Exploring the Field of LD Steel Making Unlocking New Possibilities
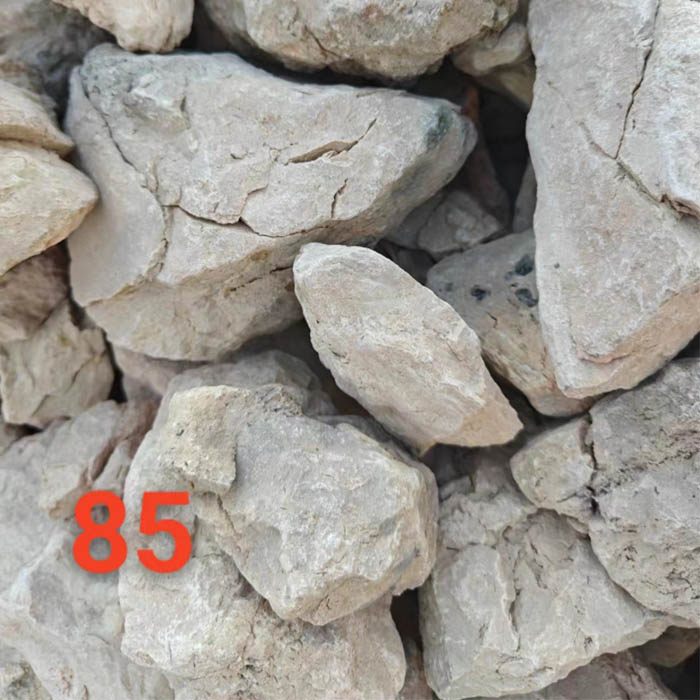
LD steel making, often referred to as basic oxygen steelmaking, represents a cornerstone in the modern steel production landscape. It is an efficient and widely utilized method, primarily due to its cost-effectiveness and ability to produce high-quality steel with enhanced properties. This process revolutionized the steel industry by significantly improving upon earlier methods such as the Bessemer process.
At the core of the LD process is the use of a basic oxygen furnace (BOF), where pure oxygen is blown into molten iron to reduce carbon content and convert raw iron into steel. This transformative approach provides a refined and superior product suitable for various applications, including construction, automotive, and heavy machinery industries.
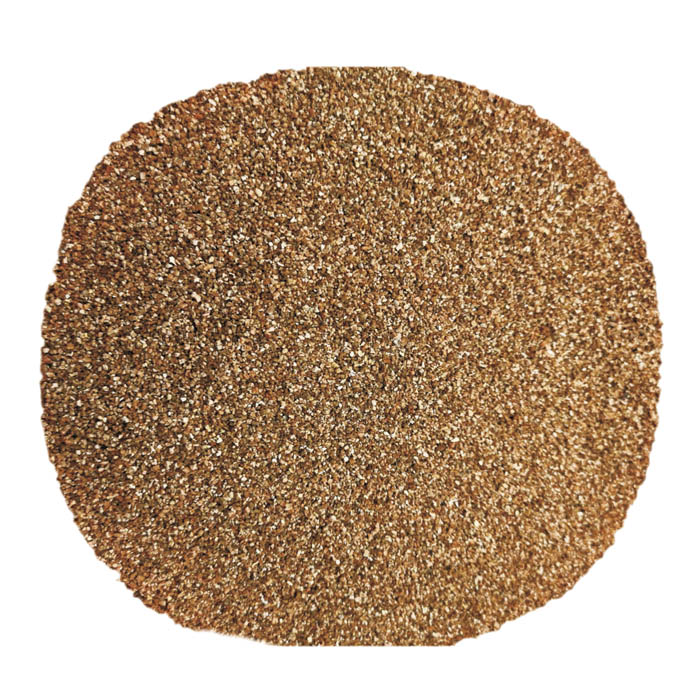
Professionals in the field recognize the unparalleled advantages of LD steel making. Its speed and efficiency outperform traditional methods, allowing the production of large quantities of steel in significantly reduced timeframes. This makes it a preferred choice in industries where meeting high demand is crucial without compromising on quality.
Expert insights reveal that the precision of LD steel making lies in its control over chemical compositions. By tuning variables such as temperature and flow of oxygen, metallurgists can achieve desired chemical properties tailored to specific industrial needs. For instance, alterations in manganese and silicon levels can influence the final steel's tensile strength and ductility, properties critical in manufacturing robust and reliable products.
ld steel making
Authoritative sources emphasize that LD steel making contributes to environmental sustainability. Unlike earlier methods that emitted a considerable amount of pollutants, the LD process minimizes emissions by utilizing pure oxygen rather than air. This commitment to reducing environmental impact aligns with modern industry standards aiming for greener production processes.
Furthermore, advancements in technology have propelled the LD steel process into new territories of innovation. Automation and digital control systems enhance precision, reduce human error, and increase safety within steel plants. Leaders in the industry are investing in these technologies to not only boost efficiency but also ensure that the highest standards of safety and sustainability are maintained.
Real-world experience from industry veterans underscores the strategic importance of ongoing training and development in mastering LD steel making. As technological advancements continue to shape this dynamic field, continuous learning ensures that professionals remain at the forefront of innovation, capable of leveraging new tools and methodologies to maximize production quality and efficiency.
Trustworthiness in LD steel making is reflected in the stringent adherence to international standards. Regulatory compliance ensures products meet rigorous quality and safety benchmarks, providing assurance to clients and stakeholders alike. Reputable steel manufacturers routinely subject their processes to rigorous scrutiny, maintaining transparency and accountability in all operational facets.
In conclusion, LD steel making symbolizes the marriage of tradition and innovation within the steel industry. Its prowess in producing high-quality, sustainable steel positions it as a critical player in fulfilling the demands of modern infrastructure and manufacturing. By incorporating cutting-edge technology, adhering to environmental standards, and maintaining a focus on professional development, the industry not only enhances its output but also fortifies its commitment to excellence and reliability.