Precast refractory materials have revolutionized industries that rely on high-temperature processes, such as steel manufacturing, cement production, and petrochemical industries. Their innovative design and application not only enhance performance but also contribute significantly to process efficiency and energy savings. Understanding the intricacies of these materials, alongside their benefits and applications, is key to fully leveraging their capabilities in industrial processes.
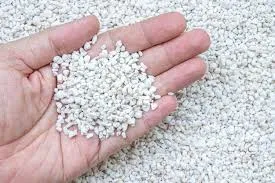
Precast refractory materials are engineered for extreme temperature conditions, offering both durability and versatility. These materials are pre-molded into specific shapes before installation, an advancement over traditional refractories that require labor-intensive on-site application. This shift towards pre-molded solutions is driven by the need for quick turnaround times, precision, and consistent quality in demanding industrial environments.
One key advantage of precast refractory products is their tailor-made nature. Each unit can be customized for a specific application, ensuring optimal performance. Customization involves engineering specific shapes and sizes, as well as selecting the most suitable materials based on the anticipated thermal and mechanical stresses. Such thorough design minimizes the risk of premature failure, reducing downtime and maintenance costs significantly.
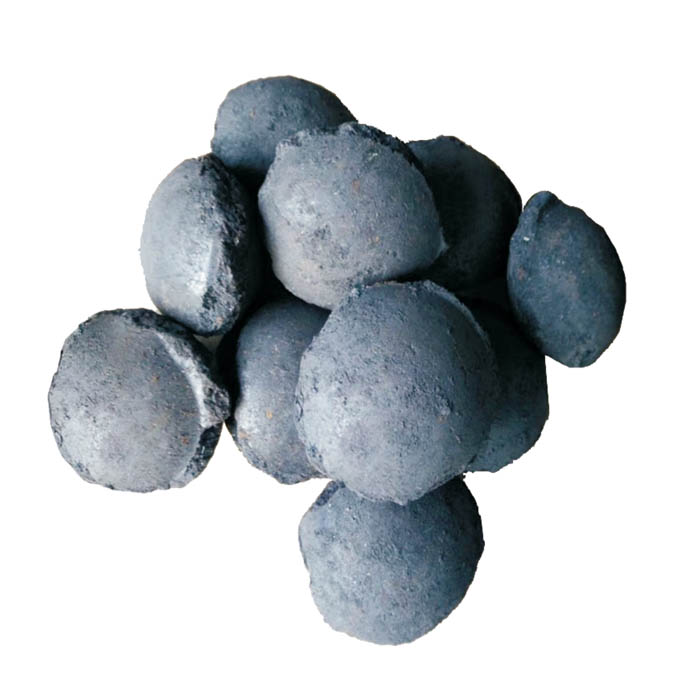
The expertise involved in crafting precast refractories cannot be overstated. It requires a deep understanding of material science, thermodynamics, and industrial engineering. Manufacturers use advanced techniques like computer-aided design (CAD) and finite element analysis (FEA) to simulate and optimize the performance of these materials in real-world conditions. Additionally, the use of modern sintering and casting technologies ensures the highest quality standards, enhancing the physical properties of the refractories like strength, corrosion resistance, and thermal stability.
Furthermore, the installation of precast refractory materials is a testament to their authority in the industrial sector. They are integral to optimizing operational efficiency and productivity. By reducing the installation time compared to traditional refractories, production facilities experience less downtime. The quick and straightforward installation process comprises aligning and securing the shapes with precision fittings and minimal jointing materials, ensuring that the structural integrity and insulation properties are uncompromised.
precast refractory material
Trustworthiness in the use of precast refractory materials is cemented through years of successful applications and continuous improvement. Leading manufacturers conduct rigorous quality control tests, including high-temperature cycling, compressive strength, and erosion assessments, to guarantee performance under all operating conditions. Moreover, long-term partnerships with industry leaders provide evidence of reliable performance, while detailed failure analysis and feedback loops drive innovation.
Cutting-edge developments in precast refractory materials include the incorporation of advanced ceramic and composite materials, which provide enhanced thermal insulation and mechanical strength. The integration of features such as complex geometries for improved heat distribution and reduced thermal loss has led to significant energy savings in high-temperature processes.
Additionally, sustainability is a growing focus within the industry. Efforts to reduce carbon footprints have seen precast refractories being engineered with recyclable components and environmentally-friendly production techniques. This not only meets regulatory requirements but also aligns with global sustainability initiatives.
In conclusion, the application of precast refractory materials is pivotal to the advancement of industries reliant on high-temperature processes. Their precision-engineering, efficiency in installation, and durable performance ensure their status as a staple in industrial applications. Manufacturers and industries alike benefit from the elevated performance, energy efficiency, and reliability that these advanced materials bring, thereby solidifying their place as an indispensable component of modern industrial operations. To fully capitalize on their potential, investing in expert design and careful application is essential, promoting sustainable and efficient industrial practices globally.