Moldable refractory materials represent a significant advancement in industries requiring materials capable of withstanding extreme temperatures and harsh chemical environments. This innovative solution caters to sectors like metallurgy, glass, ceramics, and cement, where high-temperature operations are crucial.
Moldable refractory products not only offer enhanced flexibility and performance but also ensure longevity and efficiency in industrial processes.
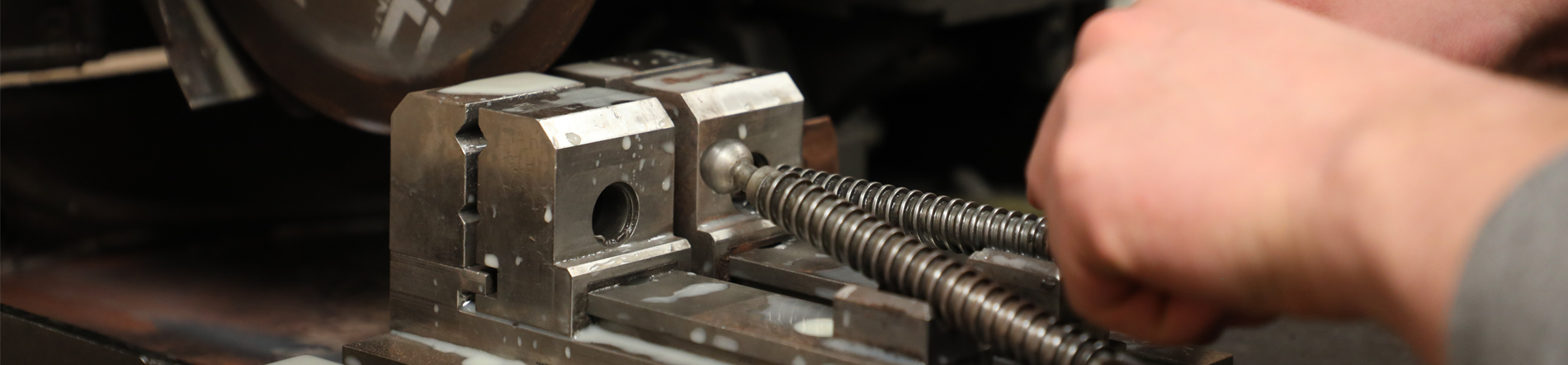
The application of moldable refractory materials is revolutionizing how industries approach high-temperature operations. Unlike traditional refractory bricks and ceramic fiber products, these materials can be shaped and tailored on-site, offering a level of customization that significantly enhances performance. For large industrial furnaces and kilns that operate under strenuous conditions, the adaptability of moldable refractories allows for more precise lining, reducing gaps and inefficiencies that contribute to energy loss and operational downtimes.
Experience in using moldable refractory materials highlights their practicality and effectiveness across various applications. Industrial operators have observed substantial improvements in thermal management, mechanical strength, and resistance to thermal shock. For instance, in the steelmaking industry, the use of these materials in the construction and maintenance of ladles and tundishes enables longer operational periods without failure, which translates into lower maintenance costs and increased production efficiency.
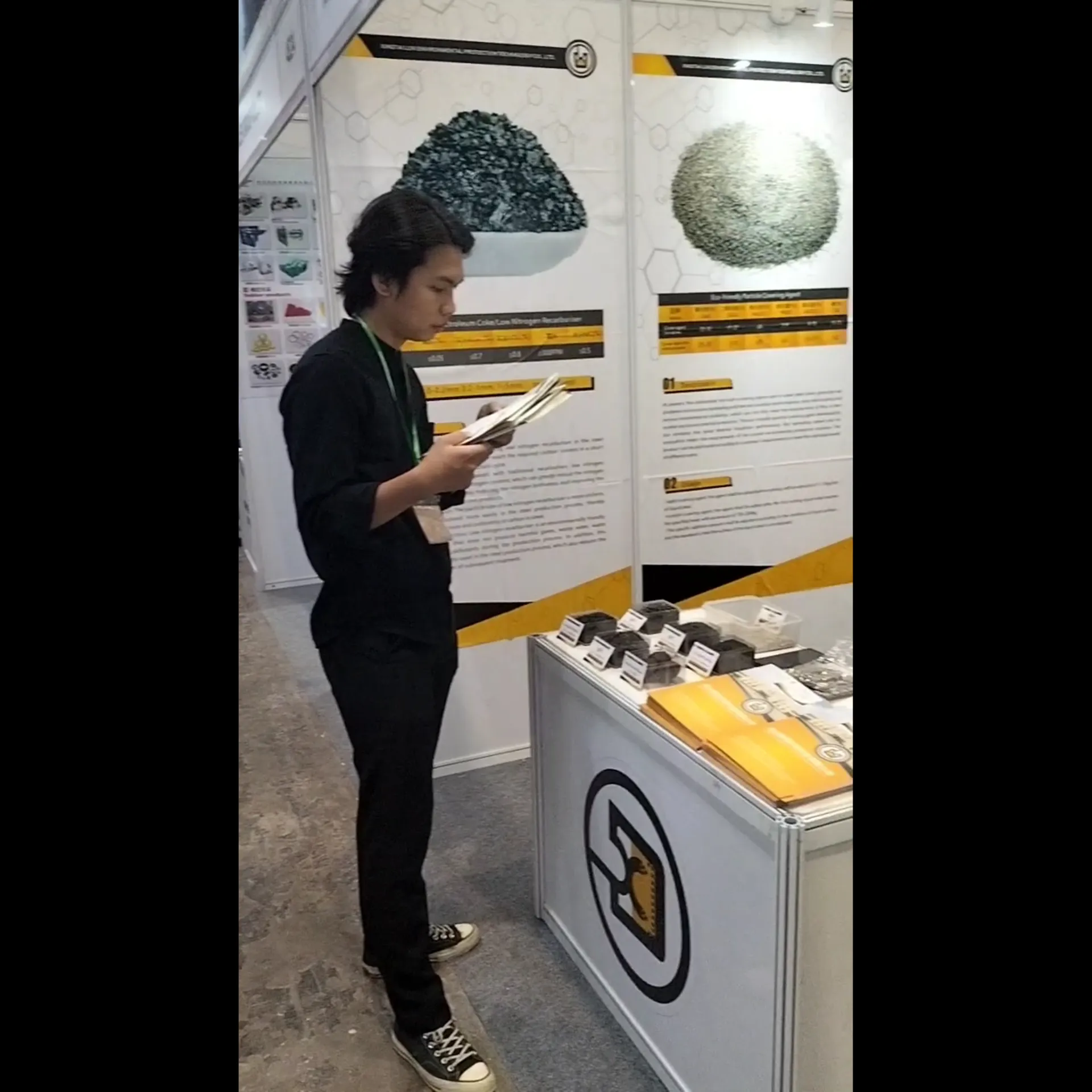
The expertise surrounding moldable refractory materials is supported by ongoing research and development in the field of materials science. Leading manufacturers continually refine their compositions to enhance their properties, such as thermal conductivity, cold crushing strength, and resistance to corrosive slag. This advancement is driven by a deep understanding of high-temperature chemistry and the need to meet the ever-evolving challenges posed by industrial processes.
Authoritativeness in moldable refractory materials is established through rigorous testing and certifications that ensure these products meet international standards. Standards such as ASTM International provide guidelines that help manufacturers produce materials with consistent quality and reliability. Moreover, these standards foster trust among industrial users, who rely on these specifications to ensure that materials possess the requisite durability and performance attributes.
