Pourable heat setting refractory materials represent a significant technological advancement in industrial and construction sectors where high-temperature resistance is paramount. These cutting-edge materials have been engineered to provide unparalleled performance in environments subjected to extreme thermal conditions, offering both versatility and reliability.
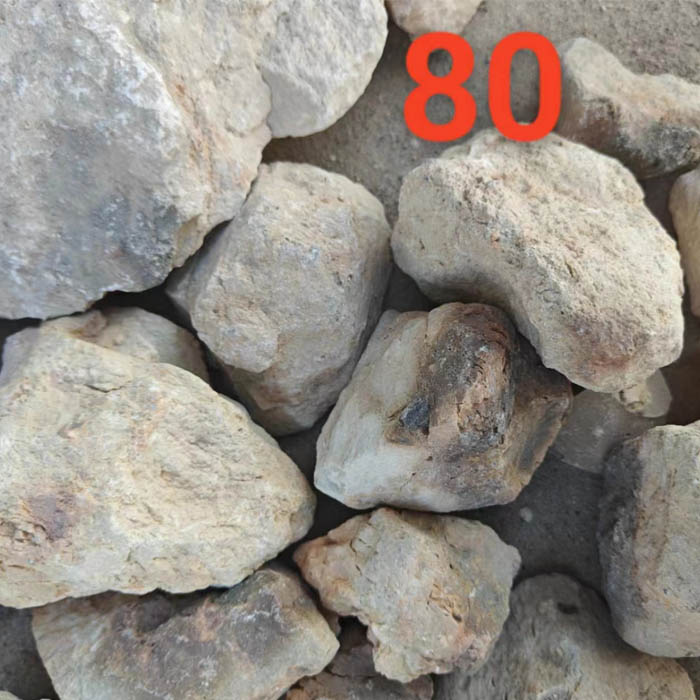
Known for their unique ability to be poured and set at high temperatures, pourable refractory materials have transformed traditional methods of insulation and lining in industries such as metallurgy, ceramics, and power generation. These materials are specifically designed to withstand intense heat while providing robust mechanical strength and thermal insulation, which is critical in both maintaining process efficiencies and protecting infrastructures from heat-induced damage.
When it comes to real-world applications, pourable refractory materials can be seamlessly integrated into various processes. Their fluid consistency before setting allows them to fill complex molds or cracks in existing linings, ensuring an impeccable fit and finish. Once the heat catalyzes the curing process, these materials harden into a solid mass, capable of withstanding temperatures of up to 1700°C or more. This attribute makes them ideal for use in kilns, furnaces, and reactors, where uniform thermal stability is essential.
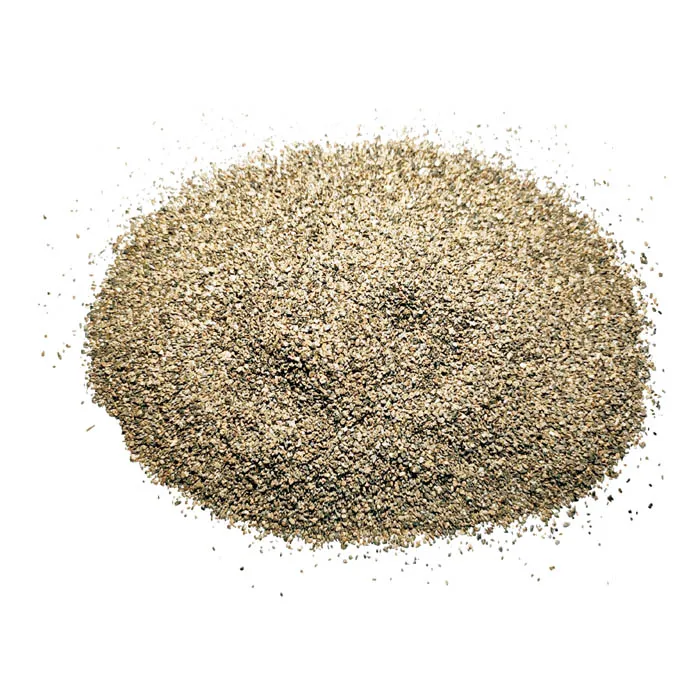
The expertise involved in the development of pourable heat setting refractory materials lies in the precise formulation of their composition. By incorporating advanced binding agents and high-purity aggregates, manufacturers can tailor the physical and chemical properties of these materials to meet specific operational requirements. This customization can include optimizing attributes such as thermal expansion, resistance to thermal shock, and overall durability, which are crucial for high-demand applications.
From an authoritative standpoint, leading producers of refractory materials continuously invest in research and development to innovate and improve product offerings. They collaborate with industry professionals and academic researchers to test and validate the performance of their products, ensuring they meet the highest standards of safety and efficiency. Moreover, these companies often obtain certifications and comply with international standards, such as ISO and ASTM, further solidifying their credibility within the industry.
pourable heat setting refractory material
In practice, choosing the right pourable heat setting refractory material requires a thorough understanding of the specific thermal conditions and mechanical demands of the intended application. Engineers and material scientists often conduct detailed analyses, including thermal simulations and stress testing, to determine the most suitable composition and installation method, thereby maximizing the material's lifespan and performance.
Providing reliable solutions, these materials are integral to operations in harsh environments. Companies that invest in high-quality refractory solutions often experience improved energy efficiency due to reduced heat losses and minimized downtime caused by material failure. This not only enhances operational productivity but also contributes to sustainable practices by lowering overall energy consumption.
For businesses considering incorporating pourable refractory materials into their processes, aligning with trusted suppliers is paramount. A reputable supplier will provide not only the material but also the technical support needed for successful installation and maintenance. This includes offering guidance on best practices, such as the appropriate mixing ratios, pouring techniques, and curing requirements, which are vital to achieving optimal performance.
Ultimately, the trustworthiness of pourable heat setting refractory materials is derived from their proven track record in demanding environments and the continuous advancements driven by leading experts in the field. As industries evolve, these materials remain a cornerstone in achieving resilient and efficient high-temperature operations, securing their place as an indispensable component in modern engineering solutions.