Refractory materials play a pivotal role in high-temperature industrial applications, particularly in industries like steel, glass, and ceramics manufacturing. Among these,
lightweight refractory materials have gained traction for their unique blend of attributes. Offering thermal insulation properties without the bulk of traditional refractory materials, they present an efficiency-saving solution for various high-temperature processes.
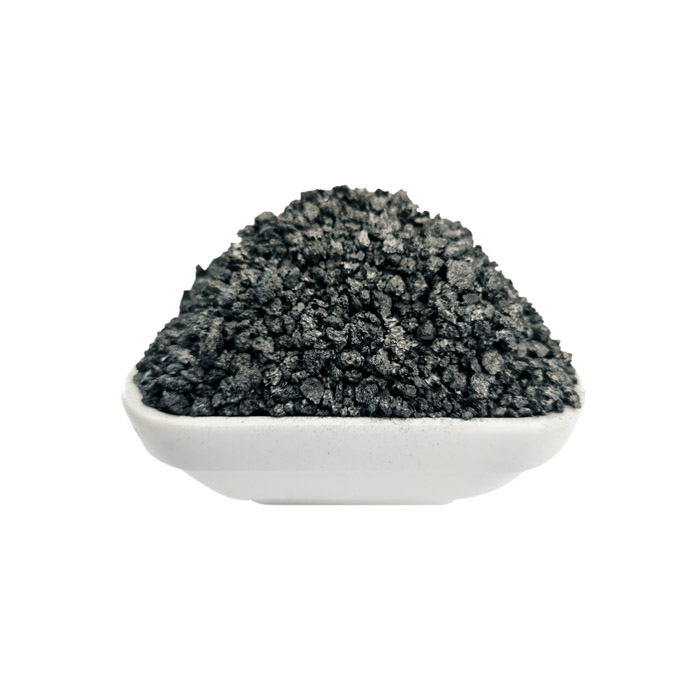
Lightweight refractory materials are characterized by their low thermal conductivity and density, which is achieved through the introduction of air spaces via manufacturing processes that include firing at high temperatures to partially vitrify the material. This reduction in density makes them highly suitable for applications where weight and thermal conservation are critical.
In industries where the thermal performance and efficiency of furnaces, kilns, or reactors are paramount, the use of lightweight refractory materials ensures that less energy is required to maintain desired operational temperatures. This can significantly reduce energy costs while also extending the lifecycle of the equipment by reducing thermal shock – one of the main adversities in high-temperature operations.
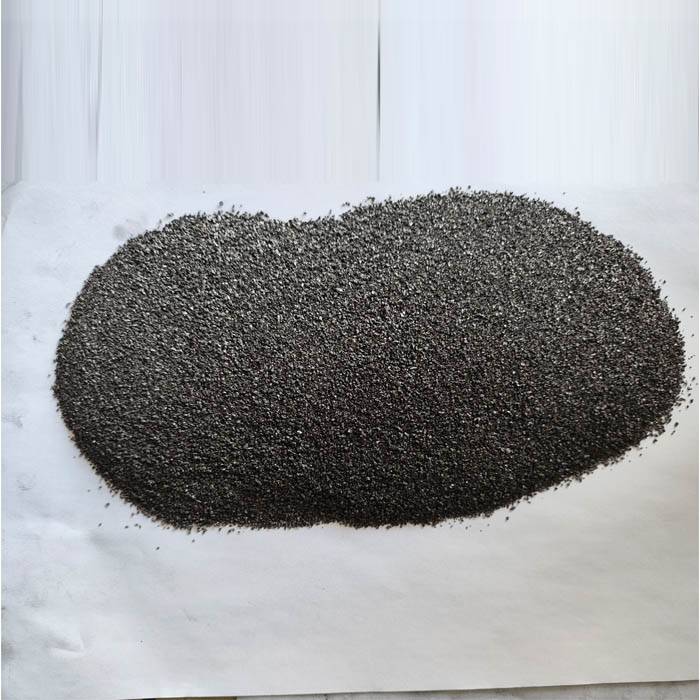
The choice of lightweight refractory materials is bolstered by several years of research and development, ensuring they are not only effective but also durable. Their composition often includes perlite, vermiculite, or lightweight aggregates like expanded clay, which are designed to withstand exposure to severe operational conditions without compromising their structure. Experts in the field can attest to their reduced heat storage and rapid heating and cooling capabilities, which can be vital in processes requiring precise temperature control.
A crucial aspect of their application is ensuring the right specification for the operating conditions. Consultation with refractory specialists is recommended to tailor the material to the specific needs of the operation, ensuring compatibility not only with temperature but also with other operational demands such as chemical exposure and physical wear. Companies like Morgan Advanced Materials and Vesuvius are industry leaders in providing such customized solutions, backed by extensive research and in-field expertise.
refractory material lightweight
Trustworthiness in the use of lightweight refractory materials comes from their proven impact on operational efficiencies and their growing adoption across multiple sectors. Regular assessments and performance measurements are advised to maximize their potential. Engaging with reputable suppliers who offer not just the products but comprehensive user guidance and testing can further reinforce confidence in these solutions.
Understanding the full potential of lightweight refractory materials requires both a theoretical and practical appreciation of their capabilities. Real-world case studies highlight their successful integration into industrial processes. For instance, a well-documented implementation is in aluminum production where the process demands not only high heat tolerance but also minimal energy consumption. The transition to lightweight refractory materials in such scenarios has been shown to dramatically reduce thermal leaks, ensuring more energy-conservative operations.
Therefore, businesses looking to improve their high-temperature processing systems significantly benefit from insights provided by engineers and specialists versed in the nuances of refractory technology. The integration of lightweight refractories is not merely a purchase but an investment into more sustainable and economically viable industrial practice.
In summary, lightweight refractory materials represent a harmonious blend of innovation and efficiency. Their adoption in high-temperature industries is a testament to ongoing advancements in material science, offering industries not just a product but a solution for scaling efficiency, reliability, and sustainability. With the continual development of these materials, the future holds significant potential changes in how thermal processes are managed, promising greener operational methodologies and improved cost management.