Monolithic refractories play an irreplaceable role in various high-temperature industrial processes. These materials are designed to withstand extreme conditions and serve as the backbone for industries like steel, cement, glass, and non-ferrous metals. But what makes the raw material of monolithic refractories so crucial? Let's delve into the realm of these refractory materials to understand their significance, properties, and selection criteria.
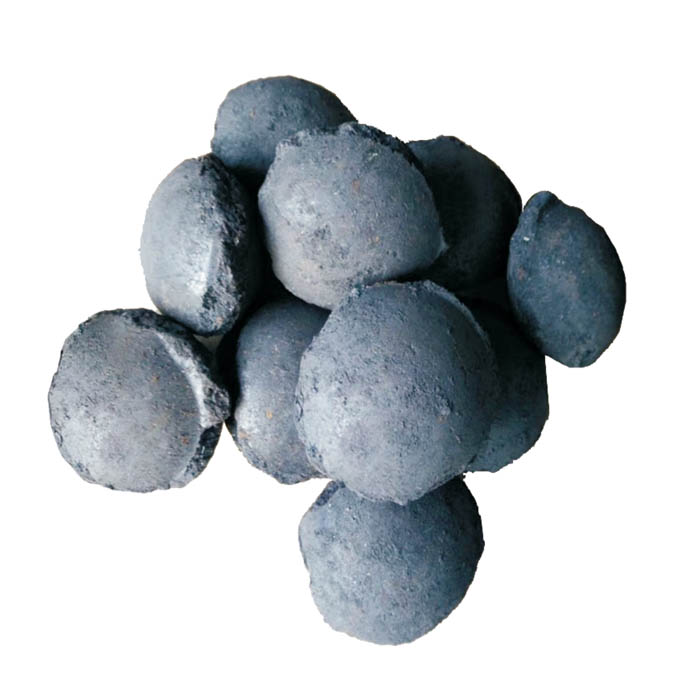
Monolithic refractories, unlike shaped refractories, consist of unshaped materials that incorporate various aggregates and binders to form a solid, homogeneous mass. This category includes castables, plastics, ramming materials, gunning mixes, and patching products. The raw materials' selection is vital to ensure that these refractory products meet the demanding conditions they need to endure.
First and foremost,
the effectiveness of monolithic refractories is driven by the choice of raw materials. The primary ingredients include alumina, silica, magnesium oxide, and calcium aluminate cement. Each of these components brings distinct properties to the table
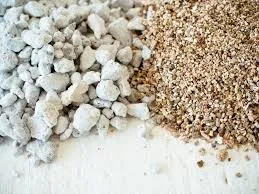
- Alumina Known for its high melting point and excellent insulating properties, alumina is a cornerstone in the formulation of monolithic refractories. It enhances mechanical strength and thermal resistance, making it indispensable for applications subjected to high temperature and corrosive environments.
- Silica Silica's ability to withstand substantial thermal shock is unmatched, making it a favored choice for lining furnaces and kilns. Its insulation characteristics prevent heat loss, which is pivotal for energy conservation in industrial settings.
- Magnesium Oxide (Magnesia) As a refractory component, magnesia excels in offering chemical stability and resistance to basic slag corrosion. This makes it particularly valuable where metal and mineral processing involve basic environments.
- Calcium Aluminate Cement Acting as a binder, calcium aluminate cement enhances the structural integrity of refractories. It is renowned for its rapid hardening properties, crucial for applications needing swift setting to reduce downtime.
monolithic refractories raw material
The process of selecting the right monolithic refractory raw materials goes beyond their inherent properties. Industries must consider factors like thermal expansion, which could lead to structural damage if not managed properly. Moreover, the thermal conductivity, chemical compatibility, and abrasion resistance of these materials determine their suitability for specific industrial applications.
Industries need to conduct a rigorous evaluation of the operational conditions that the refractories will be exposed to. This includes assessing factors like the target operating temperature range, the mechanical stresses involved, and potential chemical interactions. By understanding these parameters, one can tailor the composition of raw materials to optimize performance.
Innovation in raw material technology has propelled advancements in monolithic refractory performance. Recent developments have focused on refining material purity, enhancing phase composition control, and optimizing grain size distribution. These improvements contribute to prolonged service life, reduced maintenance costs, and improved energy efficiency, reinforcing the inherent advantages of monolithic refractories.
Safety and environmental considerations are also paramount. Adopting eco-friendly raw materials that adhere to global safety standards is essential. This not only minimizes environmental impact but also ensures compliance with industry regulations, bolstering the trust and credibility of the products.
In addition, the installation and maintenance of monolithic refractories heavily rely on the expertise of specialists. Installation methods such as casting, ramming, and gunning require precision to achieve optimal performance. Regular maintenance practices like thorough inspections and timely repairs should be employed to extend the lifespan of refractory linings.
In conclusion, the raw materials used in monolithic refractories are the unsung heroes that ensure the durability, efficiency, and safety of high-temperature industrial applications. With the advancement in material technology and a focus on sustainability, these refractories continue to evolve, promising a future of enhanced performance and reduced environmental impact. The choice and management of these materials necessitate a blend of experience, expertise, authority, and trustworthiness — qualities that industries must prioritize to sustain their operations in the long run.