The process of joining and insulating gas pipes is a critical component in ensuring the safety, efficiency, and longevity of gas supply systems. The integrity of these connections and the quality of the insulation used can significantly impact the performance of both residential and commercial gas systems. With the advancement of technology, the materials and methods employed in this area have evolved, providing solutions that bring both reliability and efficiency to the forefront.
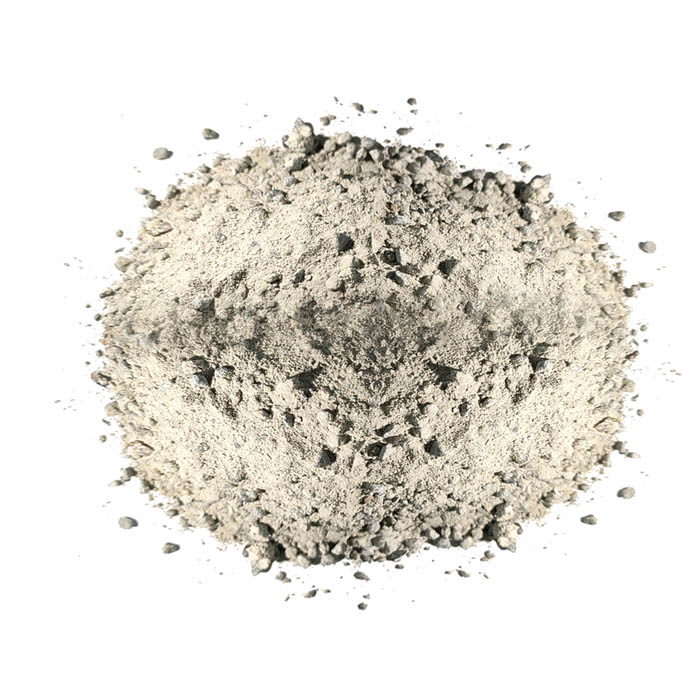
Gas pipe joining involves the physical connection of pipe sections to create a continuous gas passage system. Traditionally, materials like black iron and galvanized steel were the primary choices for gas piping. They require complex threading and cutting processes, and although still in use, today's systems more frequently employ flexible materials like copper and polyethylene (PE). Copper, known for its durability and resistance to corrosion, is joined using flare fittings or soldering. PE pipes, meanwhile, are increasingly favored for their flexibility and ease of installation, often joined using mechanical fittings or a fusion process that melts and joins the plastic material together, creating a leak-proof seal.
Among the advances in gas pipe joining materials, cross-linked polyethylene (PEX) stands out. PEX provides a high degree of flexibility and resistance to temperature and pressure changes. It is typically joined using crimp rings and cinch clamps over barbed fittings made from brass or polymer, creating a tight, secure connection that minimizes the risk of leaks. PEX's versatility and ease of installation have made it a popular alternative to traditional materials.
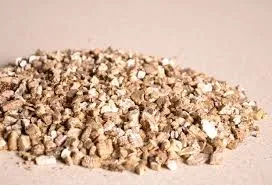
Insulation of gas pipes is another essential factor in optimizing the performance of a gas supply system. Proper insulation prevents heat loss, increases energy efficiency, and provides an essential layer of safety by controlling surface temperatures and minimizing condensation issues that could lead to corrosion or other issues.
Traditionally, insulation materials such as fiberglass and foam rubber were used extensively. Fiberglass, prized for its thermal resistance, is often applied in spaces where higher temperatures might be encountered. However, it can pose installation challenges due to its rigidity and requirement for vapor barriers. On the other hand, foam rubber, with its inherent flexibility and ease of application, is often used in residential settings where it can be applied quickly and efficiently around piping runs.
Recent innovations have introduced advanced materials such as aerogels and flexible elastomeric foams. Aerogels provide superior thermal resistance while maintaining a very low density and minimal thickness, making them ideal when space is a premium. Flexible elastomeric foams offer excellent thermal insulation properties while also providing moisture resistance, making them suitable for both indoor and outdoor applications.
gas pipe joining insulating material
The integration of these modern insulating materials not only helps in reducing energy loss but also significantly extends the life cycle of the piping system by protecting it from environmental factors and physical damage. The key to effective insulation lies in choosing the material that best suits the environmental conditions and the specific physical requirements of the gas piping system.
Expert advice suggests that maintaining a system of regular checks and preventive maintenance can enhance the efficacy of both the joining and insulation processes. Advanced imaging technologies like infrared thermography can be employed to detect heat loss or leaks in pipes, providing a non-invasive method to maintain efficiency and safety standards.
Furthermore,
proper installation of both the joining components and insulation materials is vital. This requires skilled technicians who understand the nuances of each material and can apply industry best practices to ensure a secure and efficient system.
Investing in high-quality materials and professional installation might involve an up-front cost, but it yields significant long-term benefits including reduced maintenance costs, improved safety, and enhanced performance of the gas supply system. Additionally, systems designed with energy efficiency in mind contribute to reduced environmental impact, aligning with more sustainable building practices.
In conclusion, the field of gas pipe joining and insulating materials has undergone significant advancements, greatly impacting the safety, efficiency, and sustainability of gas supply systems. By selecting suitable materials and ensuring expert installation, stakeholders can achieve a robust pipeline infrastructure that stands the test of time. With continuous technological innovations and adherence to best practices, the possibilities for increased efficiency and reliability in gas supply systems continue to expand.