoid skin irritation and inhalation hazards. This material is also cost-effective and provides good thermal and acoustic insulation, making it a versatile choice.
Aerogel insulation, though relatively expensive, provides superior thermal performance due to its ultra-low thermal conductivity. It is an excellent choice for space-limited applications, offering high insulation even in thin layers. The material's hydrophobic properties protect against moisture intrusion, thereby prolonging its lifespan. Aerogel's advanced thermal performance can lead to significant energy savings, justifying its higher initial investment.
Elastomeric foam is another popular material for cold insulation, offering flexibility and ease of installation. Its closed-cell structure makes it resistant to moisture absorption, which is crucial for maintaining consistent performance. Elastomeric foam is ideal for applications requiring flexibility, such as in HVAC systems where vibration damping is advantageous.
cold insulation material for pipes
Environmental sustainability and compliance with regulations are increasingly critical considerations. Many industries are shifting towards insulation materials that minimize environmental impact, both in terms of manufacturing and disposal. Solutions like phenolic foam, which offer low smoke emission and reduced environmental footprint, are gaining traction. Companies must consider these factors not only for regulatory compliance but also to align with global sustainability trends and corporate responsibility.
In addition to selecting the right material, proper installation cannot be overstated. Incorrect installation can compromise the effectiveness of the insulation, leading to energy loss and potential damage to the system. Ensuring that installation professionals are well-trained and adhere to industry best practices is essential to maximizing the benefits of any insulation material.
Technical advancements and innovations continue to emerge in the field of cold insulation. Materials with enhanced features are being developed to cater to the evolving needs of various industries. Innovations focusing on reducing thermal bridging, enhancing moisture resistance, and integrating smart monitoring technologies are transforming the landscape of cold insulation solutions.
Stakeholders must engage with industry experts and collaborate with knowledgeable suppliers who can provide detailed insights and the latest product information. A thorough understanding of the specific environmental conditions and operational requirements is critical in making informed decisions. Reliable partners can aid in navigating the complexities of material selection, ensuring the project’s success and longevity.
Trustworthiness in supplier relationships is vital; choosing providers with a proven track record, transparent dealings, and comprehensive post-installation support can make a significant difference. Organizations that prioritize robust customer support and warranty policies further increase the reliability of their insulation solutions.
In conclusion, the selection of cold insulation materials for pipes involves a multidimensional evaluation of thermal performance, durability, environmental impact, and cost. By focusing on these key factors, businesses can achieve operational efficiency, environmental compliance, and substantial cost savings. As the industry continues to evolve, staying informed about new developments and best practices is imperative for ongoing success and innovation.