Navigating the world of large foundries offers a captivating glimpse into the backbone of modern industrial manufacturing. These colossal establishments are much more than production facilities; they are sophisticated ecosystems where raw materials transform into complex components that drive industries like automotive, aerospace, and construction. Understanding their significance involves delving into aspects such as expertise in metallurgy, cutting-edge technological integration, and an unwavering commitment to quality.
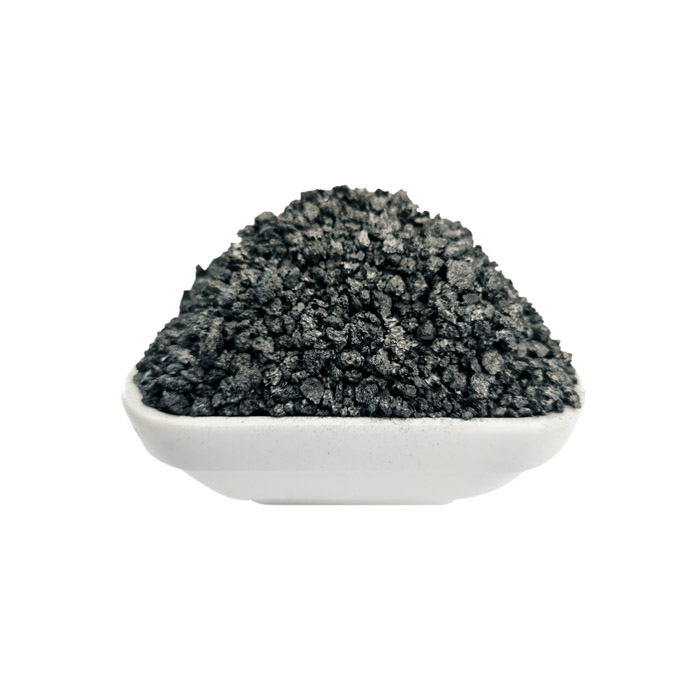
The craft of foundry operations is rooted in the mastery of metallurgy. Expert metallurgists in large foundries skillfully manipulate metal properties to meet specific manufacturing needs, whether it’s the durability required for an aircraft engine or the heat resistance necessary for a construction tool. The expertise in metallurgy is not only foundational but also evolutionary; metallurgists are constantly researching and developing new alloys that can withstand more stress, provide greater longevity, and offer better performance. This level of expertise is indispensable, as it allows foundries to produce high-performing parts that comply with stringent international standards.
In addition, large foundries have become synonymous with technological innovation. The integration of advanced machinery and computer systems ensures precision and efficiency across the board. State-of-the-art equipment such as CNC machines and robotic arms work in synergy, achieving levels of accuracy that manual processes cannot.
The advent of industry 4.0 technologies like IoT and artificial intelligence further propels foundries into the future by automating routine tasks and providing real-time analytics that optimize production cycles. This technological prowess not only enhances output but also minimizes waste, aligning operations more closely with the sustainable practices demanded by modern industries.
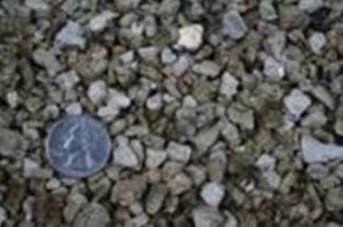
Quality assurance in large foundries is paramount, enveloping the entire production process from start to finish. Rigorous testing protocols are embedded at every stage of manufacturing to ensure conformity to design and functionality requirements. Non-destructive testing techniques, such as X-ray and ultrasound, are routinely employed to detect internal defects without compromising the integrity of the product. This authoritative approach to quality is backed by certifications from leading international bodies, strengthening the trustworthiness of these foundries as reliable suppliers in the global market.
large foundry
Authority in large foundry operations extends beyond internal practices. A commitment to collaboration with clients to tailor solutions that fit unique requirements is essential. This client-centric approach often involves deploying specialized teams that work closely with clients throughout the development process, ensuring that every specification and need is meticulously addressed. Such collaborative partnerships not only ensure the production of bespoke solutions but also establish the foundry as a thought leader in problem-solving and innovation, earning them a place of authority within the industry.
Trustworthiness in foundry operations is also reflected in their environmental stewardship. Large foundries are increasingly adopting eco-friendly practices to minimize their carbon footprint. Through investment in emission control technologies and recycling programs, they strive to reduce their environmental impact. Being proactive in sustainability enhances their reputation amongst environmentally-conscious clients and stakeholders, serving as a testament to their responsibility towards future generations.
In conclusion, large foundries epitomize the convergence of expertise, technological innovation, quality assurance, and environmental responsibility. Their involvement in critical industries makes them indispensable, and their progressive approach ensures they remain at the forefront of industrial evolution. As industries continue to evolve, the role of large foundries will undoubtedly expand, pushing the boundaries of what is possible in manufacturing and setting new standards of excellence globally.