In the realm of industrial engineering and production, refractory materials play a pivotal role in enhancing the durability and efficiency of manufacturing processes. These materials, known for their exceptional resistance to high temperatures and thermal stress, are indispensable in industries such as steelmaking, glass production, and cement manufacturing, where extreme thermal conditions are the norm. For companies sourcing refractory materials, understanding their composition, application, and the latest advancements is crucial for optimizing their benefits.
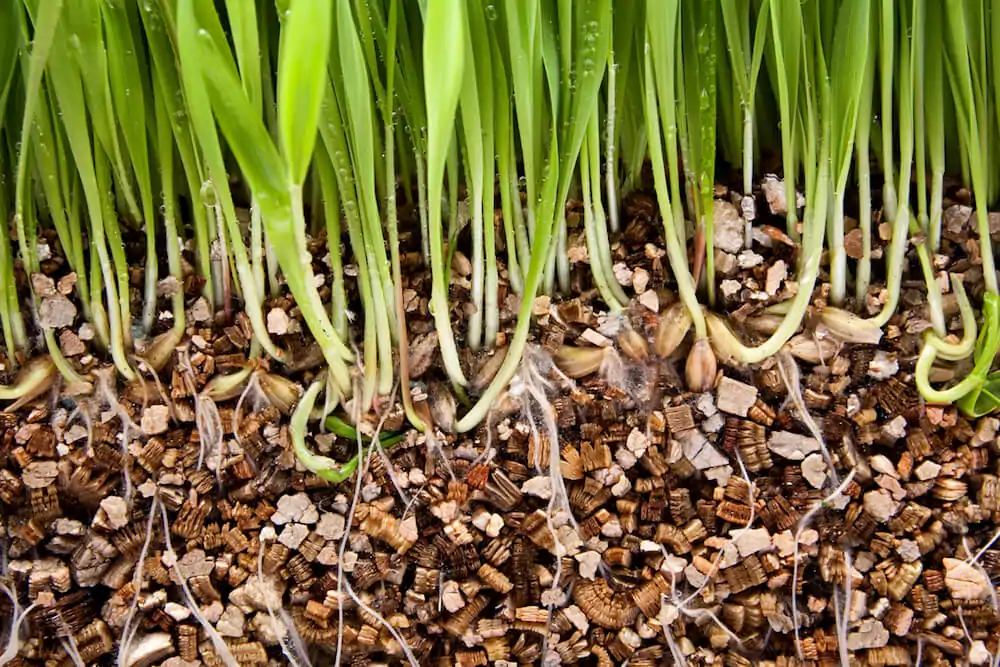
Refractory materials primarily consist of ceramics, which exhibit high melting points, thermal stability, and chemical inertness. Among the most widely used are alumina, silica, magnesia, and zirconia.
Each of these materials offers distinct properties suited to specific applications. For instance, alumina-based refractories are highly resistant to slag and metallic penetration, making them ideal for use in steel ladles and furnaces. On the other hand, silica refractories, with their excellent thermal shock resistance, are frequently used in the glass industry to line furnaces and kilns.
A deeper understanding of the selection process of refractory materials is paramount for industry professionals. The choice depends on several factors, including the operating temperature of the application, chemical compatibility, and mechanical stress. Additionally, cost considerations and environmental impact are increasingly significant in today's market. By prioritizing these factors, companies can ensure optimal performance and longevity of their refractory installations, ultimately leading to substantial cost savings and reduced downtime.
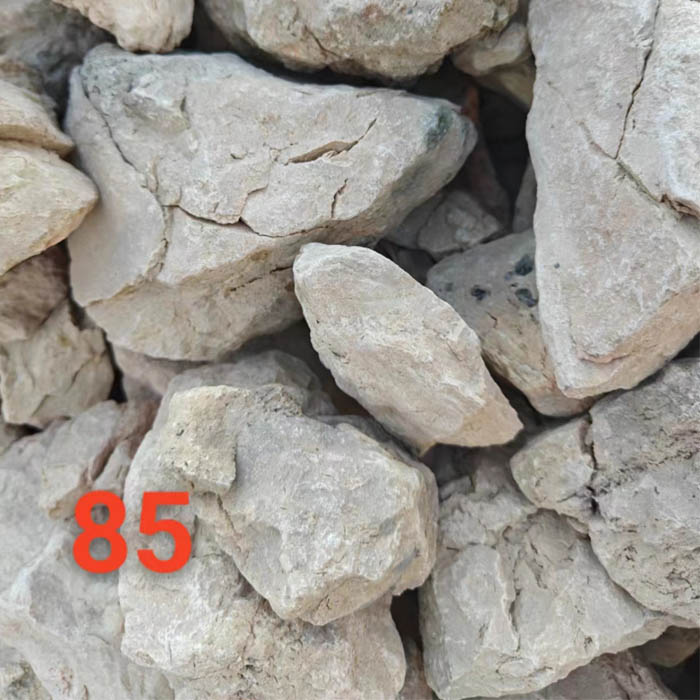
Recent advancements in refractory technology have resulted in the development of innovative materials and systems that offer superior performance. One such innovation is the integration of nanotechnology into refractory production. Nano-refractories are engineered at the molecular level to enhance properties such as thermal conductivity, strength, and wear resistance. This cutting-edge approach not only improves the efficiency of high-temperature operations but also contributes to energy conservation through better insulation.
refractory materials from stage
Expertise in the installation and maintenance of refractory materials is equally critical to their performance. Proper installation is a complex process that involves meticulous procedures to prevent common issues such as thermal spalling and chemical corrosion. Regular maintenance, including thorough inspections and timely repairs, extends the lifespan of refractories. Industries are now employing sophisticated diagnostic tools like thermographic imaging and laser scanning to monitor the condition of refractory linings, ensuring early detection of potential failures.
Authority in refractory materials is evident through industry leaders who continuously research and develop new products tailored to ever-evolving industrial demands. These companies often collaborate with universities and research institutes to advance the science of refractories, resulting in patented technologies and proprietary formulations that set new standards in the field. Their expertise not only provides reliable products but also offers consultancy services that guide clients in making informed decisions tailored to their specific needs.
Trustworthiness is a cornerstone in the selection and application of refractory materials. Reliable suppliers provide not only product assurance but also extensive technical support and after-sales service. Ensuring compliance with industry standards and certifications further solidifies their credibility. Customers seek suppliers who are transparent about the sourcing of raw materials, adhere to environmental regulations, and demonstrate a commitment to sustainability.
In summary, the exploration and utilization of refractory materials are integral to the efficiency and sustainability of high-temperature industrial operations. Through comprehensive expertise, authoritative development, and credible practices, refractory materials continue to evolve, meeting the demanding conditions of modern industries while pushing forward the boundaries of innovation and sustainability. For businesses in search of durable, high-performance solutions, staying abreast of these advancements in refractory technology is essential for maintaining a competitive edge.