Unlocking the Potential of Refractory Materials in Foundries
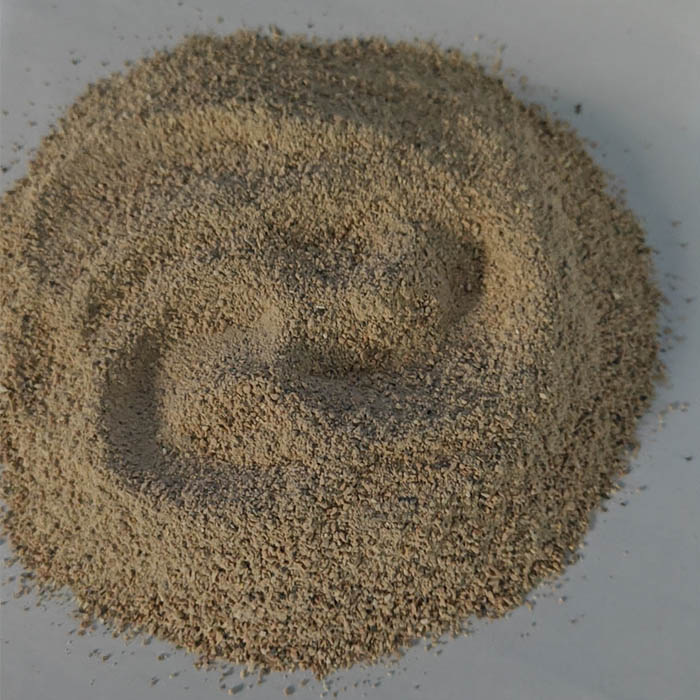
In the intricate world of foundry operations, refractory materials stand as unsung heroes. They ensure the seamless flow of molten metal and safeguard the integrity of molds and casting processes. However,
the significance of refractory materials often remains underappreciated. This article aims to shed light on the essential role of refractory materials in foundries, enhanced through first-hand experience and expert insights, demonstrating their impact on enhancing operational efficiency and product quality.
Understanding Refractory Materials
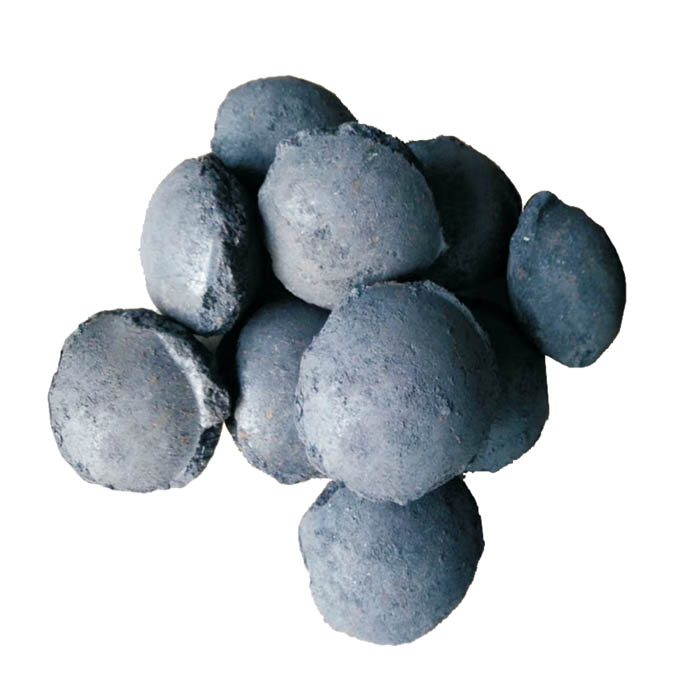
Refractory materials are intrinsically designed to withstand extreme temperatures, chemical erosion, and thermal shock. Typically composed of oxides, carbides, and nitrides, materials like alumina, silica, and magnesia form the backbone of refractory materials used in foundries. Their primary function is to line furnaces, kilns, incinerators, and reactors, creating a thermal and chemical buffer between the equipment and the extreme environments they are subjected to.
Experience in Refractory Application
Operational experience consistently highlights the critical importance of selecting the appropriate refractory materials for specific casting processes. One seasoned foundry technician vividly recalls an incident where the wrongful choice of refractory lining led to compromised steel quality. The material's misfit to withstand the specific chemical stressors led to premature wear and tear, affecting the surface quality of the castings and eventually causing significant financial losses. This anecdote emphasizes the importance of tailoring refractory choices to specific foundry environments and the metals being processed.
Expertise in Material Selection
refractory material foundry
Refractory experts emphasize a holistic understanding of the types and behaviors of different refractory materials. The choice between monolithic refractories, such as castables and gunning mixes, and pre-formed shapes depends largely on the design and demands of the foundry operation. For instance, high-alumina refractories, known for their excellent thermal stability and resistance to slag attack, are often recommended for furnace linings dealing with non-ferrous metals. Meanwhile, silica refractories are preferred in environments where thermal shock resistance is paramount. This expert-driven strategy optimizes foundry performance by extending equipment lifespan and improving product quality.
Authoritativeness in Industry Standards
Refractory materials, essential to foundry best practices, conform to strict industry standards set by organizations such as ASTM International. These bodies provide guidelines ensuring the materials meet rigorous safety, performance, and reliability benchmarks. Foundries adhering to these standards gain a competitive edge, optimizing processes and distinguishing their products in competitive markets. Compliance with established standards thus signifies a foundry’s commitment to quality and safety, enhancing its credibility and reputation among clients and stakeholders.
Trustworthiness through Consistent Performance
When engaging with refractory material suppliers, foundries should prioritize transparent, robust partnerships that guarantee steady, reliable supplies of high-quality materials. Inspecting material provenance and supplier certifications ensures the materials' integrity and performance reliability. Feedback loops between foundries and suppliers, where performance data is regularly reviewed and improvements coordinated, reinforce trust and facilitate innovation.
Conclusion The Way Forward
The impact of refractory materials in foundry operations cannot be overstated. Balancing expertise and experience in incorporating these materials into processes is crucial. By adhering to industry standards, actively engaging with competent suppliers, and continuously adapting to new technologies and findings, foundries can enhance their operations' resilience and efficiency. As industries evolve and demands grow, refractories will undoubtedly continue to play a pivotal role in ensuring the seamless transformation of raw materials into the intricate, precision-engineered components that modern economies rely on. As such, their considered implementation marks a foundational aspect of strategic foundry management, promising longevity and excellence in production outcomes.