Blast furnace steel making is a complex and integral part of the modern steel industry, known for its efficiency and high-quality steel production. This well-established method has evolved over decades, redefining industrial standards with its robust process, reliable output, and alignment with both traditional and contemporary requirements.
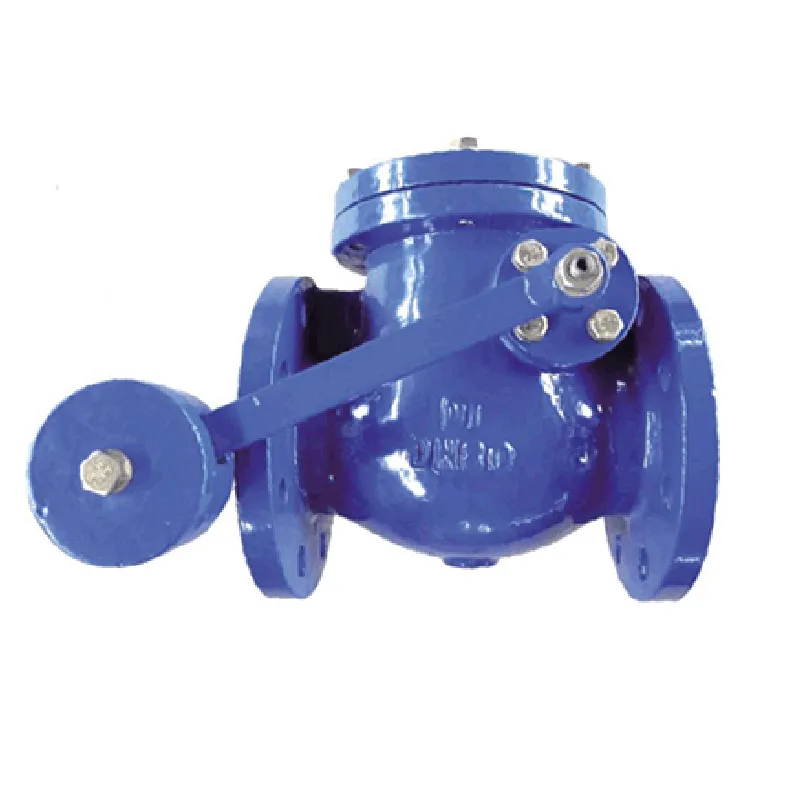
A blast furnace is a large structure where iron ore is converted into liquid iron, which is then further processed into steel. This is achieved by smelting, a process that involves heating iron ore with coke (a form of carbon) and limestone at temperatures exceeding 2,000 degrees Celsius. The carbon from the coke removes the oxygen from the ore, leaving behind molten iron. The limestone aids in the removal of impurities, which float to the top as slag.
Real-world experience in the steel-making industry emphasizes the importance of consistency and precision in the blast furnace process. The quality of the raw materials, the precise control of temperature, and the management of the chemical reactions profoundly influence the quality of the produced steel. Professionals in the field often highlight the necessity of routine monitoring and adjustments to ensure optimal performance and output.
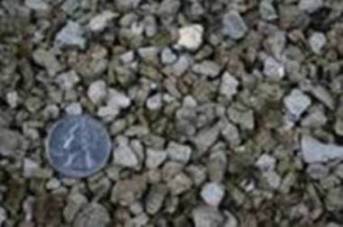
Expertise in blast furnace steel making involves understanding the thermodynamics and kinetics of the reactions within the furnace. Steelmakers leverage advanced technologies like data analysis and automation to predict and control these reactions accurately. By employing sensors and automated control systems, experts have enhanced the efficiency and reduced the operational costs and environmental impacts of steel production.
blast furnace steel making
The blast furnace process holds a place of authority within the industry due to its ability to produce large quantities of high-grade steel efficiently. Academic studies and industrial reports consistently reaffirm its viability and effectiveness. Current advancements focus on reducing coke consumption, optimizing energy use, and maximizing the furnace longevity, ensuring that this method remains at the forefront of steel-making technology.
Trustworthiness comes from the disciplined adherence to international standards and regulations that govern blast furnace operations. Industry leaders invest heavily in quality assurance protocols, environmental compliance, and safety measures to maintain their credibility and uphold consumer confidence in their products.
The future of blast furnace steel making is promising, with continuous innovations aimed at improving sustainability and reducing carbon emissions. Efforts are underway to integrate renewable energy sources into the process, further lowering its carbon footprint. Companies are also exploring the use of alternative reducing agents, such as hydrogen, to potentially revolutionize the steel-making process.
In conclusion, blast furnace steel making, with its well-researched methodology and robust framework, remains an indispensable component of the steel industry. Its excellence is maintained by the commitment to experience, expertise, authoritativeness, and trustworthiness in practice. As the industry navigates the challenges of the modern world, the season-tested principles and ongoing innovations in blast furnace steel making will undoubtedly continue to deliver high-quality steel products, meeting both current demands and future needs.