Refractory materials play a crucial role in a wide range of industrial applications, from steel manufacturing to the production of ceramics. As high-temperature resistant materials, they ensure the safety and efficiency of processes that require extreme heat. This article explores the unique attributes and advantages of refractory materials, offering real-world insights and industry expertise to highlight their critical role in various applications.
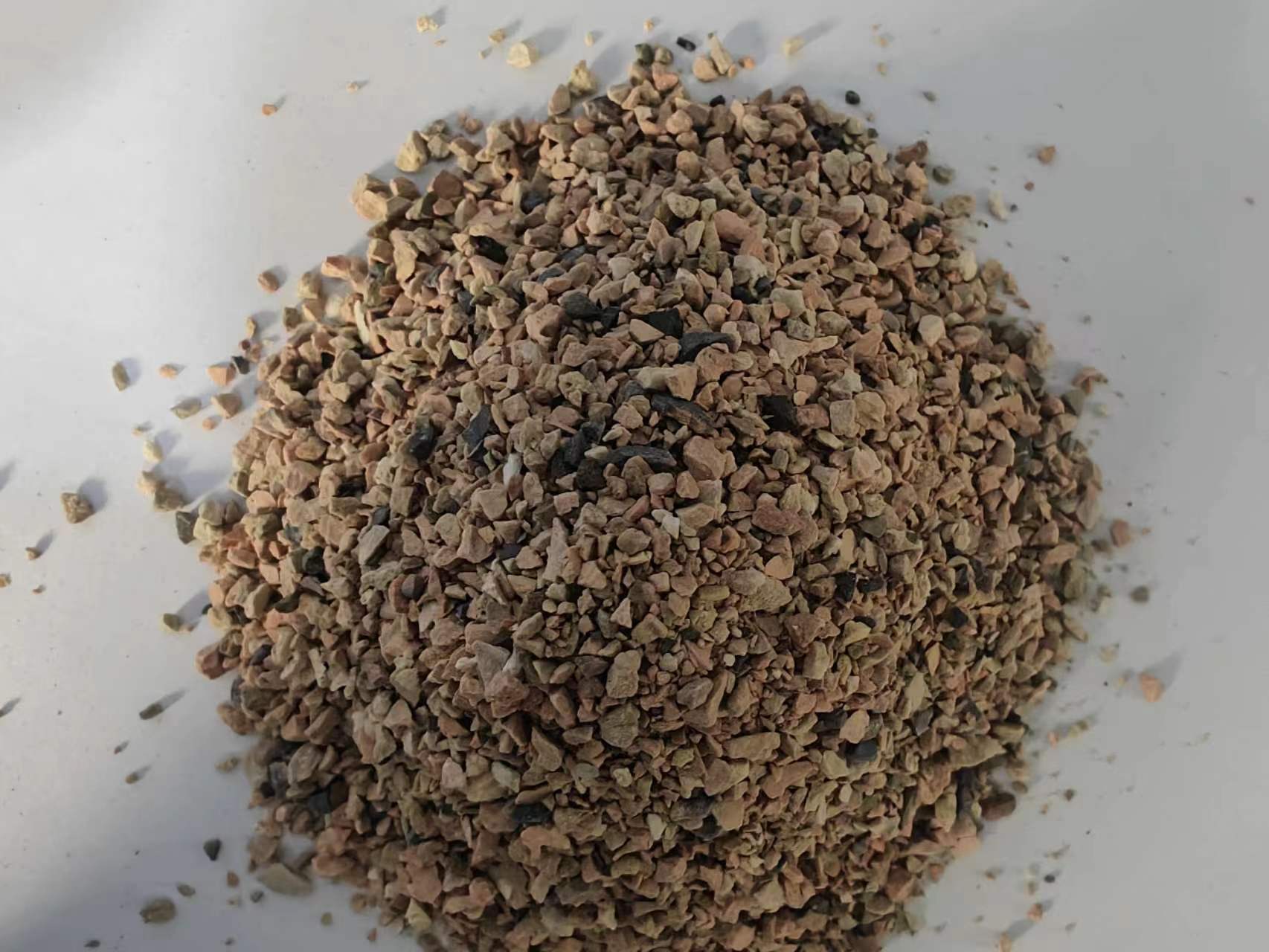
Refractory materials are engineered to withstand temperatures exceeding 1,000°C, making them indispensable in industries where processes occur at exceedingly high temperatures. High thermal resistance is achieved through the use of compounds such as alumina, silica, magnesia, and zirconia. These compounds are selected for their ability not only to resist high temperatures but also to maintain structural integrity and thermal stability under extreme conditions.
One of the leading industries dependent on refractory materials is steel manufacturing. The production of steel requires furnaces that operate at temperatures surpassing 1,600°C. In this scenario, refractories are used to line furnaces and ladles, ensuring the containment of molten metal. Companies relying on quality refractory products maintain not only efficiency but also prioritize safety by minimizing the risk of furnace and ladle failures.
