Refractory patching material is a critical component extensively used in industries where high temperatures and harsh conditions are the norms. These conditions push standard materials beyond their limits, making refractory solutions invaluable for maintaining the integrity and efficiency of industrial processes.
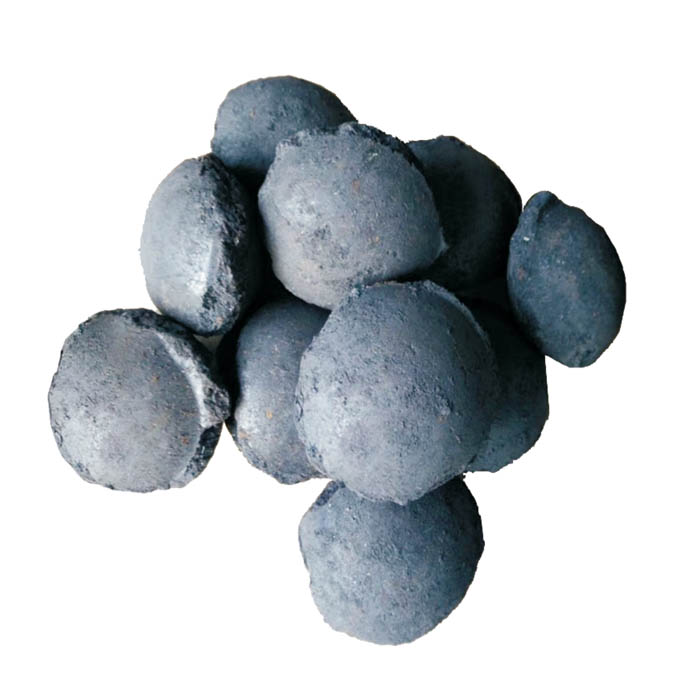
Manufacturers and industries looking for ways to enhance their operational resilience will find refractory patching materials indispensable. These materials are specifically engineered to withstand extreme conditions, such as the intense heat and chemical environments typical in kilns, furnaces, and boilers. The advanced composition of refractory materials provides the optimal balance of thermal stability and durability, allowing them to withstand temperatures that often exceed 1000°C.
What sets apart superior refractory patching materials is their composition. They usually consist of a blend of ingredients like alumina, silica, magnesium oxide, and zirconia, carefully chosen for their heat-resisting properties. This blend is crucial not just for thermal resistance but also for the material’s ability to undergo rapid temperature changes without cracking—a property known as thermal shock resistance. The ability of refractory materials to handle such stresses ensures minimal downtime and maintenance in industrial settings, saving both time and resources.
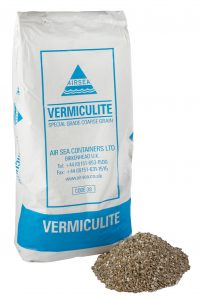
From expert reviews and field applications, refractory patching materials demonstrate phenomenal adherence to existing structures, proving essential in maintaining long-term operational stability. Their ease of application makes them a favorite in various industrial settings, allowing for quick repairs without the need for specialized tools or extensive downtime. This ease of use, combined with their robust performance, underlines their importance in maintaining the infrastructural health of thermal systems.
When choosing refractory patching materials, it is crucial to consider the specific conditions they will face. For instance, environments exposed to acidic or basic slags will demand specific compositions to resist chemical corrosion. Thus, selecting the right type of patching material involves understanding both the operational environment and the unique properties of the available materials.
refractory patching material
Industry professionals emphasize the importance of expertise in both the selection and application of refractory materials. Consulting with material scientists and industry experts can lead to better-informed decisions, ensuring that the materials used are optimal for the specific heat and chemical conditions in play. This tailored approach results in enhanced durability and efficacy, reducing the frequency of repairs and extending the lifespan of industrial assets.
Moreover, manufacturers are constantly innovating, driving forward improvements and adaptations in refractory materials to meet more demanding industrial requirements. Recent advancements include the development of nanotechnology-enhanced refractories, which promise even greater resistance to thermal and mechanical stress. These innovations highlight the dynamic nature of the refractory material sector, constantly evolving to support industrial growth and sustainability through improved efficiencies and cost-reduction.
For industries investing in high-quality refractory patching materials, the benefits include not only better protection of their high-temperature operations but also the assurance of reduced frequency of halts and breakages. This reliability significantly impacts the bottom line by enhancing productivity and reducing unforeseen expenses associated with equipment failure.
Overall, purchasing refractory patching materials from a reputable supplier ensures authenticity and quality. Trustworthy suppliers have a proven track record, provide essential technical support, and share invaluable expertise—an indispensable component when dealing with complex industrial requirements.
Thus, refractory patching materials stand as a testament to human ingenuity, enabling industries to reach new heights of operational efficiency and resilience, thereby cementing their place as a critical element of modern industrial infrastructure.