Electric furnace steel making, an integral component of the modern steel industry, has been transforming the way steel is produced since its introduction. As an experienced practitioner in the steel production field, I have witnessed firsthand how electric furnaces provide unique advantages that not only optimize production processes but also align with sustainable practices — a crucial consideration in today's environmentally conscious market.
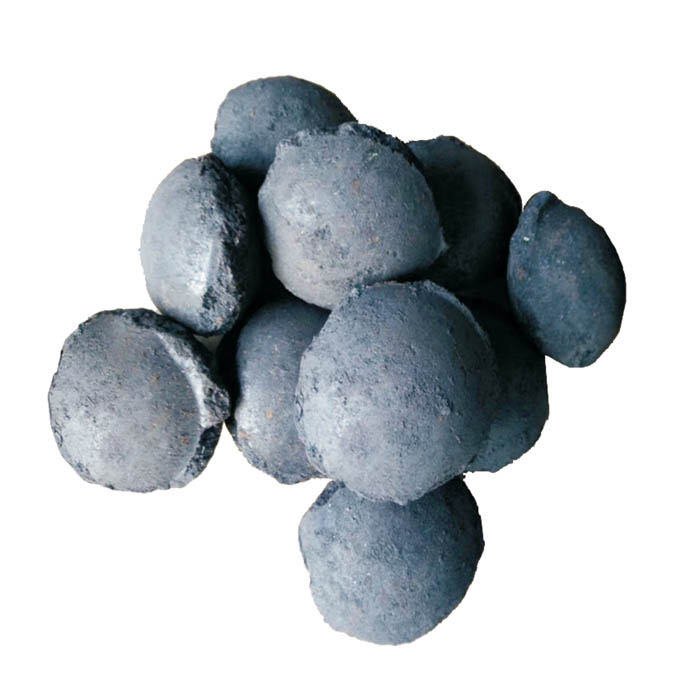
Historically, steel manufacturing predominantly relied on blast furnaces, which involved high carbon emissions and significant energy consumption. However, with growing technological innovations and a shift towards greener manufacturing processes, electric arc furnaces (EAF) have gained prominence. Unlike traditional methods, electric furnace steel making employs an electric arc between electrodes to melt scrap steel — a process that is not only efficient but also environmentally friendly due to its lower carbon footprint.
From a technical standpoint, the expertise involved in operating electric furnaces represents an advanced skill set. Operators must understand the nuances of maintaining the perfect arc temperature to ensure optimal melting, while also consistently monitoring energy consumption to enhance efficiency. Unlike conventional methods, the flexibility of electric furnaces allows for batch-specific adjustments, accommodating diverse grades and types of steel. This adaptability results in better resource utilization and reduced waste, underscoring the expert-level knowledge required to manage these dynamic variables effectively.
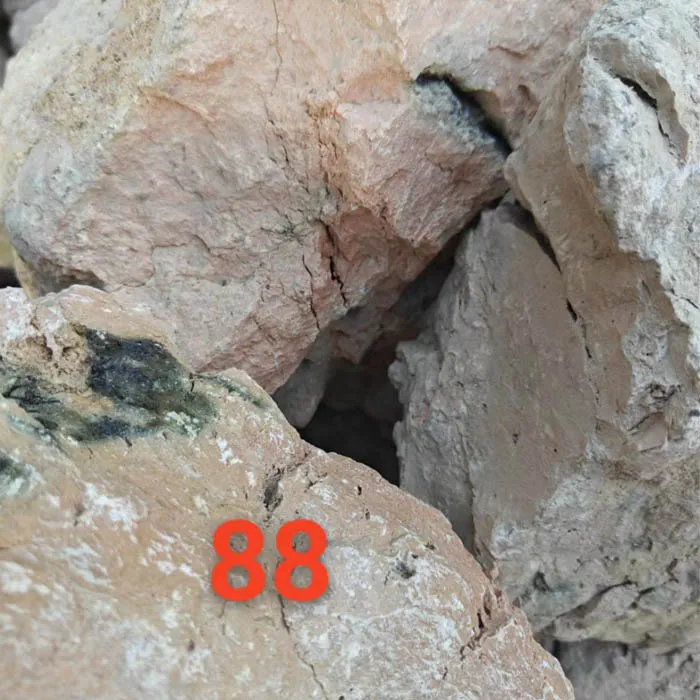
The authority of electric furnace steel making lies in its capacity to integrate with other innovative technologies such as direct reduced iron (DRI) processes and scrap pre-heating methods. These technologies further optimize resource use, minimize impurities, and enhance the overall quality of steel. As industry experts acknowledge, the integration of these systems positions electric furnaces at the forefront of modern, efficient, and eco-friendly steel production technology.
electric furnace steel making
Trustworthiness in electric furnace steel making is emphasized through the rigorous standards and certifications that govern the process. Operators must adhere to stringent guidelines to ensure that the steel produced meets international quality standards. Regular audits and compliance checks are essential to maintain the integrity of operations, reinforcing the credibility of steel produced via electric furnaces. Furthermore, transparency in reporting production statistics, energy consumption, and environmental impact contributes to building trust with stakeholders and customers alike.
Product-wise,
steel produced through electric furnaces does not compromise on quality. With controlled manufacturing conditions, it often exhibits superior properties such as enhanced strength, ductility, and durability, making it highly sought after in construction, automotive, and infrastructure projects. The demand for high-quality, sustainably manufactured steel has never been greater, aligning perfectly with the capabilities of electric furnace steel making.
In conclusion, the evolution of electric furnace steel making encapsulates the intersection of experience, expertise, authority, and trustworthiness. It provides a sustainable, efficient alternative to traditional steel production methods, fulfilling both industrial and environmental imperatives. As the steel industry continues to evolve, embracing electric steel making furnaces represents a forward-thinking approach that not only meets current market demands but also anticipates future advancements in eco-friendly manufacturing practices.