Refractory Lining Materials A Key Component in Industrial Manufacturing
Refractory lining materials, the unsung heroes of high-temperature industrial processes, play a pivotal role in manufacturing industries worldwide. These specialized materials, designed to withstand extreme heat and corrosion, are manufactured by companies that understand the intricate balance between durability, thermal resistance, and operational efficiency.
Manufacturers of refractory lining materials are at the forefront of innovation, constantly developing new compositions and technologies to cater to the diverse needs of various industries. From steel production to cement manufacturing, power generation, and even glass and ceramic industries, these linings serve as a protective shield, ensuring the integrity and longevity of equipment operating under severe conditions.
The refractory lining material is primarily composed of refractory bricks, monolithics, and castables. Refractory bricks, made from alumina, silica, magnesia, or a combination, form the backbone of many furnace linings due to their exceptional heat resistance. Monolithics, on the other hand, are castable mixes that can be applied in a variety of shapes and sizes, offering flexibility in installation. Castables, with their high strength and resistance to wear, are ideal for areas subjected to mechanical stress.
Manufacturing these materials involves precise formulation and processing techniques. Raw materials, often mined minerals, are crushed, sieved, and blended in exact proportions. The mixture is then shaped, either through pressing for bricks or casting for monolithics, followed by drying and firing at high temperatures to achieve the desired refractoriness. Advanced manufacturing facilities utilize computer-controlled systems for consistency and precision Advanced manufacturing facilities utilize computer-controlled systems for consistency and precision
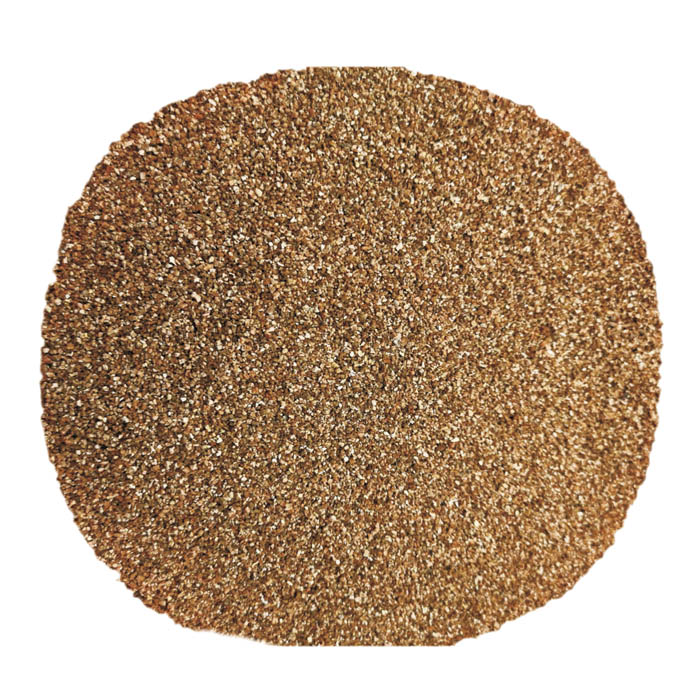
Advanced manufacturing facilities utilize computer-controlled systems for consistency and precision Advanced manufacturing facilities utilize computer-controlled systems for consistency and precision
refractory lining material manufacturer.
Refractory lining manufacturers also focus on developing eco-friendly and energy-efficient solutions. For instance, lightweight refractories, made from porous aggregates, reduce fuel consumption by minimizing the weight of the furnace. Furthermore, they work on enhancing the insulation properties to minimize heat loss, contributing to energy conservation.
Innovations in refractory lining materials have significantly impacted the performance and sustainability of industrial operations. The introduction of high-alumina and chrome-based refractories has improved resistance to chemical attack and slag, while the use of fiber-reinforced materials has enhanced mechanical strength.
However, the selection of the right refractory lining material is crucial, as it directly impacts process efficiency and equipment lifespan. Manufacturers collaborate closely with clients, understanding their specific requirements, operating conditions, and budget constraints to provide tailored solutions.
In conclusion, refractory lining material manufacturers are more than just producers; they are partners in ensuring the smooth and efficient functioning of high-temperature processes. Their commitment to research, development, and customization is testament to their vital role in the global manufacturing landscape. As industries continue to evolve, so too will the world of refractory lining materials, promising a future of enhanced performance, durability, and environmental responsibility.