Neutral refractory materials are a critical component in industries requiring high resistance to thermal, chemical,
and mechanical degradation. Over the years, advancements in material science have profoundly influenced their development, resulting in products that not only withstand extreme operating conditions but also enhance energy efficiency and longevity in industrial applications.
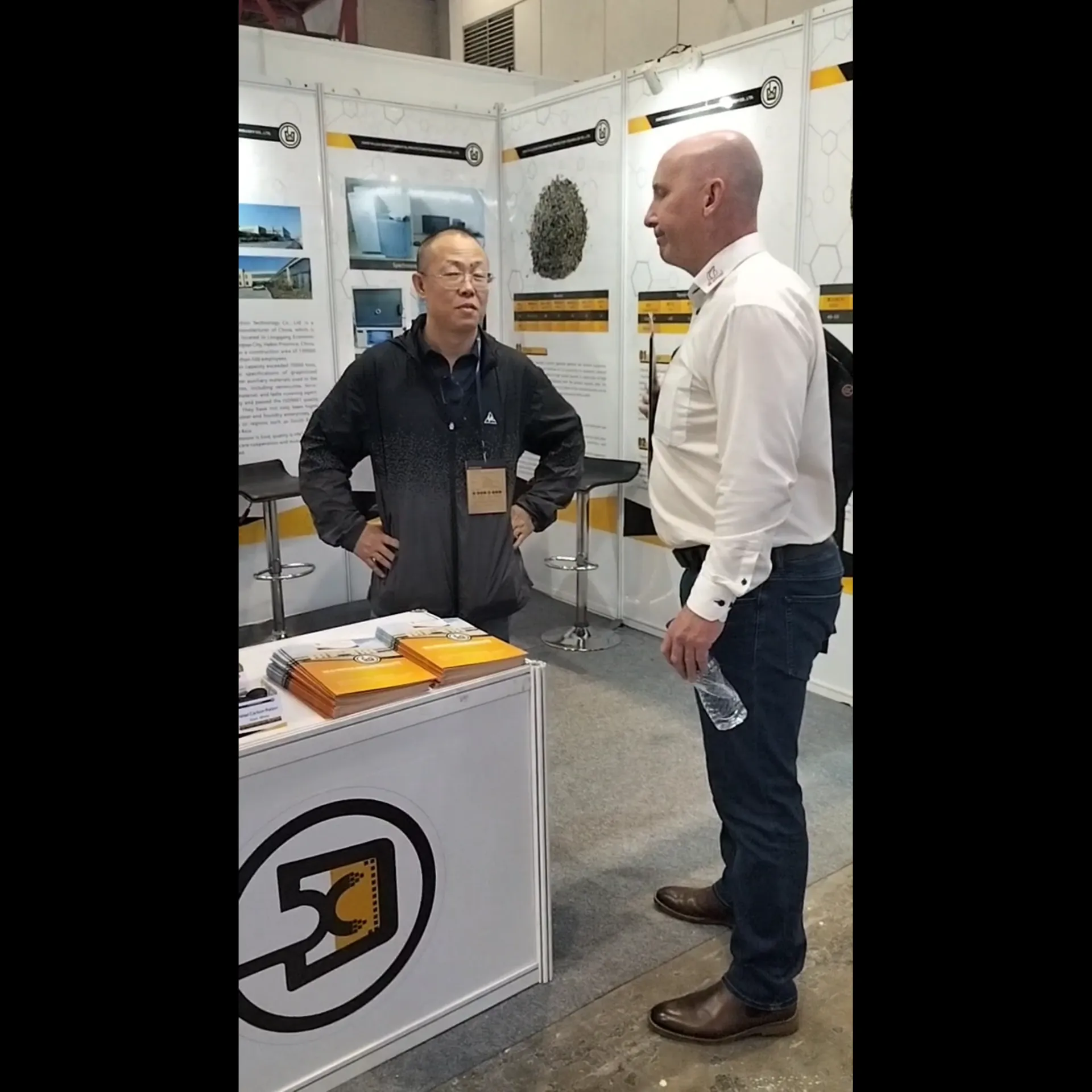
A brief examination of neutral refractory materials reveals their unique properties that make them indispensable in sectors such as steel, cement, and glass production. Typically comprised of alumina, chromia, or a combination of the two, these materials exhibit neutrality when exposed to both acidic and basic slags, ensuring minimal reaction during use. This stability under different chemical environments significantly impacts the efficiency and safety of industrial processes.