moldable refractory material
Trustworthiness in the deployment of moldable refractory solutions is affirmed through testimonials and case studies from industry leaders who have successfully integrated these materials into their operations. For example, a notable case involved a major glass manufacturer who reported a 25% increase in furnace efficiency after transitioning from traditional refractory lining to a moldable alternative. Positive outcomes such as these create a compelling narrative for the suitability of these materials in various high-stress environments.
The deployment of moldable refractory materials requires knowledgeable professionals who understand how to effectively install and maintain these materials. Proper installation is crucial to maximizing their benefits, which is why partnerships with certified technicians and engineers are essential. Training and certification programs further bolster the industry’s ability to utilize these materials effectively, ensuring that personnel understand the nuances associated with their application.
From a product standpoint, moldable refractory materials contribute to a sustainable industrial future. Their durability and efficiency help reduce energy consumption and minimize environmental impact by extending the lifespan of high-temperature systems. This aligns with global efforts toward sustainability and resource efficiency, making moldable refractories an attractive option for companies looking to enhance their green credentials.
In conclusion, moldable refractory materials offer significant benefits that cater to the dynamic needs of high-temperature industries. Their unique combination of flexibility, durability, and efficiency positions them as a leading solution in the quest for optimal industrial performance. As industrial challenges continue to evolve, so too will the technology behind moldable refractories, ensuring that they remain at the forefront of innovation in material science. By investing in expertise, maintaining authoritative practices, and cultivating trust through evidence-based results, businesses can harness these materials to achieve superior outcomes in their high-temperature applications.