When delving into the world of automotive enhancements and acoustic engineering, sound absorbing materials have emerged as essential players in both fields. This dual focus is especially apparent when examining their application in dynamometers, often referred to as dynos. These devices, vital to performance tuning and testing, generate significant noise levels during operation. Integrating sound absorbing materials in these settings not only enhances the auditory environment but also boosts overall performance metrics.
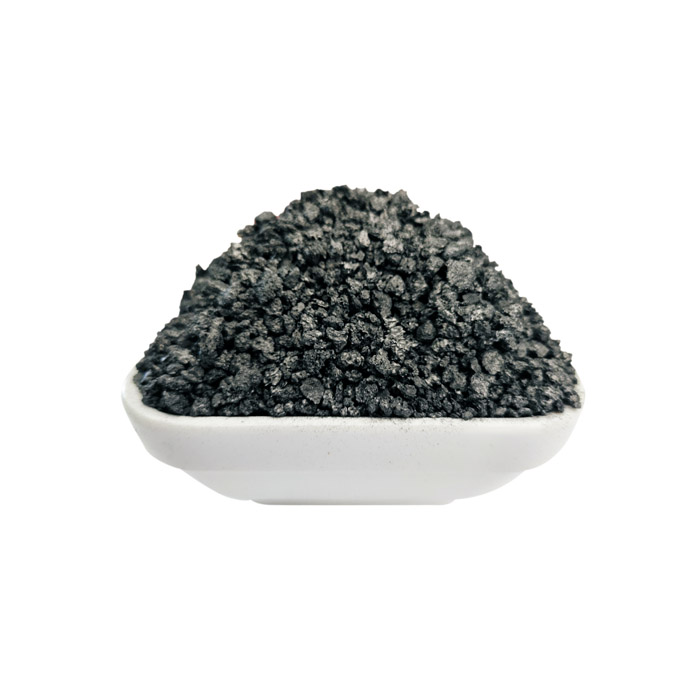
Sound absorbing materials utilized in dynos are sophisticated composites designed with a focus on fidelity and precision. Their ability to mitigate noise extends from a deep understanding of both material science and the complex sound profiles produced by high-performance engines. The essence of these materials lies in their porous structure, which effectively captures and dissipates sound waves rather than reflecting them. This mechanism is paramount in creating an environment that allows for clearer acoustic analyses and communication during testing.
The expertise behind developing these sound absorbing materials is grounded in acoustic technology advancements. Engineers and specialists draw from years of research in sound dynamics to create products that meet the stringent demands of a dyno environment. Companies leading this innovation have access to state-of-the-art testing facilities where every layer of their product can be meticulously examined for efficiency and durability, ensuring that their materials maintain performance even in the most rigorous conditions.
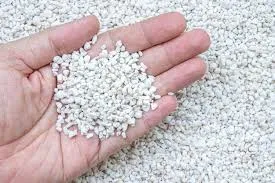
These materials offer unyielding authoritativeness in their functionality. Their application is not limited to sound absorption alone; they play a significant role in temperature regulation within the testing facility and often contribute to improved engine performance by reducing acoustic interference. By minimizing reverberations, sound absorbing materials prevent false readings and enhance the accuracy of data collection, which is crucial for precise engine tuning and benchmarking.
The trusted names in this niche often come equipped with credentials that substantiate their know-how, backed by certifications and customer testimonials. Such endorsements are integral components of their brand’s trustworthiness. They provide clients with certainty, knowing that the products have been vetted and approved by industry standards. This trust extends beyond the products themselves to the brands that manufacture them, many of which maintain longstanding relationships with automotive giants and professional racing teams.
sound absorbing material dyno
Employing sound absorbing materials in dyno setups is not merely about sound reduction; it is about creating an optimized environment for superior performance and accurate diagnostics. Their use translates to enhanced testing integrity, offering clearer insights and better-informed decisions when fine-tuning engines for maximum output and efficiency.
The tangible benefits provided by these materials manifest in various performance metrics. Users often report noticeable decreases in ambient noise levels, leading to reduced operator fatigue and enhanced communication efficiency during testing sessions. Moreover, the quality data gathered in such controlled acoustic conditions can lead to improved engine modifications and innovations.
Last, considering safety, these materials also contribute substantially by diminishing the risk associated with prolonged exposure to high noise levels, ensuring that those working in or near dynos experience a comfortable and secure environment. This multifaceted approach exemplifies the modern dynamometer's pivotal role in automotive engineering, where precision and performance enhancement intersect with sound management.
Ultimately, sound absorbing materials are indispensable in dyno applications, offering unmatched acoustic control, data accuracy, and operational efficiency. They reflect the ongoing pursuit of perfection within the automotive industry, standing as testament to the power of engineering excellence and innovative material application. Through their integration, dynos not only validate performance but also redefine the boundaries of what is possible in engine testing and development.