Steel-making, a vital process in industrial manufacturing, holds the backbone of modern infrastructure and development. Over centuries, this field has evolved, transforming from ancient methods to today's state-of-the-art practices, driven by technology and innovation.
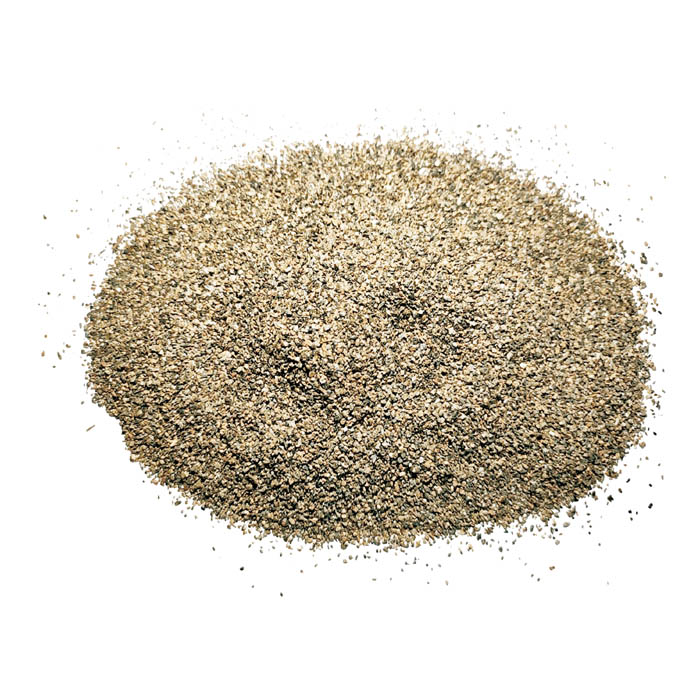
The journey of steel-making begins with the selection of raw materials, primarily iron ore, coke, and lime. Expertise in the choice and blending of these materials directly impacts the quality of the final product. Industry experts advocate using high-grade iron ore to ensure the steel produced will have robust structural integrity and versatility. Real-world experience has shown that an optimal mix can reduce energy consumption and minimize impurity infiltration, enhancing the overall efficiency of steel production.
A deep dive into the technical realm reveals that expertise in the blast furnace operation plays a crucial role. This giant structure, often towering several stories high, uses intense temperatures to convert iron ore into molten iron. Experienced operators ensure precise temperature control and maintain the perfect balance of input materials to enhance output and reduce waste. Many leading manufacturers have integrated AI and IoT technologies to monitor and adjust these parameters in real-time, thus optimizing productivity while lowering environmental impact.
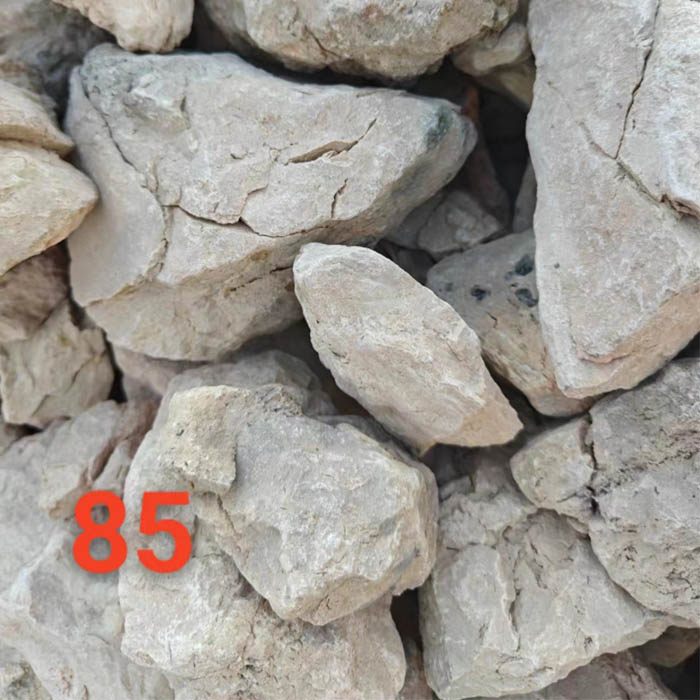
In modern steel-making, the transition from molten iron to steel involves the Basic Oxygen Steelmaking (BOS) or Electric Arc Furnace (EAF) methods.
Expertise in these techniques is paramount. For example, BOS, which involves blowing oxygen through the molten iron, rapidly reduces carbon content, producing high-quality steel. Conversely, EAF, primarily used in recycling scrap steel, offers a more energy-efficient alternative and underpins sustainable steel manufacturing practices.
steel-making
Powerful advisory from seasoned industry specialists suggests that mastering metallurgical science significantly boosts production output and quality. Knowledge of optimum carbon levels and the introduction of alloying elements such as manganese, nickel, or chromium can fine-tune the properties of steel, tailoring it for specific applications from construction to aerospace.
Authoritativeness within the steel-making industry is backed by adherence to international standards and certifications like ISO 9001 or ASTM, ensuring that each batch of steel meets stringent quality requirements. Accreditation by globally recognized bodies not only elevates a manufacturer's reputation but also enhances trustworthiness among clients. These standards provide customers confidence, knowing they are receiving products that comply with rigorous testing and safety procedures.
Trustworthiness in steel-making extends beyond product quality. It encompasses environmental responsibility, an increasingly crucial factor in global manufacturing practices. Adopting eco-friendly practices, such as recycling steel and reducing emissions through cleaner technologies, earn credibility and trust from customers and shareholders alike. Companies at the forefront of this initiative are often recognized for innovative solutions that align with global sustainability goals, further solidifying their authoritative standing in the market.
In conclusion, the steel-making industry is a testament to the blend of deep-rooted tradition and cutting-edge innovation. Its evolution is anchored by real-world expertise, technical mastery, authoritative practices, and unwavering trustworthiness. As industries worldwide continue to lean heavily on steel, the ongoing advancements in this field promise a future rich in potential, contributing significantly to global economic growth and sustainability.