Refractory material insulating castables are critical components in various industrial applications, providing both thermal insulation and structural integrity to high-temperature environments. As industries evolve, the demand for innovative and effective insulating castables has surged, leading to advancements in material science and engineering. This article delves into the nuances of these castables, offering insights into their unique properties, manufacturing processes, and application benefits, while anchoring their importance in industrial settings.
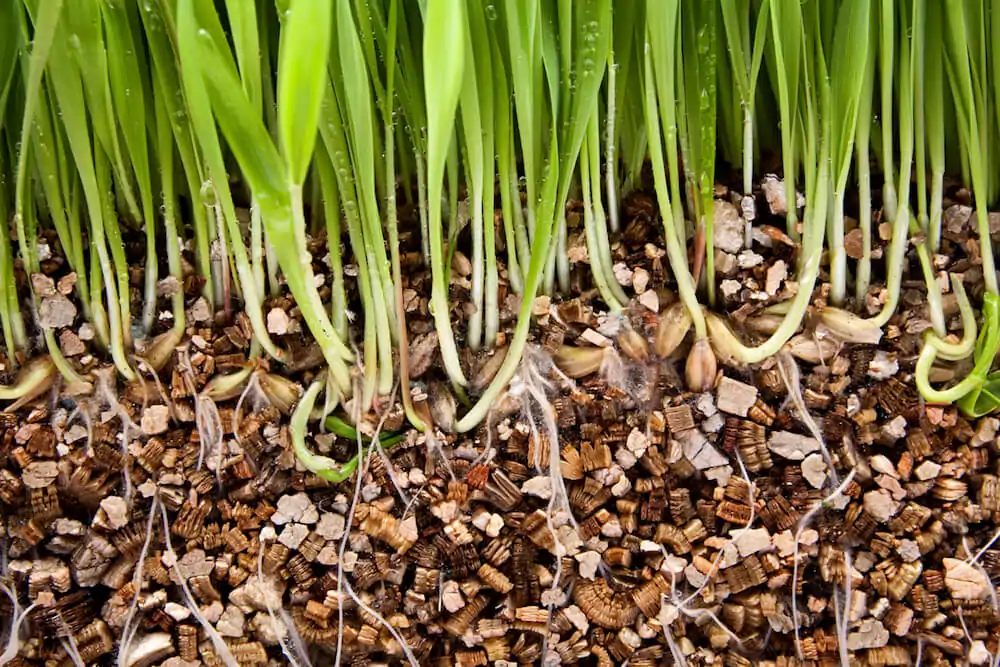
One of the key attributes of refractory material insulating castables is their ability to withstand extreme temperatures while minimizing heat loss. This dual functionality is achieved through a complex blend of raw materials, including refractory aggregates, binders, and additives, each playing a distinct role in enhancing the performance of the castables. Refractory aggregates, often composed of alumina, silica, or magnesia, provide the castable with its primary heat-resistant properties. These aggregates are selected based on the specific operating conditions and thermal requirements of the application.
Binders such as calcium aluminate cement are integral to the formation of a robust matrix that binds the aggregates together. The choice of binder significantly influences the castable's thermal conductivity, density, and setting characteristics. Additives, ranging from deflocculants to fibers, are included to improve workability, reduce shrinkage, and enhance the mechanical strength of the final product. The formulation of these components is a meticulous process, requiring expertise in material science to ensure optimal performance across various high-temperature environments.
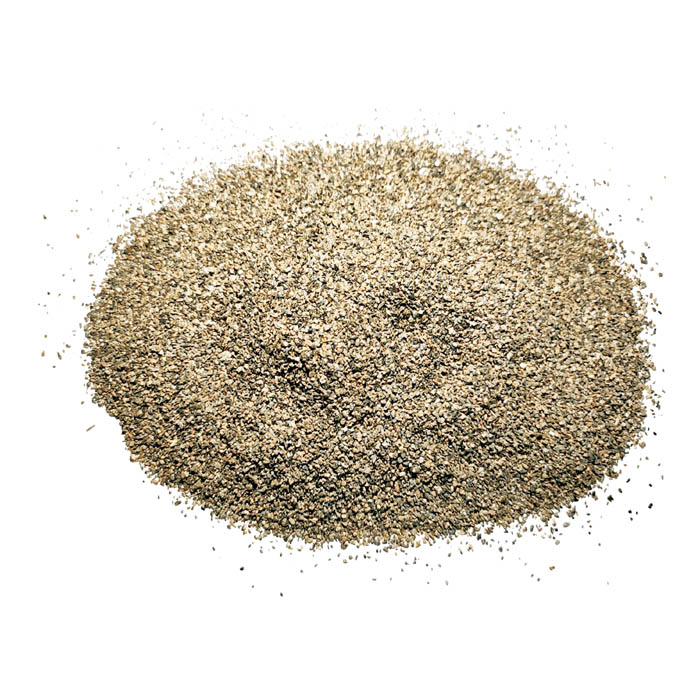
The production of refractory insulating castables is rooted in precision and quality control. The manufacturing process begins with the careful selection and proportioning of raw materials, followed by thorough mixing to achieve uniform consistency. Advanced mixing technologies ensure that each particle is evenly coated with the binder, optimizing the castable's performance. The mixture is then subjected to stringent testing protocols to evaluate its refractoriness, mechanical strength, and thermal insulation properties.
Application techniques for insulating castables vary, depending on the complexity and demands of the project. Common methods include gunning, casting, and ramming, each offering distinct advantages in terms of installation speed and versatility. The choice of method is determined by factors such as the size and shape of the installation area, as well as the thermal and physical stresses anticipated in service. Expert application not only ensures the integrity of the insulating layer but also prolongs the lifespan of the installation, reducing maintenance costs and downtimes.
refractory material insulating castables
In industries such as metallurgy, energy, and petrochemicals, the role of refractory insulating castables cannot be overstated. They are essential in furnaces, kilns, and reactors where high temperatures and corrosive environments are prevalent. The ability of these castables to provide thermal insulation while maintaining structural support enhances energy efficiency and operational safety. This is particularly crucial in energy-intensive processes where heat retention translates directly to cost savings and reduced environmental impact.
Amazon's supply-chain reliance on efficient insulating materials in its large-scale warehousing facilities is testament to the versatility and economic advantage of advanced insulating castables. In modern electric arc furnaces, for instance, the integration of specialty castables has revolutionized efficiency metrics, with temperature retention contributing directly to reduced energy consumption.
The evolution of refractory material insulating castables is driven by continuous research and development efforts. Innovations in nanoparticle technology and composite material engineering hold promise for future advancements, potentially pushing the boundaries of what is possible in terms of thermal insulation and durability. Industry-leading manufacturers invest significantly in R&D to remain at the forefront, offering products that not only meet but exceed industry standards.
In summary, refractory material insulating castables are indispensable in high-temperature industrial settings, providing unparalleled thermal insulation and structural integrity. Through a combination of expert formulation, precise manufacturing, and skilled application, these materials ensure efficiency, safety, and sustainability in demanding environments. As industries seek to optimize their operations, the role of innovative insulating castables will only continue to expand, setting new benchmarks in industrial performance and cost-effectiveness.