Grinding refractory materials represents a critical process in various industrial applications, necessitating a synergy of expertise and experience. As engineers and materials scientists hone their understanding of these procedures, it's crucial to familiarize oneself with the intrinsic qualities and handling of these extraordinary substances. Not just common abrasives, refractory materials are meticulously crafted to withstand extreme conditions without degrading. This offers unparalleled advantages, but it also demands precise grinding techniques tailored for effective utilization.
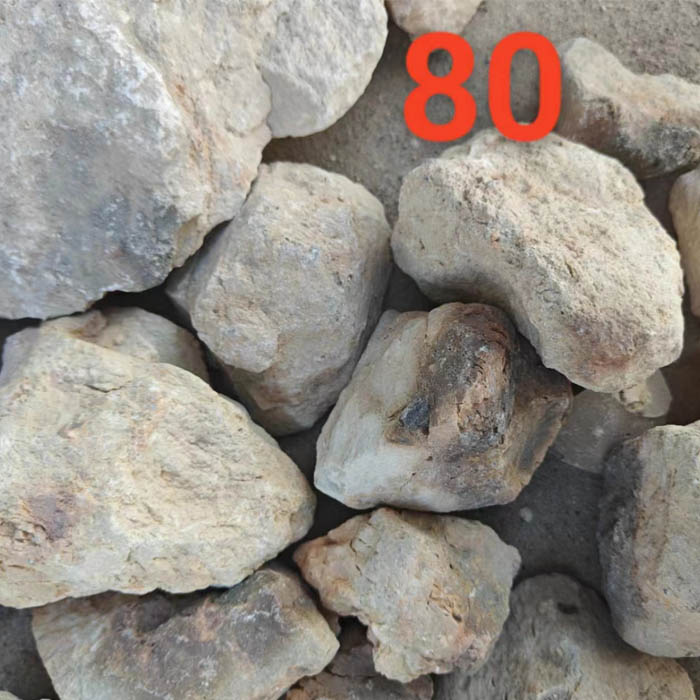
Often employed in high-temperature settings such as kilns, reactors, and furnaces, refractory materials owe their resilience to the high alumina, silicon carbide, and zirconia compositions. These components ensure they withstand thermal shocks, mechanical wear, and chemical corrosion. When tasked with grinding these materials, operators must consider not only the hardness but also the inherent brittleness that could lead to micro-cracking if mishandled. The expertise required to grind these materials begins with understanding the microstructure and the intended end-use.
The initial step in the grinding process involves selecting appropriate grinding tools. The use of diamond grinding tools is prevalent, given their superior hardness and ability to minimize heat generation, which is critical in maintaining the integrity of the refractory material. Additionally, the grinding machine itself must have the capability to maintain high consistency and pressure, ensuring precision in achieving the desired particle size distribution.
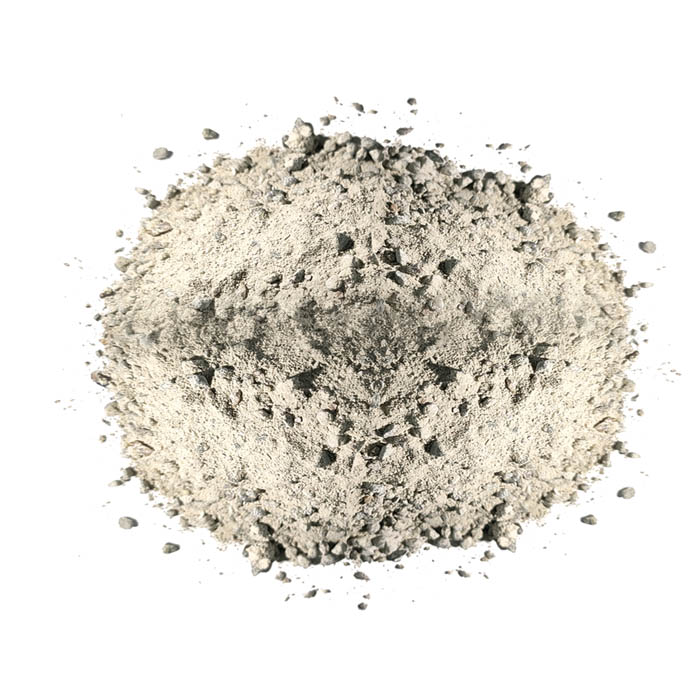
Experience plays a pivotal role when grinding refractory materials, as working with these substances involves an inherent risk-to-reward ratio. A seasoned professional understands the subtle nuances, such as the necessity of regulating speed, pressure, and temperature. For instance, inappropriate speed settings could lead to material overheating, causing modification in structural properties and diminished performance. Achieving optimal grinding results without sacrificing material quality showcases the intersection of skill and knowledge.
grinding refractory material
Expertise is also reflected in the ability to adapt grinding parameters based on the specific type of refractory material in use. Alumina-based refractories may require different approaches compared to silicon carbide or zirconia counterparts. Factors that come into play include the inherent thermal expansion coefficient and porosity levels, which affect how the materials react under the pressure of grinding. Successfully navigating these variables can enhance the material's performance in its final application.
From an authoritative standpoint, contributions from leading industry experts and academic research continuously refine methodologies for grinding refractory materials. These resources provide insights into the latest advancements in grinding technology and innovative techniques for improving efficiency and outcomes. As new refractory compositions are developed, it remains essential for professionals in the field to stay abreast of cutting-edge research to maintain the highest standards of quality and performance.
Trustworthiness underscores every aspect of grinding refractory materials. Authenticating the source of materials is critical, as subpar quality can compromise the safety and functionality of an entire operation. Ensuring the proper certification and traceability of refractory materials alleviates concerns surrounding impurities or defects. Furthermore, documenting the grinding process and maintaining rigorous standards of quality control cultivates confidence among clients, stakeholders, and regulatory bodies.
Ultimately, the grinding of refractory materials is more than a mere mechanical procedure; it is a manifestation of harmonizing science and skill, with each ground granule bearing testament to the meticulous engineering and thoughtful consideration that defines this specialized domain. Professionals engaged in this field are not only crafting materials but are integral players in industries that demand the highest level of performance and reliability. The depth of knowledge and the caliber of craftsmanship required fortify grinding refractory materials as an indispensable component within global industrial frameworks.