Refractory kiln lining materials play a pivotal role in industries ranging from metallurgy to ceramics, ensuring efficiency, safety, and longevity in high-temperature operations. With an emphasis on the latest innovations and industry standards, understanding the true potential of these materials requires a thorough grasp of their applications, benefits, and advancements.
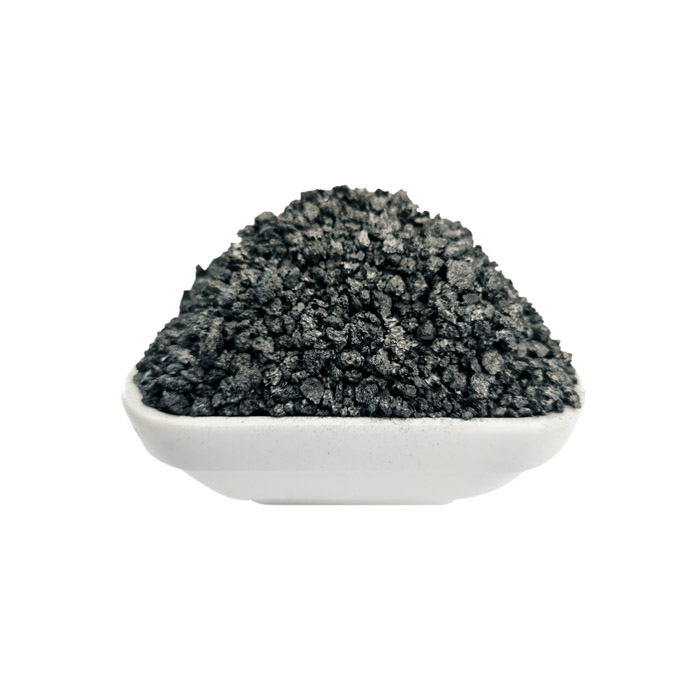
Refractory materials are engineered to withstand not just intense temperatures, but also the chemical and physical wear that comes with industrial kiln operations. These materials are crucial as they protect the kiln's structure, maintain thermal efficiency, and ensure product quality. This holistic approach underscores the importance of expertise when selecting the right refractory material.
There are several categories of refractory kiln lining materials, each designed to cater to specific needs of industrial operations. Among these, the most commonly used are brick-based linings, castables, and ceramic fibers. Each type possesses unique properties that suit different environments and applications.
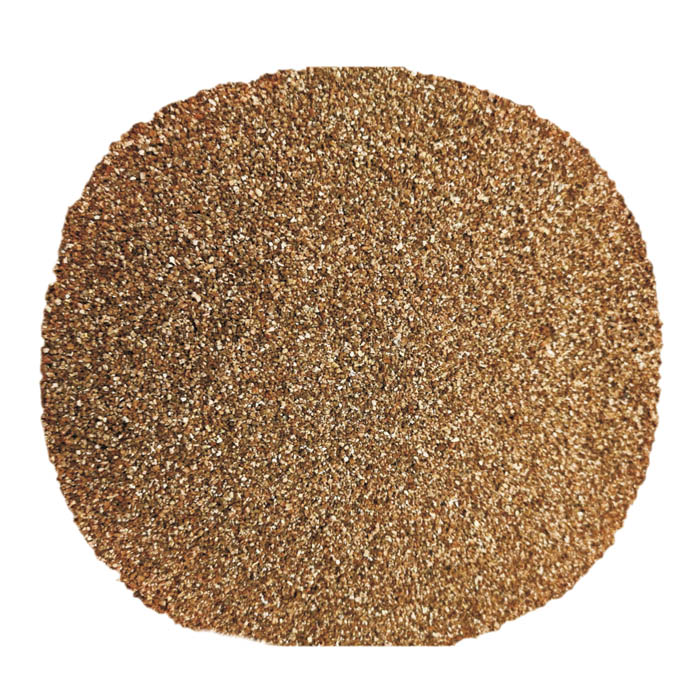
Brick-based linings are traditionally used for their durability and capacity to hold up under severe thermal cycling and mechanical stress. These bricks are composed of alumina, silica, fireclay, or a combination thereof, allowing them to deliver exceptional performance in high-temperature ovens and kilns used in steel and glass production.
Castables are a versatile category of refractory materials, comprising a mix of refractory aggregates, bonding agents, and admixtures. These materials provide enhanced thermal insulation and are particularly favored for their ability to be molded into complex shapes that fit unique industrial settings. High-quality castables exhibit low thermal conductivity, reducing heat loss and improving energy efficiency.
Ceramic fibers represent the cutting-edge in refractory technology, offering lightweight insulation with excellent thermal stability. These materials facilitate quick kiln heat-ups and cool-downs, optimizing productivity and operational flexibility. Their installation is straightforward, significantly reducing downtime while ensuring comprehensive coverage, even in hard-to-reach areas.
refractory kiln lining material
The evolution of refractory kiln lining materials is closely tied to innovations in material science. Recent advancements have focused on increasing the service life of these linings, enhancing their resistance to corrosion and mechanical wear. Research in developing non-wetting mixes, particularly for non-ferrous metal processing, has yielded impressive results, minimizing downtime and maintenance costs.
Expertise in the selection and installation of refractory materials is fundamental to harnessing their full potential. Incorrect installation can lead to premature wear and energy inefficiencies, costing businesses significantly in terms of both repairs and energy consumption. Partnering with experienced industry professionals ensures that the specific thermal, chemical, and mechanical demands of your operation are met, safeguarding both investments and production timelines.
Authoritativeness in the field of refractory materials is established through adherence to international quality standards and certifications. Ensuring that the materials comply with standards such as ASTM, ISO, or other relevant bodies underpins their reliability and performance. Manufacturers committed to these standards demonstrate a dedication to offering superior products, engendering trust among consumers and industry partners alike.
Finally, trustworthiness in the context of refractory kiln lining materials extends beyond product quality to encompass ethical sourcing, environmental responsibility, and customer support. Reputable suppliers emphasize sustainable practices, providing eco-friendly solutions that do not compromise on performance. Offering robust customer support further solidifies their commitment to client success, providing guidance and solutions throughout the material's life cycle.
In conclusion, the landscape of refractory kiln lining materials is as diverse as it is critical to industrial success. By emphasizing experience, expertise, authoritativeness, and trustworthiness in selection and application, industries can ensure efficient, safe, and profitable operations. Investing in high-quality refractory solutions not only maximizes kiln performance but also underscores a commitment to innovation and sustainability in pursuing industrial excellence.