Aluminium Silicate Refractory Materials Factory An Industrial Marvel
The aluminium silicate refractory materials factory stands as a testament to the ingenuity and resilience of modern industrial processes. This specialized facility is dedicated to the production of high-quality, heat-resistant materials that are essential for a variety of applications, ranging from construction to metallurgy. The heart of this factory beats with the rhythmic hum of machinery and the occasional spark of innovation.
Aluminium silicate, also known as kaolinite or simply kaolin, is a clay mineral that exhibits extraordinary properties when subjected to extreme temperatures. Its ability to withstand thermal shock and maintain stability under intense heat makes it an ideal choice for lining furnaces, kilns, and other equipment where high temperatures are a norm. The process of transforming raw kaolin into a usable refractory material involves several critical steps, each performed with precision and care within the factory walls.
The journey begins with mining, where high-quality kaolin is extracted from the earth. This raw material is then transported to the factory, marking the first step in its metamorphosis. Upon arrival, the kaolin undergoes rigorous cleaning and sorting processes to ensure only the finest particles are used in production. These particles are subsequently milled into a fine powder, setting the stage for their transformation into refractory bricks, castables, or shapes.
One of the most critical phases is the blending of the aluminium silicate with binders and other additives to enhance its refractory qualities. This mixture is then formed into the desired shapes using either molding or casting techniques This mixture is then formed into the desired shapes using either molding or casting techniques
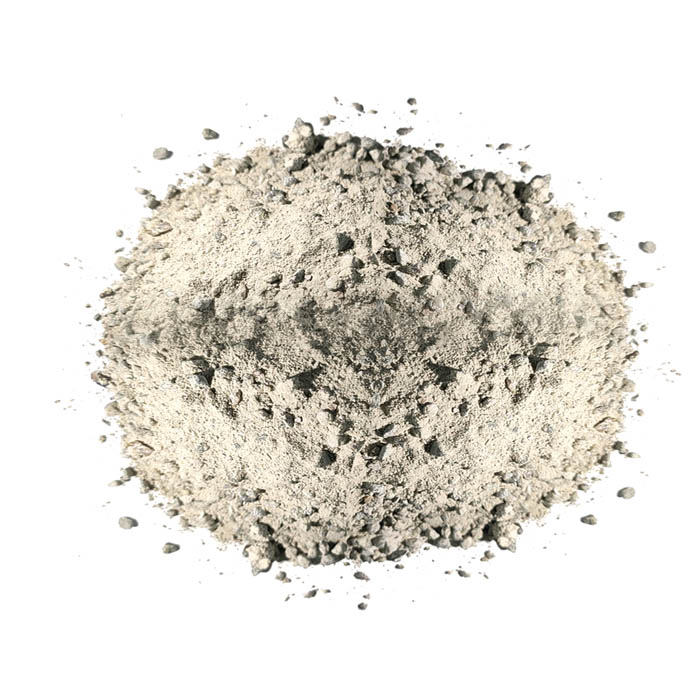
This mixture is then formed into the desired shapes using either molding or casting techniques This mixture is then formed into the desired shapes using either molding or casting techniques
aluminium silicate refractory materials factory. The shaped materials are dried carefully to remove moisture without compromising their structure. Finally, they enter the kiln, where they are fired at temperatures that can exceed thousands of degrees Celsius. This firing process solidifies the bonds between particles, creating a durable and heat-resistant end product.
The aluminium silicate refractory materials factory thrives on innovation and sustainability. Engineers and scientists continuously research and develop new formulations and techniques to improve product quality and efficiency. Additionally, the factory operates with a keen eye on environmental impact, striving to minimize waste and maximize resource use.
In conclusion, the aluminium silicate refractory materials factory is a beacon of industrial excellence, producing vital components that enable many of the modern world's critical processes. From the extraction of raw materials to the final firing in the kiln, every step is executed with precision, ensuring that these refractory materials meet the highest standards of quality and performance. As we look to the future, the advancements made within these walls will undoubtedly continue to shape the course of industrial development and innovation.