Refractory board materials serve as essential components in multiple industrial applications, ensuring safety and longevity in high-temperature environments. These boards are engineered to withstand extreme conditions, making them crucial in industries ranging from metallurgy to energy production.
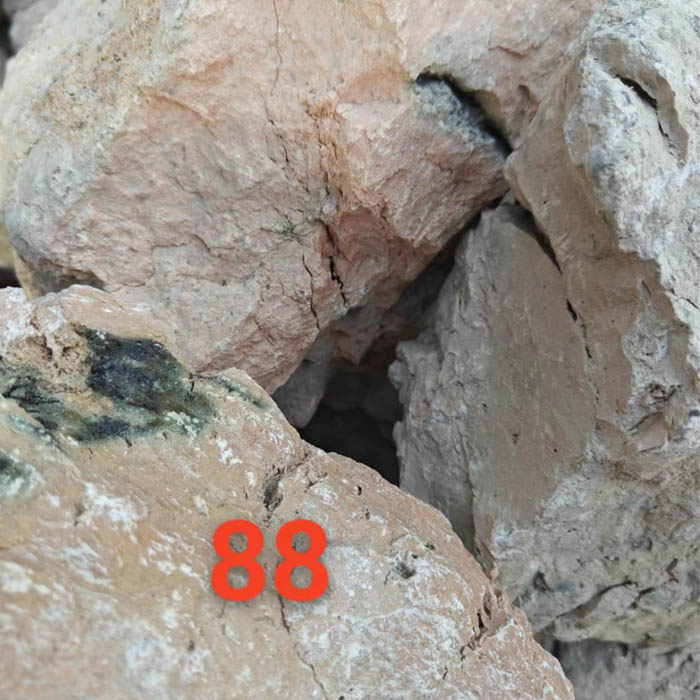
Experience is the first pillar to consider when understanding the significance of refractory board materials. Across various projects, these boards have consistently proven their ability to provide thermal insulation and structural support. One notable application involved their use in a steel manufacturing facility,
where refractory boards lined the interior of blast furnaces. The boards successfully shielded the furnace walls from temperatures exceeding 1600°C, significantly extending the lifespan of the furnace and enhancing safety for operators. This real-world success story highlights their indisputable value in high-stress environments.
In terms of expertise, refractory board materials are distinguished by their unique composition. Typically, they are made from high-alumina cement, silica, or calcium silicate, each offering specific benefits depending on the application. For instance, boards with a high percentage of alumina are ideal for areas exposed to particularly high temperatures, as they offer excellent thermal stability. Moreover, advancements in manufacturing have led to the development of boards with reduced thermal conductivity, resulting in even more efficient insulation properties. These innovations reflect ongoing research and development efforts that continue to refine the effectiveness of refractory boards.
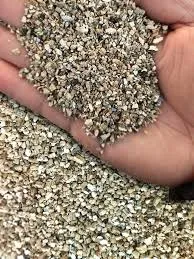
refractory board material
Authoritativeness is demonstrated by the widespread industry recognition of refractory board materials. Organizations such as ASTM International have established standards governing their manufacture and use, ensuring consistency and reliability. Furthermore, the expertise of professionals in materials science and engineering underpins the rigorous testing and quality control processes that refractory boards undergo. This authoritative oversight provides assurance that these materials meet the high standards expected in demanding industrial settings.
Trustworthiness is built over time, stemming from repeated successful deployments of refractory board materials. Companies specializing in refractory solutions often provide extensive warranties and support, underscoring their confidence in the longevity and performance of their products. The trust placed in these materials by industry leaders is further evidenced by their inclusion in critical infrastructure projects. For instance, when constructing state-of-the-art power plants, engineers often specify refractory board materials for lining turbines and heat exchangers, ensuring optimal function and durability.
In conclusion, refractory board materials are indispensable in environments that demand high-temperature resilience and insulation. Their development is rooted in a profound understanding of materials science, supported by extensive industry expertise. Recognized for their reliable performance and subject to stringent quality assurance standards, these materials continue to earn trust across industries worldwide. Whether in protecting furnace linings in steel production or ensuring thermal efficiency in power plants, refractory board materials remain a cornerstone of industrial safety and efficiency.