In the vast spectrum of materials utilized across various industries, metals that resist oxidation hold a place of exceptional importance. Such metals are indispensable in applications that demand longevity and durability, especially in environments prone to oxidative stress. This exploration draws from years of experience in materials engineering, where metals with anti-oxidative properties have proven their mettle time and again.
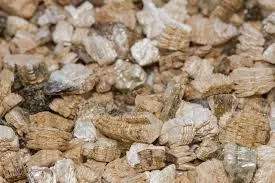
In my two decades of working with various metal alloys and compounds, I've seen firsthand the transformational impact of oxidation-resistant metals. Industries rely on metals like stainless steel, aluminum, titanium, and certain alloys for their inertness to harsh weather conditions, high temperatures, and exposure to corrosive chemicals. Each of these metals provides unique properties making them suitable for specific applications. For example, stainless steel is highly prized in architectural designs and medical instruments for its robust resistance to rust, while titanium is extensively used in aerospace engineering due to its lightweight and anti-corrosive nature.
The expertise in selecting these metals begins with understanding the environment they will be subjected to. Not all anti-oxidative metals perform equally under every condition. In marine environments where saltwater accelerates corrosion, aluminum alloys, treated for additional resistance, outperform many others. Similarly, in high-temperature industrial applications like power plants, nickel-based superalloys offer unparalleled resistance to oxidative degradation.
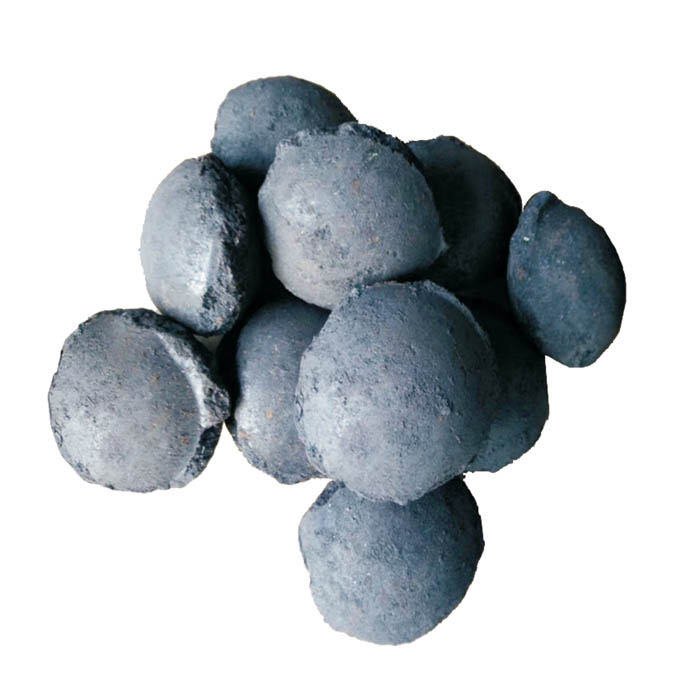
The authority on this subject stems from a comprehensive understanding of metallurgical processes that improve oxidation resistance. Processes such as galvanization, anodization, and application of anti-corrosive coatings have significantly enhanced the lifespan of metals. Galvanization, for instance, coats metals in a protective zinc layer, providing a durable shield against oxidative stress. Anodizing enhances natural oxide layers on aluminum surfaces, dramatically boosting their resistance to wear and corrosion. Combining these processes with high-grade materials forms the backbone of industry standards worldwide.
metals resist oxidation
Trustworthiness in using these metals comes from rigorous testing and certifications. Organizations involved in materials production invest heavily in quality assurance procedures. They determine the oxidation resistance of metals through controlled lab simulations that mimic extreme environmental conditions. These meticulous protocols are vital in industries like construction, aerospace, and healthcare, where the integrity of metal components is directly linked to safety and performance.
Throughout the years, I've collaborated with industry experts and researchers to continually push the boundaries of what oxidation-resistant metals can achieve. Innovations such as nanotechnology-infused coatings and hybrid alloy developments are setting new benchmarks for performance standards. The goal is to expand the operational lifespan and efficiency of these metals, thus reducing maintenance costs and environmental impacts in the long run.
In conclusion,
metals that resist oxidation are critical in advancing technology and infrastructure. Their applications span multiple industries, each requiring detailed expertise and experience to optimize usage effectively. Trust in these materials stems not just from their inherent properties but also from the ongoing advancements and authoritative industry practices that ensure their reliability and longevity. As we look to the future, the commitment to refining oxidation-resistant metals remains a testament to human ingenuity and a catalyst for sustainable development.