Iron powder metallurgy, a facet of material engineering and production that is gaining traction across various industries, is transforming the way manufacturers approach the creation of metal components. This technology not only revolutionizes the methods for producing parts with complex geometries but also ensures cost-efficiency, making it indispensable in today's competitive market landscape.
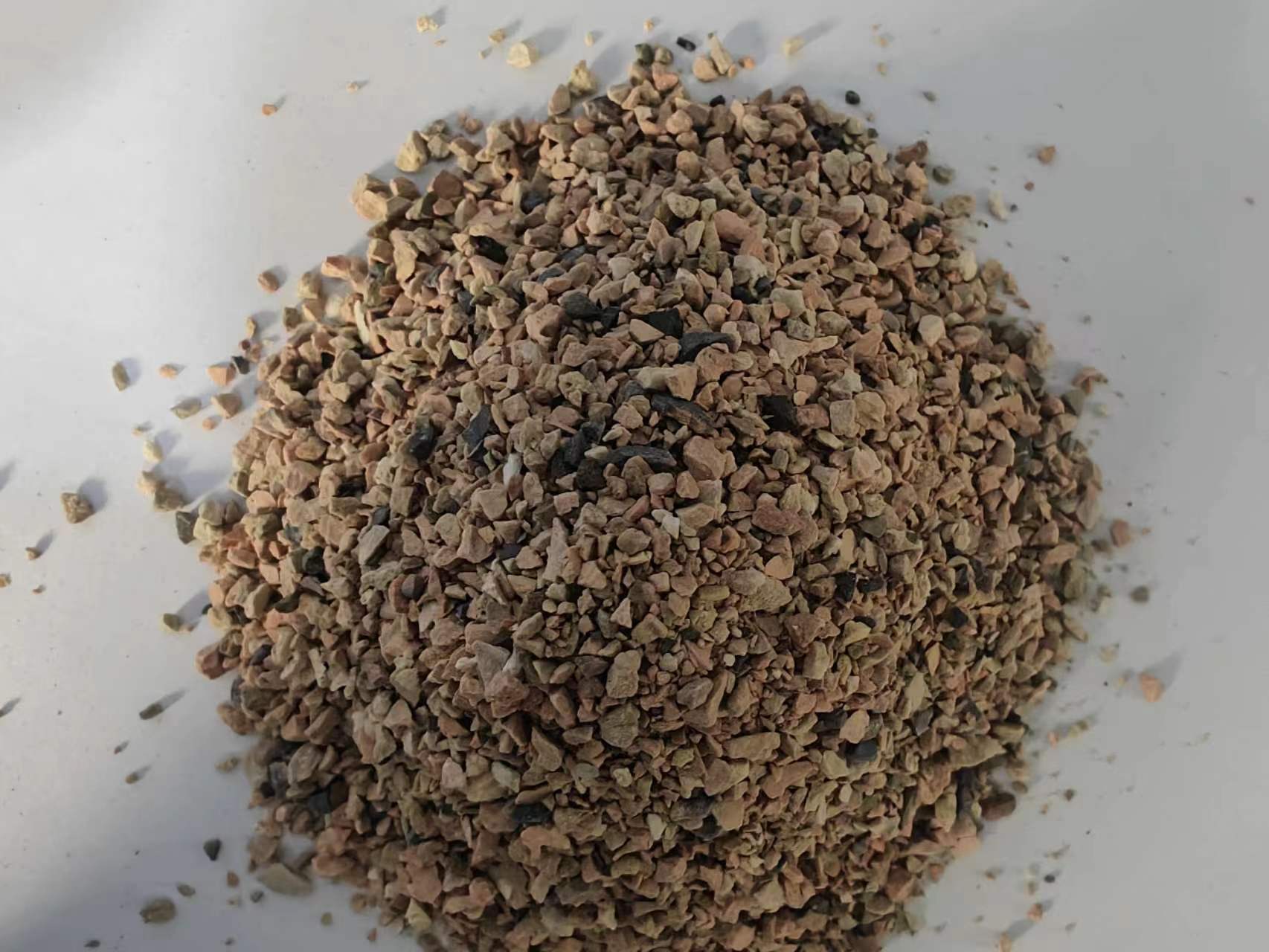
Manufacturing products through iron powder metallurgy involves several intricate processes that highlight its unique advantages. At its core, the process begins with the selection of high-quality iron powder. This powder is the foundation upon which the strength and durability of the final product are based. The consistency and granulation of the iron powder are meticulously controlled to ensure uniformity, which is crucial for the subsequent stages of production.
