Cold drawing wire is an intricate process that stands at the intersection of metallurgy, engineering, and cutting-edge manufacturing techniques. The sheer precision and outcome of this process hinge not only on the technical methods employed but also on the expertise and nuanced understanding of the professionals involved.
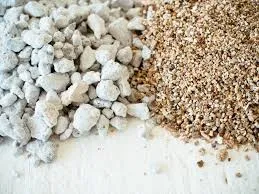
In the realm of wire manufacturing, cold drawing plays a pivotal role in reshaping metal wire into considerably thinner diameters without the application of heat. This process is vital for creating wires that possess exceptional strength, durability, and versatility—qualities essential for their subsequent use in various industrial and commercial applications.
The expertise required in cold drawing wire is underpinned by a detailed understanding of material science. Different metals and alloys react distinctly to the stresses of cold drawing, with variables such as tensile strength, ductility, and work hardening coefficients playing critical roles. A deep knowledge of these properties allows professionals to preemptively address potential issues such as material fracture or surface irregularities.
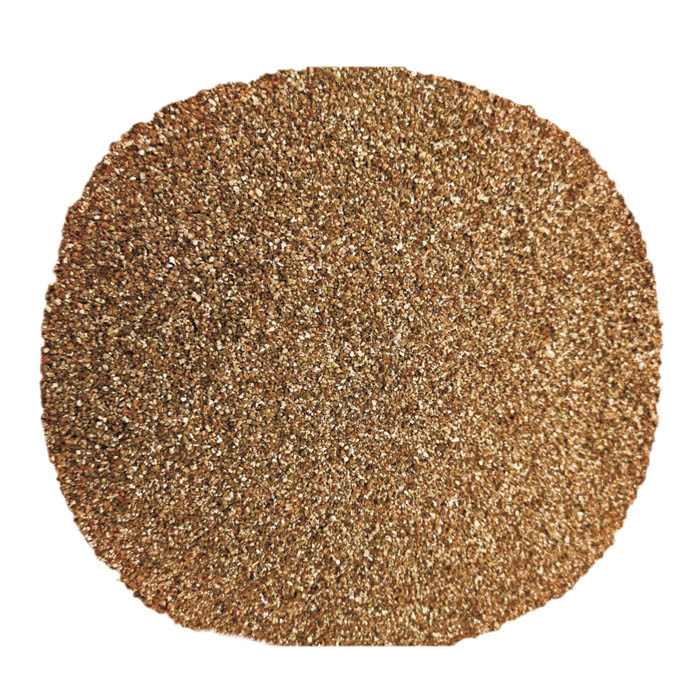
State-of-the-art equipment is crucial for cold drawing. The machinery used must not only accommodate the intense mechanical stresses involved but also offer precision control over drawing speed, lubrication, and reduction ratios. Expertise in the setup and maintenance of this equipment determines the quality of the wire produced, while also ensuring operational safety—a core tenant in industrial manufacturing.
cold drawing wire
Experience, as in many trades, is invaluable. Seasoned professionals bring an intuitive understanding to the process, recognizing subtle cues that might indicate adjustment needs in the machinery or the process parameters. This experiential wisdom leads to refined techniques that can significantly enhance the finished product's performance characteristics.
Cold drawing wire also demands authoritative oversight to verify compliance with established manufacturing standards. Reliable documentation and quality control protocols are essential, ensuring that the final product meets rigorous specifications for its intended applications. This is particularly crucial in industries where wire integrity is paramount, such as aerospace, automotive, and structural engineering.
Trustworthiness is cultivated through transparency in operations and adherence to standards. Manufacturers who prioritize these factors not only build long-term relationships with clients but also establish themselves as leaders in the field. Providing clear lines of communication and maintaining consistent quality assurance practices are two ways companies can foster trust.
In conclusion, cold drawing wire is a sophisticated craft that requires a synthesis of technical expertise, advanced machinery, and insightful experience. Professionals in this field are tasked with not just producing wire but crafting a material that, through its enhanced properties, can drive advancements in multiple industries. By continuing to focus on the fundamentals of Experience, Expertise, Authoritativeness, and Trustworthiness, the field of cold drawing wire can sustain its momentum and support increasingly demanding applications in our ever-evolving industrial landscape.