Reduced iron powder, an elemental powerhouse in various industrial applications, remains an essential commodity rooted in intricate processing techniques that ensure its vast utility. Its role extends from metal production to chemical synthesis, showcasing unparalleled versatility that can be a game-changer in specialized fields.
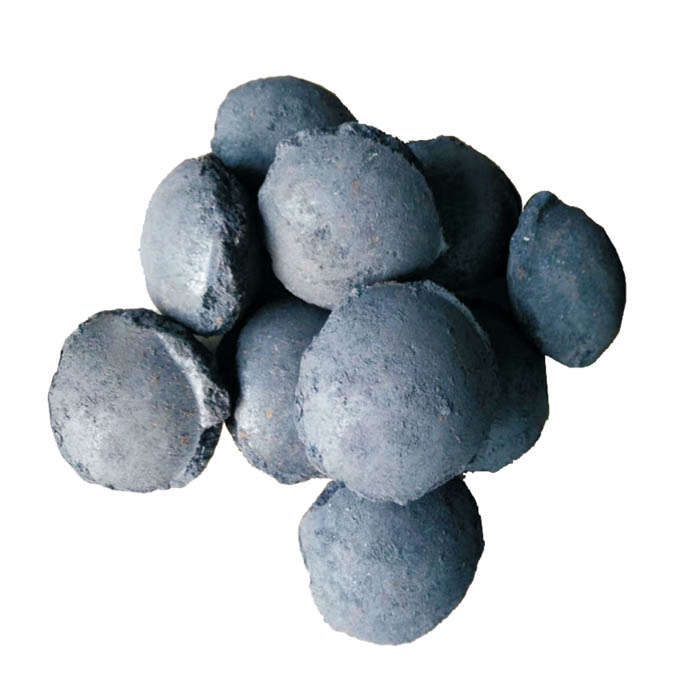
Understanding the production of reduced iron powder requires a deep dive into its manufacturing intricacies.
Typically derived from high-grade iron ores, the process begins with the meticulous reduction of iron oxide using solid or gaseous reductants. Through controlled environments of high temperatures and calibrated pressure, impurities are minimized, providing a premium quality product with consistent chemical properties. This foundational process transforms raw materials into a malleable and reactive powder ideal for further use.
Expertise in utilizing reduced iron powder can greatly enhance productivity and efficiency across multiple domains. In the realm of metallurgy, it serves as a core material for powder metallurgy, facilitating the production of components with complex geometries and exceptional mechanical properties. The high purity and uniform particle size distribution of reduced iron powder enable manufacturers to achieve desired densities and microstructures for products like gears, bearings, and magnetic materials, which demand precision and durability.
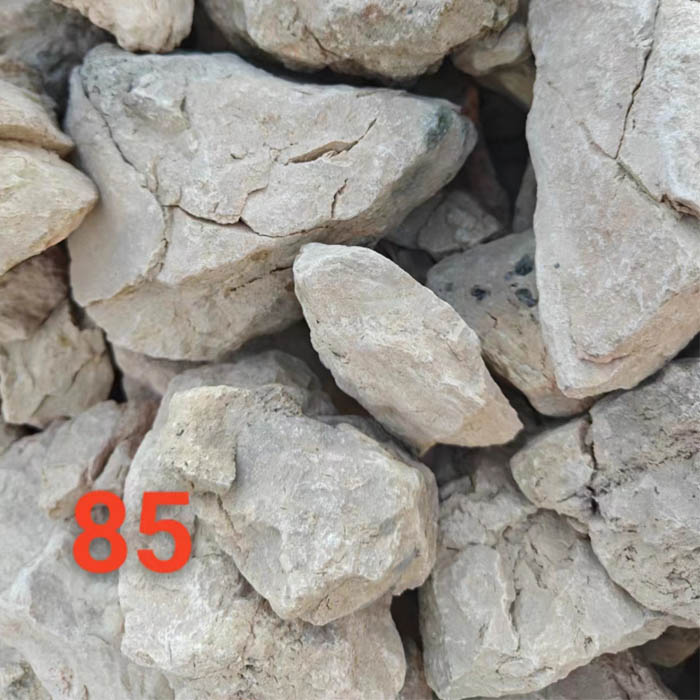
In the chemical industry, the catalytic properties of reduced iron powder are harnessed for various synthesis reactions. Its ability to serve as a catalyst in water-gas shift reactions and ammonia production showcases its chemical reactivity and reliability. Moreover, reduced iron powder's role in environmental applications, such as soil remediation and water treatment, underlines its significance as a sustainable solution provider, aiding in breaking down contaminants and promoting eco-friendly practices.
reduced iron powder
The authoritative edge of reduced iron powder lies in its adaptability to modern technological advancements. As industries lean towards greener and more efficient processes, reduced iron powder's recyclable nature and minimal waste generation support this transition. Its integration into additive manufacturing technology, commonly known as 3D printing, marks an evolution in production capabilities, allowing the creation of highly bespoke and adaptive designs that meet the growing demand for customization and rapid prototyping.
Trust in reduced iron powder is cemented by robust quality control standards and certifications. Reputable suppliers ensure adherence to stringent quality measures, providing end-users with materials that conform to international benchmarks. This reliability translates into consistent performance in application, minimizing operational risks and ensuring compliance with safety and environmental regulations.
The future of reduced iron powder appears promising as innovation continues to unlock new applications. Researchers and industry professionals are exploring its potential in emerging technologies such as energy storage systems, where its responsive characteristics could play a pivotal role in enhancing battery performance and efficiency. This continual exploration of capabilities aligns with global sustainability goals, reinforcing reduced iron powder's position as a cornerstone material in advancing industrial progress.
In conclusion, reduced iron powder's comprehensive benefits span expertise in application, authoritative adaptability, and trustworthy consistency, shaping its indispensable presence in diverse sectors. As industries evolve, so too will the utilization of this dynamic material, fostering advancements that align with both economic aspirations and environmental stewardship.