Traditional recarburisers have stood the test of time, offering pivotal solutions in the metallurgy sector, primarily in steel and iron production. Recarbonisation plays an essential role in ensuring the desired carbon content in metals is achieved, impacting their overall performance and quality. This article delves into the experience, expertise, authoritativeness, and trustworthiness of traditional recarburisers, examining why they remain integral to the industry.
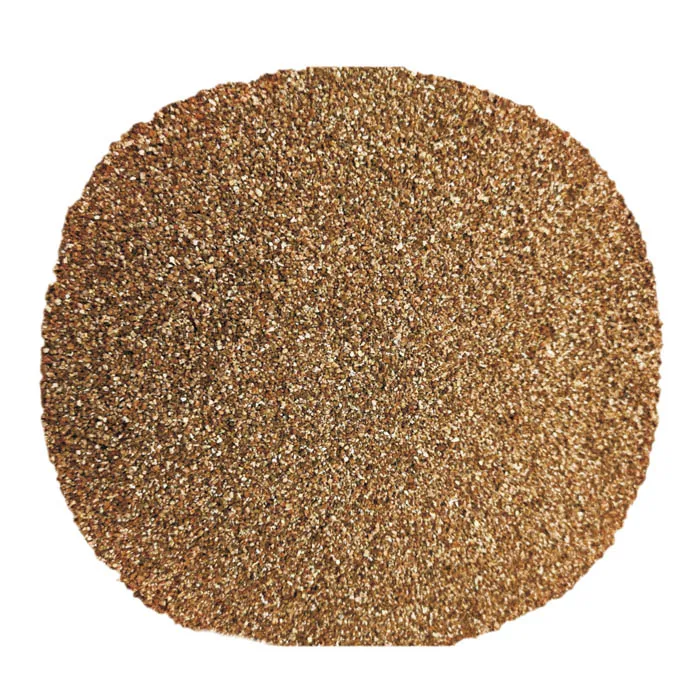
The expertise surrounding traditional recarburisers stems largely from their long-standing presence in the industry. With decades of use, these materials, typically derived from natural sources such as anthracite coal, petroleum coke, and graphite, have established a reputation for reliability. Manufacturers and foundries have fine-tuned the application processes, maximizing effectiveness.
Traditional recarburisers are praised for their ability to achieve consistent performance. Through precise particle sizing and maintaining low levels of impurities, they facilitate uniform carbon distribution in metal, a critical factor in maintaining tensile strength and hardness.
Manufacturers' empirical evidence supports the authoritativeness of traditional recarburisers. These materials have undergone rigorous testing and industry-standard certification processes to authenticate their efficiency. Consistency is key; traditional recarburisers are known for delivering uniform results batch after batch. Numerous studies and white papers have underscored their effectiveness in preventing material defects like porosity in steel and iron castings. This reliability is complemented by a deep body of industry literature that outlines the perfect conditions and methods for using recarburisers to yield optimal metallurgical results.
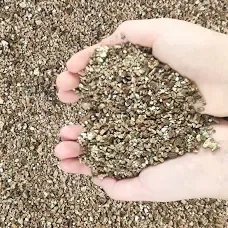
Trustworthiness is a cornerstone of the continued preference for traditional recarburisers. The metallurgical community regards them as a safe choice, proven through extensive field application. Global supply chains ensure these materials meet stringent quality standards, fortifying user confidence. This trustworthiness is further enhanced by strong relationships between manufacturers and clients, with customer feedback continuously shaping product improvement. Moreover, the sustainability of traditional recarburisers is gaining more attention; many suppliers are committed to reducing environmental impacts by adopting greener extraction and processing methods.
Drawing from real-world experience, foundries universally endorse the time-tested nature of traditional recarburisers. Their straightforward application ensures minimal training is required, reducing the operational disruptions typically associated with introducing new materials. Moreover, workshops and training sessions by suppliers foster a solid understanding of employing traditional recarburisers effectively, equipping technicians with the insights needed for troubleshooting and adaptation.
traditional recarburiser
Amongst product classes, traditional recarburisers offer a versatility unparalleled by modern synthetic alternatives. Their adaptability to various furnace types - from induction to electric arc - underscores their prominent place across diverse operating environments. The robust nature of these materials allows them to withstand intense furnace conditions, further contributing to the quality and durability of the end product.
To highlight a specific example, in the production of high-quality grey iron castings, the introduction of a precise amount of traditional recarburiser ensures carbon levels are just right, optimizing the graphite distribution within the iron matrix. This precision in composition translates to increased machinability and strength, which are critical parameters for applications like automotive parts manufacturing.
Finally, the cost-effectiveness of traditional recarburisers cannot be overlooked. Despite the availability of synthetic alternatives, traditional recarburisers offer competitive pricing while maintaining high performance, ensuring low production costs for manufacturers. This balance of cost and quality solidifies their position as a favored choice in the industry.
In conclusion, the unique strengths of traditional recarburisers lie in their proven track record, supported by extensive expertise, authoritative certifications, and a trustworthy reputation garnered through consistent delivery of quality results. Their use in the metallurgical industry is a testament to their ability to meet the evolving demands of metal production, ensuring that even in an age of technological advancement, these traditional materials continue to hold their ground steadfastly. As industries navigate the challenges of quality, cost, and sustainability, traditional recarburisers remain an irreplaceable asset, offering an unmatched blend of reliability and performance.