Once the iron powder is prepared, it proceeds to the compaction stage, where it is placed into dies and subjected to high pressures.
This process effectively transforms the loose powder into a solid yet malleable shape. The dexterity involved in achieving precise shape and density at this stage cannot be understated, as it significantly impacts the performance of the final product. Innovative techniques, such as using lubricants or binders, can enhance the compaction process, allowing for even more intricate designs and improved mechanical properties.
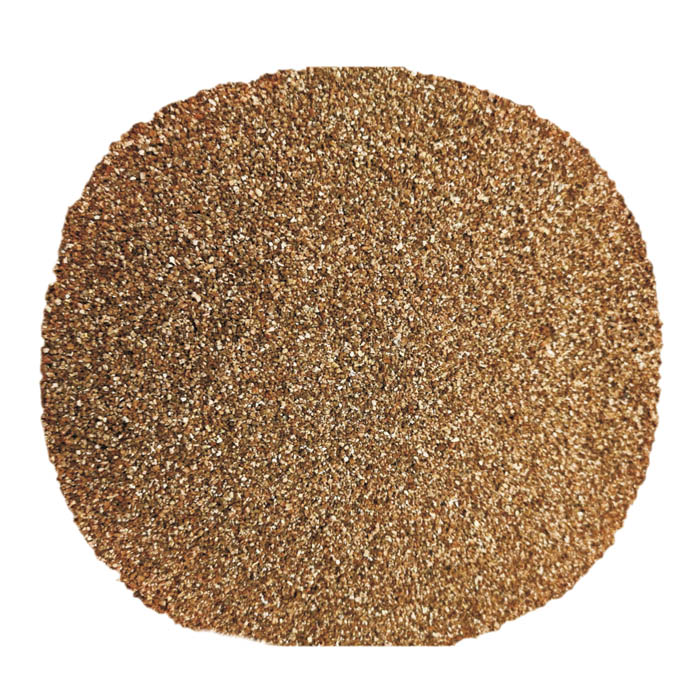
Following compaction, the component undergoes sintering, a thermal treatment that elevates the consolidated powder to temperatures below its melting point. This phase is pivotal as it strengthens the component by forming metallurgical bonds between the particles. The expertise involved in controlling the sintering environment – temperature, atmosphere, and time – is vital for optimizing the mechanical characteristics of the product. Experts often employ cutting-edge technologies like vacuum or inert gas sintering to prevent oxidation and enhance the overall quality of the component.
Iron powder metallurgy is renowned for its ability to produce parts that would be challenging, if not impossible, to mold through traditional metalworking methods. Its application is manifold, ranging from automotive gear parts to medical devices and consumer electronics. Products manufactured using iron powder metallurgy often exhibit superior wear resistance and strength, coupled with lower weights – attributes highly sought after across many industries.
iron powder metallurgy
Companies venturing into iron powder metallurgy benefit from substantial cost savings, primarily due to the minimal waste generated during production. Traditional machining processes typically result in significant material losses, but powder metallurgy utilizes nearly all of the starting material, in keeping with sustainable manufacturing practices. Additionally, the versatility in design provided by powder metallurgy means fewer assembly operations, further reducing production costs.
Trust in products manufactured through iron powder metallurgy is paramount, particularly in sectors where failure is not an option. The reliability of these components has been well-documented, thanks in part to rigorous testing and evaluation procedures. Moreover, collaborations between research institutions and industry players continue to drive innovation, ensuring that the methodologies applied are not only cutting-edge but also of the highest standards of quality and safety.
The field of iron powder metallurgy is continually evolving, with ongoing research aimed at refining existing processes and discovering new alloys with enhanced properties. Material scientists and engineers are at the forefront of these developments, spearheading advancements that promise to expand the capabilities and applications of this manufacturing technique further.
In conclusion, iron powder metallurgy stands as a testament to human ingenuity, merging expertise, experience, and authority in manufacturing and material sciences. Its future looks promising, with innovations poised to make the production of complex, high-performance parts more accessible and reliable than ever before. As industries continue to demand more from materials, the role of iron powder metallurgy in meeting these needs with precision and trustworthiness will undoubtedly grow, offering an unparalleled blend of efficiency and excellence.