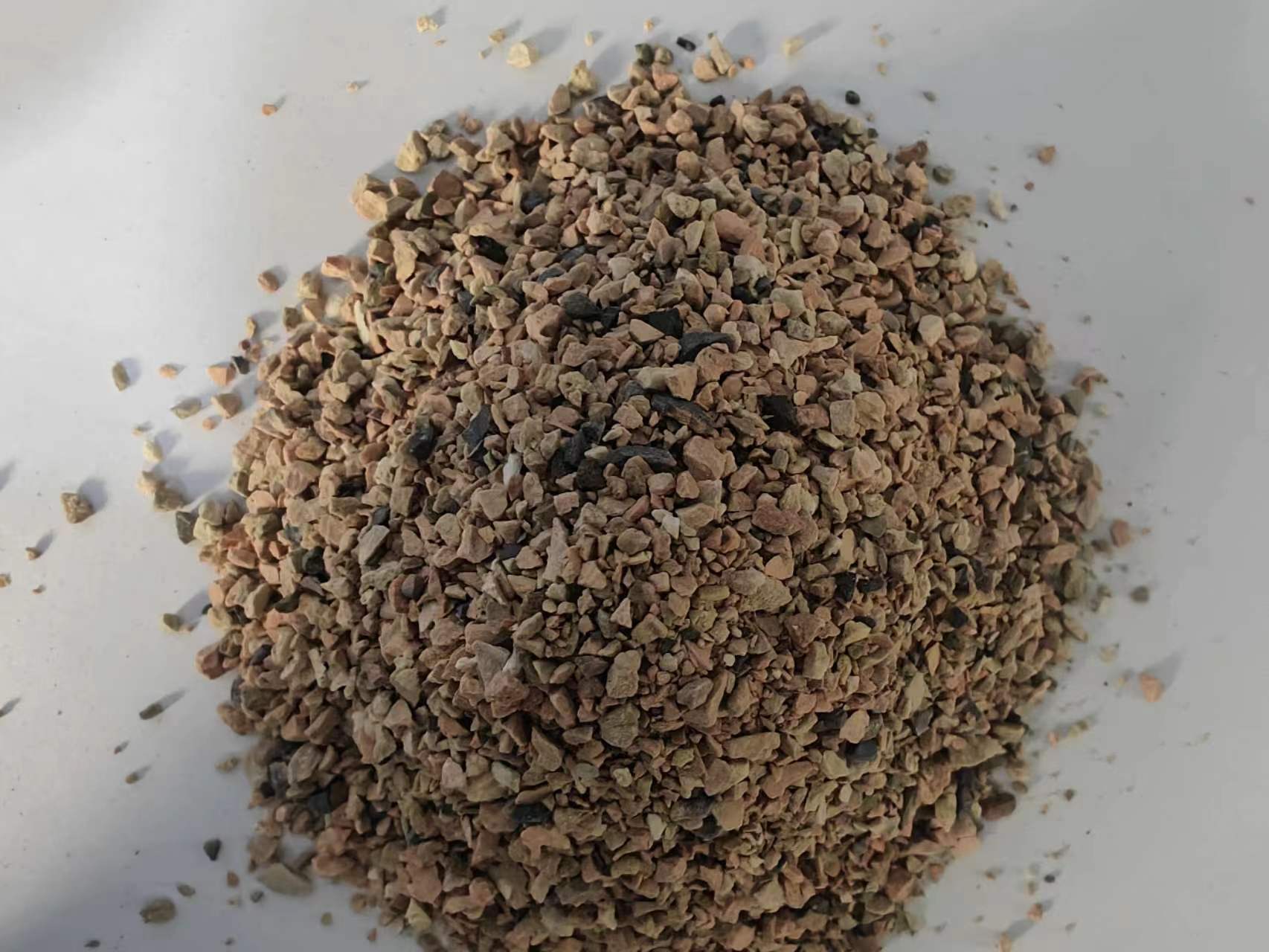
Another critical application of refractory materials is found in the production of cement. During the cement-making process, kilns lined with refractory bricks facilitate the transformation of raw materials into clinker at temperatures that can reach 1,450°C. Without high-grade refractories, kilns would suffer from wall erosions and reduced lifespan, culminating in significant downtime and maintenance costs.
The glass industry also showcases the importance of refractories. Consistent production of high-quality glass demands that melting tanks are reliable over long periods. Refractory linings in these tanks endure continuous high temperatures and corrosive environments caused by molten glass. The ability of refractories to withstand these harsh conditions ensures both product quality and operational efficiency.
refractories material
Innovative advancements in refractory materials have led to the development of specialized products tailored for niche applications, including the aerospace industry. Here, refractory metals such as tungsten and tantalum are used for their extraordinary thermal shock resistance and stability under extreme conditions found in rocket engines and spacecraft.
Application-specific innovations also underscore the importance of ongoing research and development within the field of refractories. Nanotechnology, for example, is being harnessed to enhance the performance of refractory materials, offering improved resistance to wear and tear, higher insulation properties, and overall cost-effectiveness.
The selection of appropriate refractory materials relies heavily on expertise and precise understanding of the operational environment. Factors such as thermal conductivity, thermal expansion, and chemical compatibility must be thoroughly considered to ensure that the chosen material meets the specific demands of its application. Consulting with industry experts and relying on reputable suppliers ensure that these materials offer the best performance and longevity.
Trust in refractory materials is established through rigorous quality control and certification processes. Leading manufacturers adhere to international standards, conducting comprehensive testing to confirm the resilience and performance of their products. Companies that prioritize certified products not only gain a competitive edge but also earn the trust of clients in sectors where reliability is non-negotiable.
In summary, refractory materials are vital for the continued advancement and safety of industries operating at high temperatures. Their evolution, driven by scientific and technological progress, emphasizes the continued importance of expertise and innovation. Industries must work closely with trusted suppliers to source materials that meet the highest standards, ensuring operational efficiency, safety, and reliability across various high-temperature applications.