Real-world applications underscore the critical nature of neutral refractory materials. In the steel industry, for example, advancements have led to the development of high-purity alumina-based refractories. These materials extend the life of industrial furnaces by reducing wear from metallic oxides and other contaminants. By offering an enhanced resistance to slag penetration and spalling, these refined materials ensure that steel production facilities experience fewer downtimes and maintenance costs, ultimately leading to increased productivity and cost-efficiency.
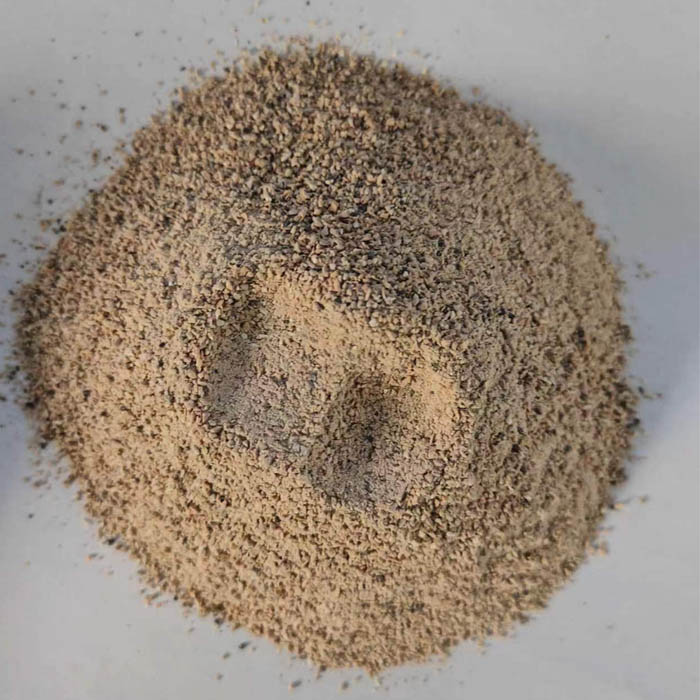
Expertise in this field not only comes from material development but also from understanding the specific requirements of different industrial applications. For instance, in cement production, kilns and preheaters benefit from specially formulated refractory linings that combat alkali attacks. Neutral refractory products designed for this application must embody not just chemical resilience but also excellent thermal insulation properties to maintain optimal energy use. Industry experts engage in continuous feedback loops with production facilities to innovate and tweak formulations to meet these evolving needs, thus demonstrating a high level of professionalism and adaptive expertise.
neutral refractory material
Authoritative knowledge is essential in the production and application of neutral refractory materials. Manufacturers and suppliers are increasingly adopting stringent quality control standards, often adhering to globally recognized certifications such as ISO 9001. This commitment to quality not only fosters trust among consumers but also establishes manufacturers as authorities in the industry. Consultations with industrial engineers and operations managers further aid in tailoring refractory solutions that align with best practices and operational goals, reflecting an authoritative approach to fulfilling industrial requirements.
In maintaining trustworthiness, transparent practices in sourcing, manufacturing, and product distribution are key. Suppliers who openly share information about the origins of their raw materials and the processes involved in their manufacturing set a benchmark for accountability in the market. Engaging regularly with clients through technical support services and offering educational insights into material handling and application techniques also reinforces reliability and builds long-lasting relationships. Trust is further built by offering extended warranties or guarantees on refractory products, which signals confidence in their durability and performance.
As we advance, the role of technology cannot be underestimated in the realm of neutral refractory materials. State-of-the-art simulation tools enable material engineers to predict the behavior of refractory linings under various operational stresses, facilitating designs that maximize efficiency and safety. Furthermore, developments in nanotechnology pave the way for refractories with superior mechanical properties and reduced environmental footprints. As sustainability becomes a central concern, the potential to recycle and reuse materials without compromising quality remains a priority in ongoing research and development efforts.
In conclusion, neutral refractory materials play a quintessential role across various high-temperature industries, necessitating a balanced approach that integrates experiential learning, scientific expertise, authoritative standards, and reaffirmed trust. Manufacturers and users alike must continue to innovate and collaborate to push the boundaries of what's possible in refractory technology, ensuring that industries not only meet their production goals but also adhere to sustainable and economically sound practices.