Integrated steel making is a transformative process that has been central to the industrial landscape for decades, renowned for its efficiency in producing steel with a variety of applications. This comprehensive process involves multiple stages that convert raw materials such as iron ore, coal, and limestone into high-quality steel. As an industry expert with years of experience in metallurgical engineering, my insights delve into the nuanced mechanisms and benefits of integrated steel making, underscoring its pivotal role in contemporary manufacturing and construction.
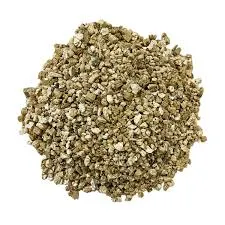
The integrated steel making process begins at the blast furnace, where iron ore, coke, and limestone function in harmony to produce molten iron. One of the most notable advantages of this method is the ability to generate large quantities of molten iron with consistency in composition and quality. This stage is crucial, as the homogeneity of the molten iron sets the foundation for producing steel that meets specific industrial standards. Moreover, employing a blast furnace is economically advantageous, considering the scale of operation and the cost-effectiveness of the raw materials involved.
Transitioning to the next phase,
the steel making process utilizes basic oxygen furnaces (BOFs) to convert molten iron into steel. By blowing oxygen into the molten iron, impurities such as carbon, silicon, phosphorus, and sulfur are significantly reduced. This conversion is not only crucial for enhancing the ductility and strength of steel but also reduces the environmental footprint of the steel making process. The basic oxygen furnace is recognized for its rapid production rate and high efficiency, minimizing energy consumption compared to older methods like open hearth furnaces. This makes it an attractive option for manufacturers striving for environmental responsibility and cost efficiency.
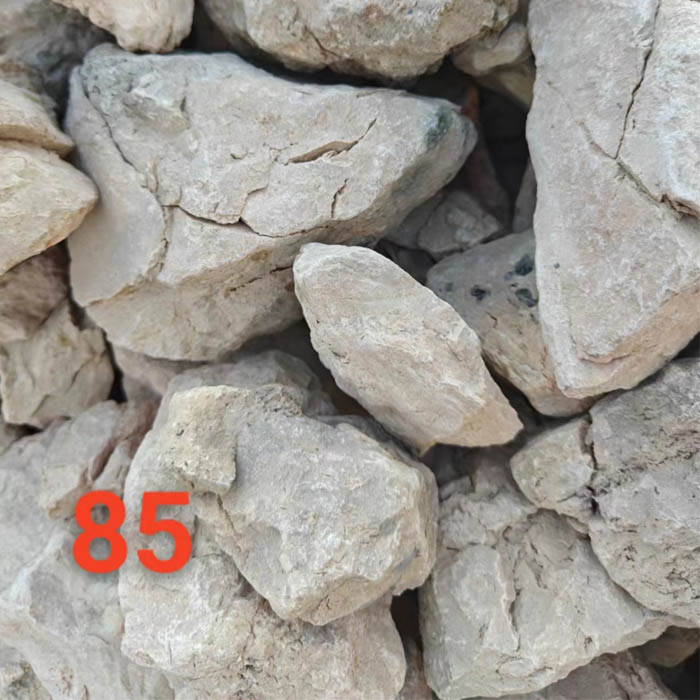
An integral component of integrated steel making is its adaptability in producing diverse steel grades tailored to meet specific application requirements. The flexibility afforded by this process allows for the addition of various alloying elements like nickel, chromium, and vanadium, which can significantly alter the characteristics of steel, enhancing attributes such as corrosion resistance, hardness, and tensile strength. As such, integrated steel making is indispensable in meeting the demands of critical industries such as automotive, aerospace, and construction, where material performance is non-negotiable.
integrated steel making
The continuous casting phase comes next, a revolutionary step that improves the quality and yield of steel production. By streamlining the transformation of molten steel into solid form, continuous casting reduces the occurrence of defects and enhances the structural integrity of the final product. This technological advancement underscores the expertise required to maintain exacting standards of production and is a testament to the commitment of steel manufacturers to deliver superior products.
Central to the reliability and trustworthiness of integrated steel making is the rigorous quality control measures implemented throughout the process. Each phase is meticulously monitored to ensure compliance with international quality standards. This involves sophisticated metallurgical analysis and testing, which is crucial in assuring customers of the material's performance and longevity. The expertise and dedication of engineers and scientists in maintaining these standards cannot be overstated, as it underpins the industry's reputation for producing materials that are both durable and reliable.
Beyond the technical aspects, integrated steel making represents a commitment to sustainability, with ongoing efforts to reduce emissions and resource consumption. Innovative strategies such as recycling steel scrap and utilizing by-products effectively are pivotal in enhancing the eco-friendliness of the process. These initiatives reinforce the trustworthiness of integrated steel production as a responsible choice for businesses mindful of their environmental impact.
In conclusion, integrated steel making stands as a hallmark of industrial expertise, underpinned by a robust framework that prioritizes efficiency, quality, and sustainability. Its role in shaping infrastructure and advancing technological progress cannot be overstated. Whether one is seeking unparalleled strength or specific material properties, the versatile outcomes of integrated steel making solidify its status as an invaluable resource in the modern industrial ecosystem.