Refractory gasket materials are essential components in high-temperature and high-pressure industrial applications. Choosing the right refractory gasket material is crucial for maintaining operational efficiency, safety, and equipment longevity. This comprehensive guide delves into the properties, applications, and advancements in refractory gasket materials, providing real-world insights into their selection and use.
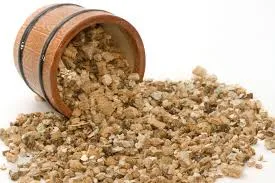
Refractory gasket materials are designed to withstand extreme conditions without degrading or losing their sealing properties. These materials are commonly used in industries such as power generation, petrochemicals, steel manufacturing, and aerospace, where they encounter intense heat, corrosive substances, and mechanical stress. The ideal refractory gasket material should offer exceptional thermal resistance, chemical compatibility, mechanical strength, and durability.
The evolution of refractory gasket materials has been driven by advancements in material science and the increasing demands of various industries. Traditional materials like asbestos have been largely phased out in favor of safer, more efficient alternatives due to health concerns. Modern refractory materials include graphite, ceramic fiber, mica, and high-performance polymers, each offering distinct advantages.
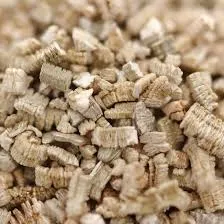
Graphite is a popular choice for high-temperature applications due to its excellent thermal conductivity and chemical resistance. It is particularly suitable for applications involving steam, hot oils, and gases. Furthermore, graphite gaskets are known for their flexibility, allowing them to create a reliable seal even in systems experiencing thermal expansion and contraction.
Ceramic fiber gaskets are another outstanding option, especially in environments where thermal insulation is critical. These gaskets can withstand temperatures exceeding 1000°C and are often used in furnaces, kilns, and other high-temperature processing equipment. The lightweight nature and low thermal conductivity of ceramic fibers enhance energy efficiency by reducing heat loss.
Mica-based gasket materials offer a unique combination of properties. With excellent dielectric strength, thermal resistance, and chemical stability, mica gaskets are favored in electrical and thermal insulation applications. Additionally, their ability to maintain integrity under intense thermal cycling makes them indispensable in specific high-demand scenarios.
refractory gasket material
High-performance polymer gaskets, such as PTFE and PEEK, are engineered to provide chemical resistance and mechanical strength at elevated temperatures. These materials are often employed in chemical processing and pharmaceutical industries, where both purity and performance are critical.
Selecting the appropriate refractory gasket material involves a thorough understanding of the operational environment and application requirements. Factors to consider include temperature range, pressure, chemical exposure, mechanical stress, and the potential for thermal cycling. Consulting with industry experts and manufacturers can provide invaluable insights into material performance and suitability for specific applications.
In recent years, innovation has focused on enhancing the performance of refractory gasket materials through composite technologies and advanced manufacturing processes. These advancements aim to improve material uniformity, reduce defects, and extend service life, thereby offering cost-effective solutions for challenging industrial environments.
Trustworthiness in selecting refractory gasket materials stems from sourcing from reputable manufacturers known for quality and reliability. Certification and compliance with industry standards, such as ASTM and API, further assure the suitability of materials for intended applications. Moreover, thorough testing and validation under simulated service conditions can provide additional confidence in material performance.
To harness the full potential of refractory gasket materials, companies must prioritize regular maintenance and inspection schedules. Early detection of wear, corrosion, or deterioration can prevent costly failures and unscheduled downtime. Implementing predictive maintenance strategies, assisted by digital monitoring technologies, can enhance operational efficiency and extend the lifespan of gasket materials.
In conclusion, refractory gasket materials are indispensable in countless industrial applications, providing vital sealing solutions in extreme environments. Understanding the properties and capabilities of various materials enables industries to make informed decisions, optimizing safety, performance, and cost-effectiveness. As technology continues to advance, the development of more resilient and adaptable gasket materials will undoubtedly meet the evolving demands of modern industry, ensuring reliability and trust in their utilization.