Refractory bricks, essential components in industries like steel, glass, and cement, face intense heat and harsh environments. The quality and composition of raw materials used in manufacturing these bricks significantly influence their performance. Selecting the right raw materials is crucial for optimal results in high-temperature applications.
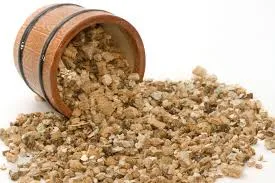
Refractory bricks primarily contain materials that can withstand high thermal stress.
Alumina and silica are two key raw materials. Alumina, derived from bauxite, is valued for its high melting point, corrosion resistance, and strength at elevated temperatures. Silica, sourced from high purity quartz, offers excellent thermal stability, which is vital for industries with fluctuating temperature conditions. A deep understanding of alumina and silica properties is essential for manufacturers to optimize these materials for specific uses.
Additionally, magnesite, a mineral composed chiefly of magnesium carbonate, is another critical raw material. Its primary attribute is its ability to withstand chemical erosion in high-temperature settings, making it ideal for steel-making furnaces. Pairing magnesite appropriately with other raw materials can enhance brick performance.
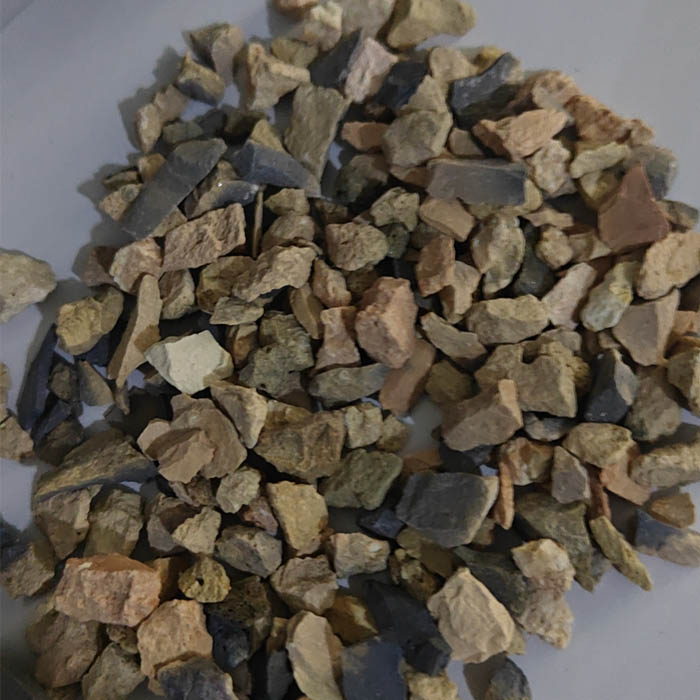
Clay, specifically kaolinite, often serves as a binding agent in refractory bricks. It's crucial not solely for its bonding capabilities but for its low thermal conductivity, which enhances the brick's insulating characteristics. When selecting clay, assessing its plasticity and chemical composition ensures compatibility with other raw materials, thus optimizing the manufacturing process.
The importance of zircon is growing because of its resistance to molten metal and glass. This material is especially favored in glass manufacturing. Its high density and low thermal expansion rate make it a formidable barrier against corrosion and thermal shock.
refractory bricks raw materials
To ensure the highest quality refractory bricks, it’s imperative to focus on the purity of these raw materials. Impurities can lead to structural weaknesses. Sophisticated testing and quality assurance processes, such as X-ray fluorescence (XRF) and scanning electron microscopy (SEM), can identify these impurities before they compromise the final product.
Another emerging trend in this industry is the use of alternative and recycled raw materials. As industries strive towards sustainability, incorporating materials like recycled alumina and silica not only reduces costs and conservation efforts but also lowers environmental impact. These recycled materials, when processed correctly, do not compromise brick quality and can enhance properties like thermal resistance.
The expertise required in formulating these materials relies on a profound understanding of the chemical interactions that occur under high temperatures. Integrating advanced technological processes in the development phase enables manufacturers to create highly specialized bricks tailored to specific industrial needs. Collaborating with material scientists and engineers can further refine the composition and achieve superior performance standards, thereby improving product reliability and lifespan.
Establishing trustworthiness in the market involves maintaining transparency about sourcing and the manufacturing procedures of these materials. Certifications from authoritative bodies in refractory technology can reinforce a brand’s credibility. Consumers respect and prefer suppliers who emphasize consistent quality and invest in research and development to stay ahead of industry trends.
In conclusion, the mastery of refractory brick raw materials lies at the intersection of traditional knowledge and modern innovation. By valuing the expertise in material properties, manufacturing techniques, and cutting-edge research, companies can create high-performance bricks that not only meet but exceed industry standards. Emphasizing quality assurance and sustainable practices not only bolsters a company's competitive edge but also fosters trust in global markets, ensuring a pivotal role in future high-temperature applications.