Packing graphite, a material renowned for its remarkable versatility and efficiency, stands as a cornerstone in various industrial applications. This article delves into the manifold benefits and applications of packing graphite, drawing from real-world experiences and the latest expert insights, ensuring that readers receive unique and authoritative content that fosters trust and clarity.
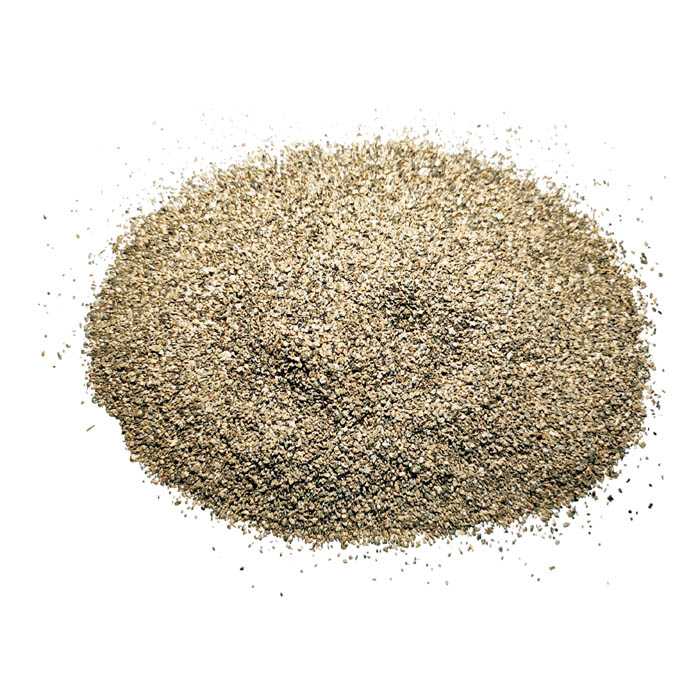
In industrial environments where sealing is critical, packing graphite emerges as an indispensable solution. Its ability to withstand extreme temperatures and pressures makes it an ideal choice for many demanding applications. In sectors such as petrochemicals, power generation, and manufacturing, equipment often operates under harsh conditions. Here, packing graphite ensures reliable sealing, preventing leaks that could lead to costly downtime or hazardous conditions.
Renowned for its flexibility and resilience, packing graphite adeptly navigates the challenges posed by thermal cycling. Unlike many materials, it maintains its integrity and performance despite continuous expansion and contraction. This property not only extends the lifespan of the packing itself but also contributes to the longevity of the equipment it supports. Thus, from an economic perspective, investing in packing graphite translates into significant savings over time, reducing maintenance costs and enhancing operational efficiency.
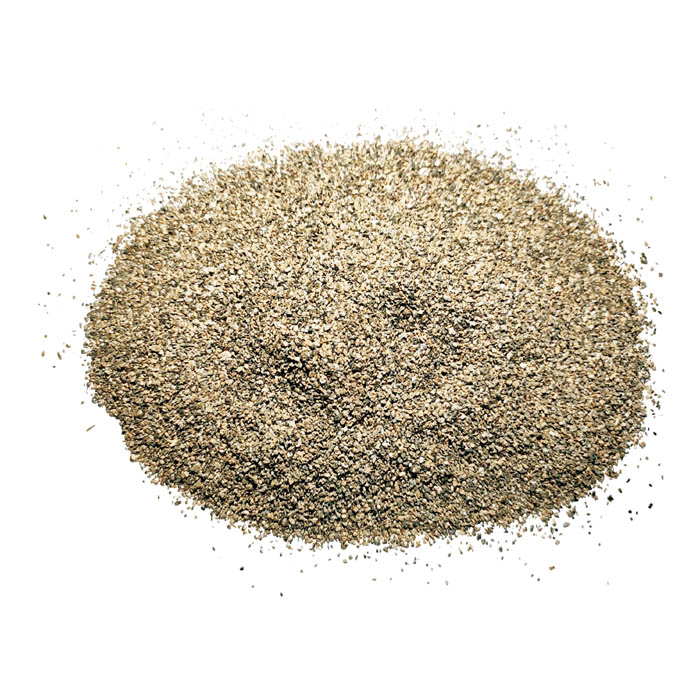
Industry experts often highlight the adaptability of graphite packing materials. These materials can be blended with other substances, such as PTFE or aramid fibers, to enhance specific properties such as chemical resistance or mechanical strength. This flexibility enables fine-tuning to meet the unique demands of various processes and environments, demonstrating the material's expert engineering and suitability for diverse applications.
The authority of packing graphite in industrial sealing applications is further validated by numerous case studies and field reports. For instance, it has been utilized successfully in refineries dealing with aggressive media, where conventional materials might fail. Such real-world applications underscore its reliability and effectiveness, cementing its status as a trusted material in critical applications.
packing graphite
The choice of packing graphite is often complemented by its inherent corrosion resistance, which contributes significantly to its trustworthiness in corrosive environments. It acts as a shield against chemical attack, ensuring that sealing solutions preserve their efficacy even in the presence of volatile substances. This property is particularly invaluable in chemical processing plants, where leaks could result in severe safety hazards or product contamination.
Noteworthy is the environmental impact of packing graphite, or rather, the lack thereof. As industries increasingly prioritize sustainability, the environmentally neutral nature of graphite becomes a major advantage. Its non-toxic composition and the fact that it does not emit harmful substances during use align with both environmental regulations and the corporate responsibility goals of forward-thinking companies.
Furthermore, advancements in the processing of graphite packing materials have resulted in enhanced performance characteristics, such as improved purity and consistency in product quality. This dedication to innovation ensures that packing graphite remains at the forefront of sealing technology, offering unparalleled reliability and performance.
In conclusion, packing graphite's widespread adoption in industrial applications is a testament to its unmatched attributes of durability, adaptability, and safety. As industries evolve, the demand for high-performance, cost-effective, and eco-conscious solutions drives the continuous development and refinement of graphite packing products. Engaging with this material not only leverages its proven capabilities but also aligns with a forward-looking, resilient approach to industrial challenges. Such qualities ensure that packing graphite stands as a premier choice in sealing technology—one that industries can rely upon to safeguard their operations and propel their advancement into a sustainable future.